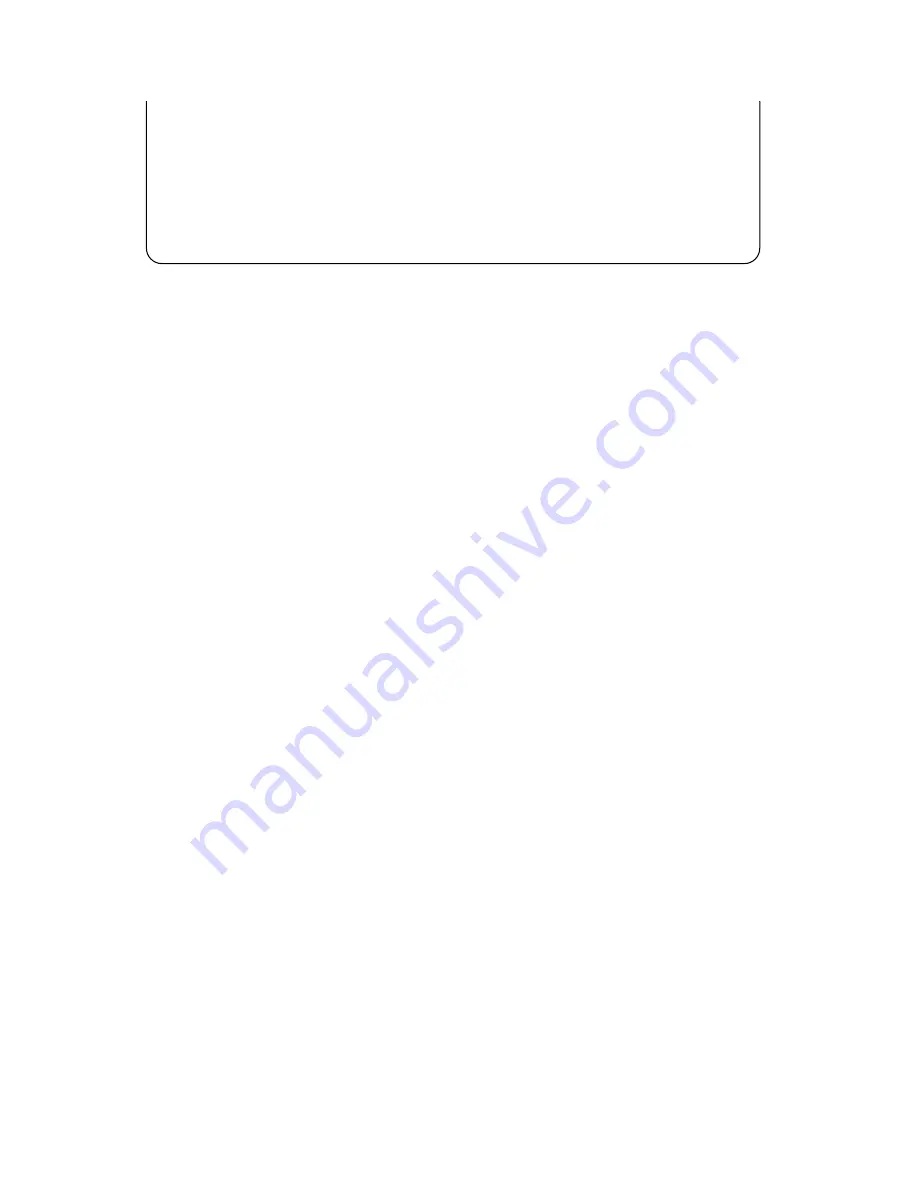
-7-
[For the U.S.A. and Canada]
WARNING
To reduce the risk of injury, user must read and understand instruction manual.
Always use guards and wear eye protection.
Use only accessories rated at least * /min.
AVERTISSEMENT
Afin de reduire le risque de blessures, I'utilisateur doit lire et bien comprendre le mode d'emploi.
Utilisez toujours un outil muni d'un protecteur et portez des lunettes on une visiere.
N'utilisez que des accessoires prevus pour au moins * /min.
* G 12VA
: 13,300
G 13VA, G 13YF
: 12,000
G 15VA, G 15YF
: 10,200
2. Control Circuit Functions and Operation
(1) The control circuit generally consists of four components (see Fig. 1). The following describes the
function and operation of each circuit component:
(a) Rotation speed detector
The rotation speed detector generates a signal whose frequency is in proportion to the motor rotation
speed.
A magnetic sensor within the controller assembly detects flux changes due to the magnet built into
the rotor assembly, and generates the frequency signal.
(b) Variable resistor
The variable resistor applies a reference voltage to the microcomputer in order to determine the no-
load speed (reference rotation speed).
(c) Triac
A trigger signal from the microcomputer determines the conduction angle of the triac, according to
which voltage is applied to the motor.
(d) Microcomputer
Under program control, the microcomputer generates trigger signals to turn the triac on and off
according to frequency signals from the rotation speed detector, the reference rotation speed
specified by the variable resistor, and the on or off state of the main switch.
The microcomputer performs the following controls based on precise trigger signal control:
• Soft-start speed control: The microcomputer generates trigger signals so that the triac's conduction
angle is gradually increased until motor speed reaches the reference rotation speed.
• Constant speed control: The microcomputer generates trigger signals so that motor speed, even if
varied, approximates the reference rotation speed. In other words, the microcomputer enlarges the
triac's conduction angle to increase voltage applied to the motor when motor load increases,
thereby lowering the rotation speed. In this way, motor speed becomes closer to the reference
rotation speed.
• Overload protection control: For overload protection, the microcomputer issues a command to shut
off power to the motor when the motor is placed under a heavier load during operation or the triac's
conduction angle exceeds a preset limit, thereby significantly lowering the rotation speed below a
preset minimum rotation speed.
• Kickback protection control: For kickback protection, the microcomputer computes the drop in
rotation speed per a specified length of time when the tool attached to the grinder receives a load
large enough to immediately stop the tool's rotation during operation, and issues a command to
shut off power to the motor if this computed drop exceeds a preset drop limit.
• 0-voltage restart protection control: For 0-voltage restart protection, the microcomputer issues a
command to shut off power to the motor to disable motor restarting once power is restored after
being cut off, even if the main switch is on (since it detects the on and off states of the main
switch) .