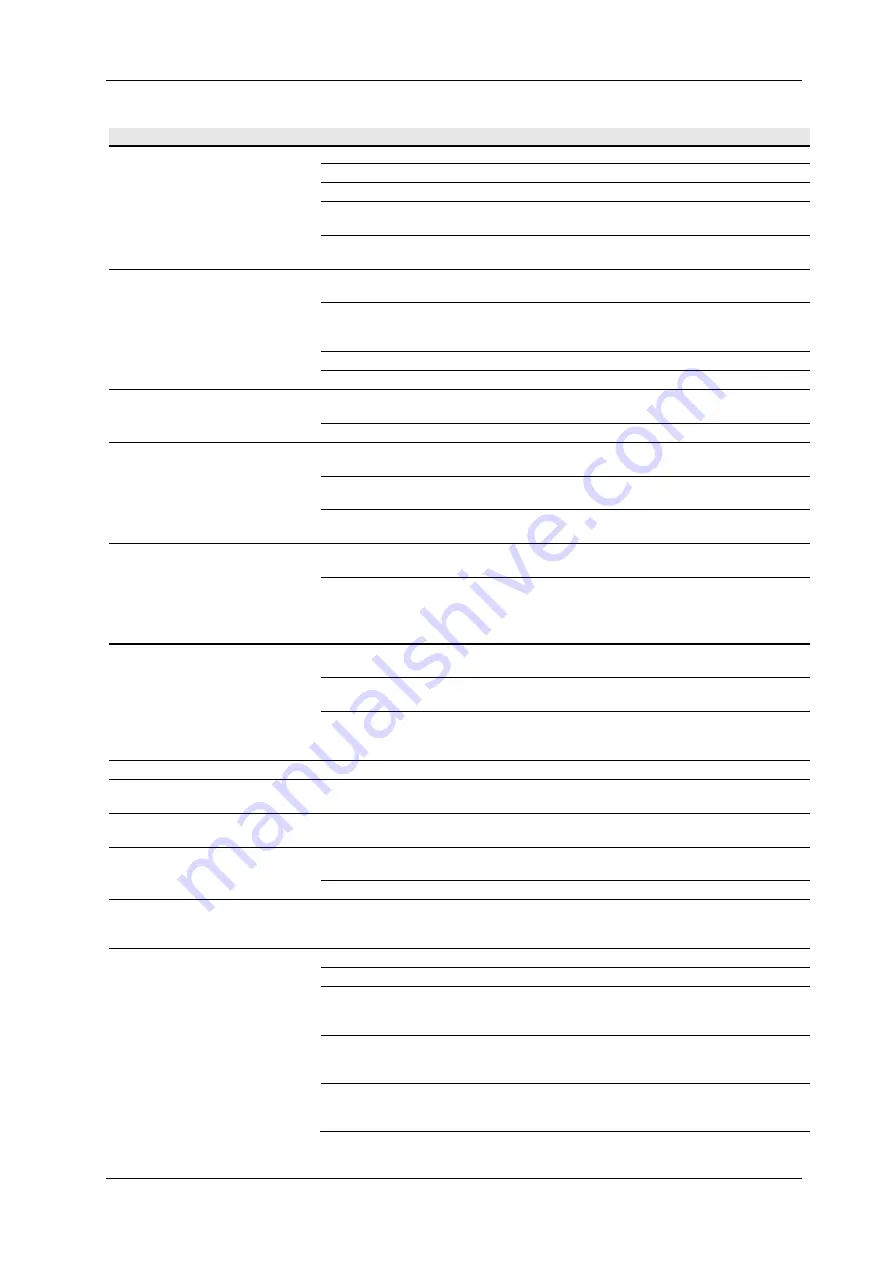
15 Problems and their removal
Operating manual for micro annular gear pumps mzr-7240
68
Technical data subject to change without prior notice!
Last update: March 2019
Disturbance
Cause
Solution
system.
Flush the pump with a syringe.
The non-return valve does not open.
Rinse the non-return valve.
Blockage of the delivery tubing or the
needle.
Cleanse, flush or exchange the delivery tubing
or the needle.
Air bubbles in the liquid delivery system,
(tubing, valves)
Fill in the pump and the delivery system with
liquid.
6 Dosage volume does not
correspond to the set values.
Air bubbles in the liquid delivery system,
(tubing, valves ,...) and the pump
Vent the liquid delivery system and check for
untight fluid connections.
Pump shows cavitation.
Too long or too narrow intake tubing. Shorten
the intake tubing or change the position of the
pump.
Polluted or too small filter
Change the filter to a new or bigger one.
The non-return valve does not open.
Rinse the non-return valve.
7 Speed of the pump cannot be
adjusted.
Defective electric installation
Check the electric installation for correct cable
configuration and loose contacts.
Defective drive control
Return the drive control to the manufacturer.
8 Liquid drops from the dosing
needle.
The non-return valve does not close.
Rinse the non-return valve.
Too high pressure on the primary liquid
tank
Stop the delivery of compressed air on the
primary liquid tank.
The liquid tank is placed at a higher level
than the dosing needle.
Place the liquid tank at the same or slightly
lower level than the pump.
9 Liquid leaks from the fluidic seal.
The connection kit of the fluidic seal
module is untight.
Check the assembly, tighten the threaded
connections.
Pressure on the induction tank of the
fluidic seal liquid
Stop the delivery of compressed air on the
sealing liquid tank
Defective sealing - if necessary return the pump
to the manufacturer.
10 The dosage volume decreases with
time.
Polluted filter.
Exchange the filter.
Deposits in the pump.
Flush the pump or return it to the
manufacturer for dismantling and cleaning.
The pump is worn after a long operating
period or after use with abrasive liquids.
New definition of the calibration factor of the
pump, by modifying the pump characteristics
graph necessary.
11 Leakage from the pump
The sealing does not function correctly.
Return the pump to the manufacturer.
12 Leakage from the coupling
assembly
Defective shaft seal
Return the pump to the manufacturer to
change the shaft sealing.
13 Leakage from the fluid connections Untight lock rings
Exchange or tighten the fluid connections,
exchange the fluid connection fittings.
14 Air bubbles on the delivery side
Loose fluid connections (particularly on the
induction side)
Check and tighten the fluid connections.
The shaft seal is untight or worn.
Return the pump to the manufacturer.
15 Minimal leakage during standstill
No error, cause relative to the operating
principle
Employ a non-return valve.
Place the liquid tank at the same or slightly
lower level than the pump
16 Excess temperature
The surface of the pump is hot.
Clean the surface of the pump, rinse the pump
The pump operates with difficulty.
The pump should be flushed.
Particles in the delivered liquid or deposits
in the pump
The operation of the pump should immediately
be stopped! Return the pump to the
manufacturer for cleansing.
Noise of beveling
The operation of the pump should immediately
be stopped! Return the pump to the
manufacturer for cleansing and repair.
The motor surface or the motor interior are
too hot.
High temperature indicator in the drive is on.
The motor has been shut down by the
thermistor. Return the pump to the