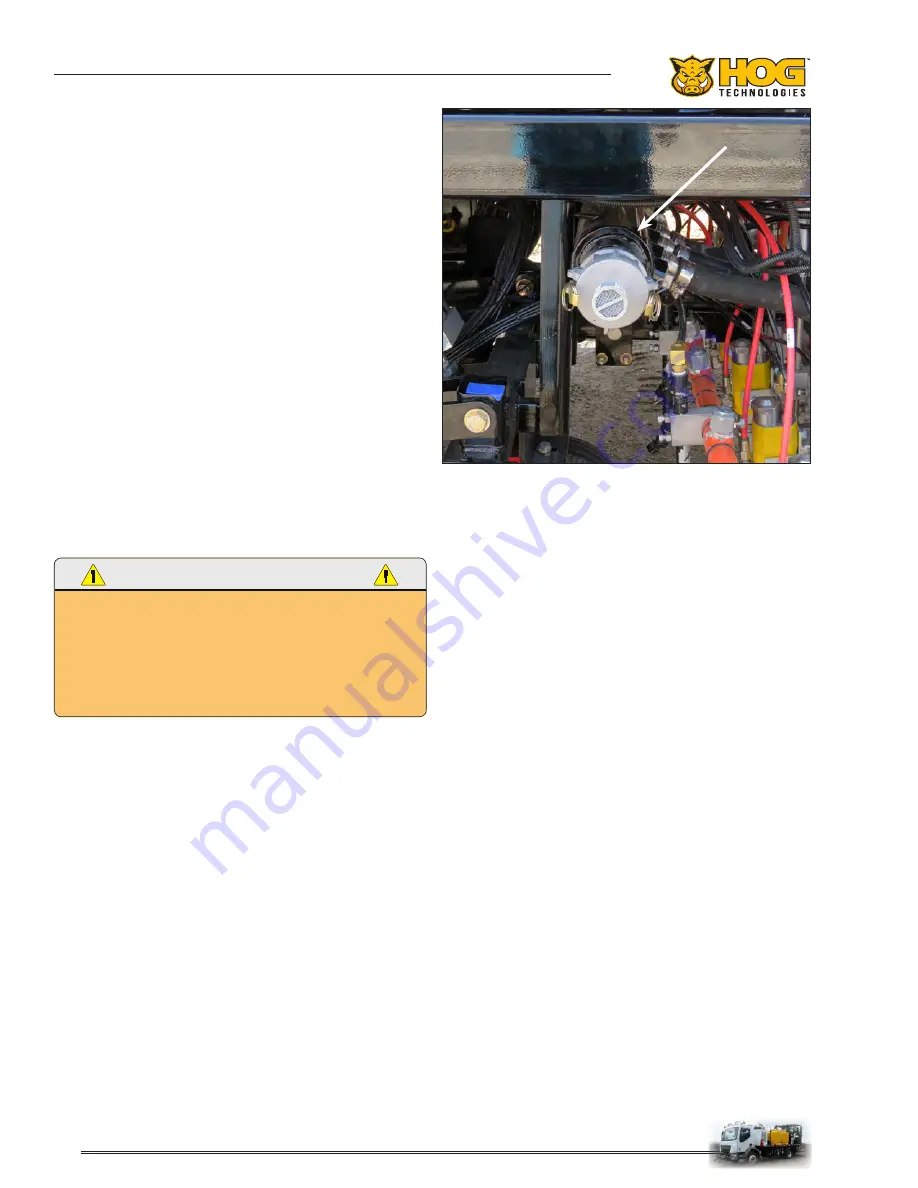
32
32
Section 2 - Paint Hog Systems
Bead Delivery System
The bead delivery system includes tubing, hoses,
manifolds and valves that channel the beads
from the tank to the bead guns. When the tank
is pressurized and the supply valve is turned on,
the beads will flow through the tubing and hoses
to the manifolds.
Beads accumulate and remain in the manifolds
until the valves at the guns are turned on by
switches in the gun control panel. The beads then
flow from the manifolds, through individual hoses
to the gun nozzles.
Special valves on the side of the manifolds purge
air locks from the bead hoses. Filters at the purge
valves prevent the beads from flowing out the
valves. These filters need to be removed and
cleaned periodically to provide proper purging.
Each manifold has a clean out cap secured to the
manifold with cam locks. The cap can be opened
to remove clogs in the manifolds or hoses con-
nected to the manifolds.
WARNING
NEVER ATTEMPT TO REMOVE THE CLEAN OUT CAP WHILE
THE BEAD TANK IS PRESSURIZED. PRESSURE IN THE TANK
WILL MAKE THE CAP DIFFICULT TO REMOVE AND WILL
BLOW THE CAP FROM THE MANIFOLD UNEXPECTEDLY
DURING REMOVAL. THIS COULD RESULT IN SERIOUS
INJURY OR EVEN DEATH TO PERSONNEL AND DAMAGE
COMPONENTS.
Bead Manifold, Cap & Filter
Summary of Contents for PAINT HOG
Page 2: ......
Page 10: ...10 NOTES...
Page 50: ...50 NOTES...
Page 80: ...80 NOTES...
Page 82: ...82 NOTES...
Page 85: ......
Page 86: ......