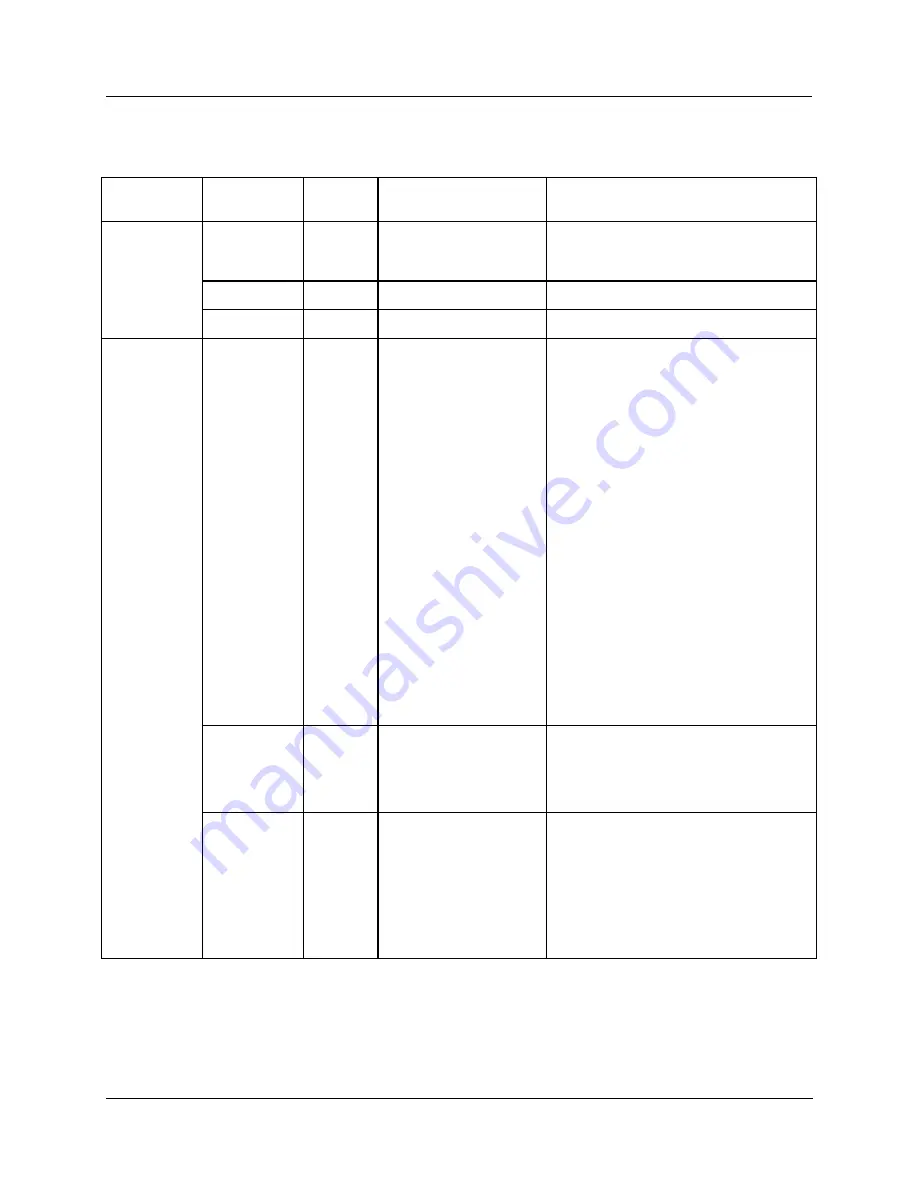
Function Blocks
PID Function Block
Revision 11
HC900 Hybrid Control Designer Function Block Reference Guide
273
2/07
Table 79 PID General tab configuration parameters
Properties
Group
Parameter
Index #
Parameter Description
Value or Selection
Block Order
N/A Execution
Order
Read Only. To change block order, right-
click on a Function Block and select
Execution Order.
Tag
Name
N/A
16 character tag name
Descriptor
N/A Block
descriptor
Control Algorithm
N/A Control
Algorithm
Note: In PID B, step
changes in setpoint
will not bump the
output; the output will
slew smoothly to the
new value.
In PID A, a step
change in setpoint will
result in a step change
in output
.
PID A
- is normally used for 3 mode
control. The output can be adjusted
somewhere between 100 % and 0 %. It
applies all three control actions -
Proportional (P), Integral (I), and
Derivative (D) - to the error signal.
PID B
- Unlike the PID-A equation, the
controller gives only an integral response
to a setpoint change, with no effect on
the output due to the Gain or Rate action,
and gives full response to PV changes.
DUPA -
like PID A but provides an
automatic method to switch tuning
constant sets for Heat/Cool applications.
DUPB -
like PID B but provides an
automatic method to switch tuning
constant sets for Heat/Cool applications.
NOTE: With PID B or DUPB selection,
you
will not
be allowed to set RESET or
RPM to 0.00 (OFF). Reset must be
enabled.
Direction
N/A Control
Action
DIRECT
- PID action causes output to
increase
as process variable increases.
REVERSE
- PID action causes output to
decrease
as process variable increases.
SP
Tracking
N/A Setpoint
Tracking
None
Track PV
- When control mode is
“manual”, local setpoint tracks process
variable.
Track RSP
- When setpoint is “remote
setpoint”, local setpoint tracks remote
setpoint.