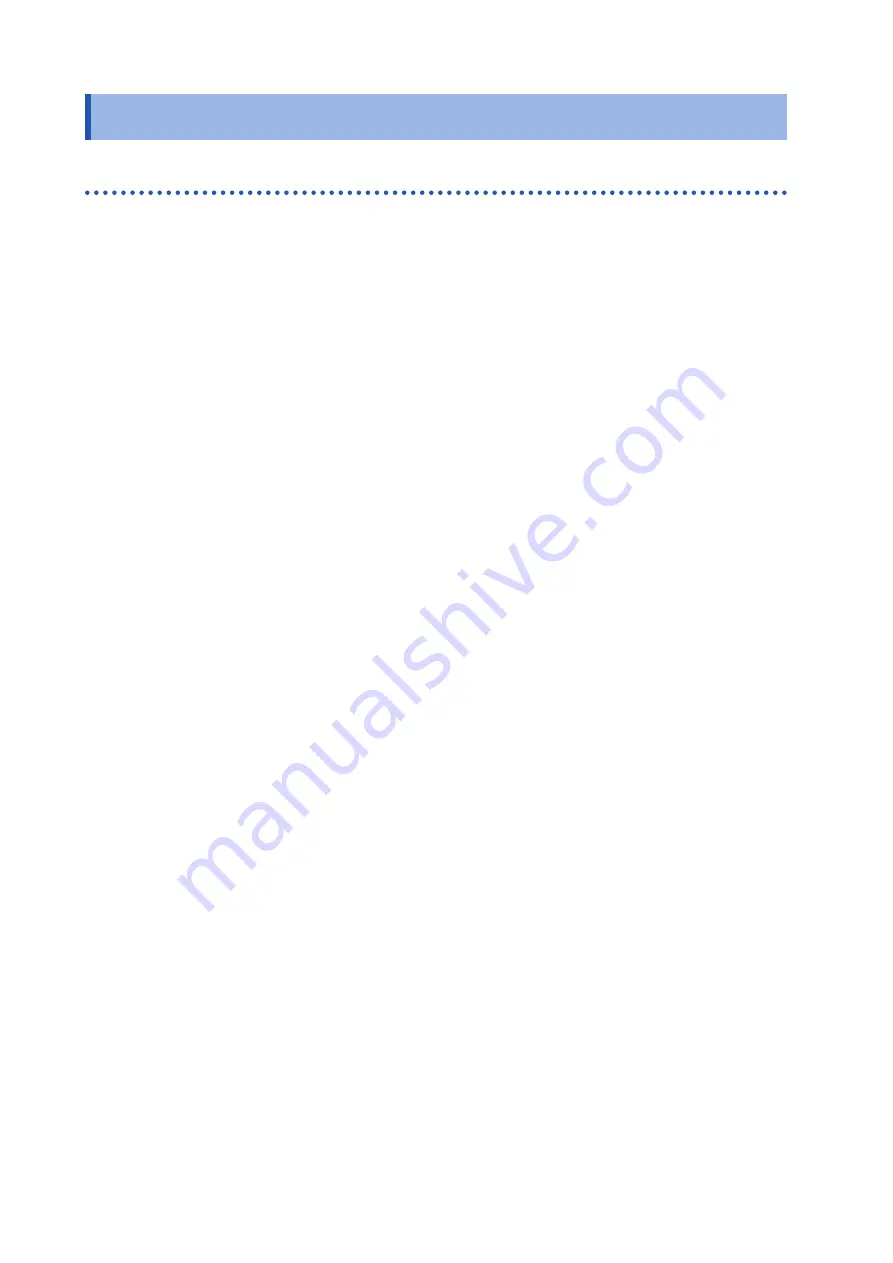
64
USB Interface
8.4 USB Interface
Installing the USB driver
When the device is connected to a PC for the first time, the dedicated USB driver is required. If the
driver is already installed, the following procedure is not required. The USB driver is on the provided
CD. It can also be downloaded from our website.
Installation procedure
Before connecting the device and PC using a USB cable, install the USB driver. If a USB cable is
already connected to the device and PC, remove the USB cable.
1
Log into the PC using an account with administrative privileges such as “administrator”.
2
Exit all applications running on the PC.
3
Open [X:\driver] on the provided CD and execute
[HiokiUsbCdcDriver.msi]
(driver installer) (X:
is a CD-ROM drive).
Follow the instructions that appear on the screen to continue the installation. Wait for a dialog box as it may
take some time depending on the operation environment.
4
Connect the device and PC using the LAN cable after the installation is completed.
The device should now be recognized.
• If the Found New Hardware Wizard screen for new hardware is displayed, select
[No, not this time]
and
then select
[Install the software automatically (Recommended)]
for checking the connection to Windows
Update.
• Even when a device with a different serial No. is connected, you may receive notification of the installation of
a new device. Follow the instructions on the screen and install the USB driver.
• A warning message is displayed since the Windows
®
logo has not been acquired. Ignore the message and
continue the installation procedure.
Uninstallation procedure
Uninstall the USB driver when it is no longer required.
Click
[Control Panel]
-
[Uninstall a program]
, and then delete
[HIOKI USB CDC Driver]
.
Summary of Contents for SW1001
Page 2: ......
Page 42: ...38 Precautions for Measurement...
Page 48: ...44 Resetting Scan Operation...
Page 50: ...46 Checking the Device Status...
Page 52: ...48 Initialization Settings...
Page 118: ...114 Sample Programs 3 Select File Save All 4 Check the save location and click Save as...
Page 156: ...152 Outline Drawings 12 4 Outline Drawings SW1001 Unit mm Tolerance 0 2...
Page 157: ...153 Outline Drawings SW1002 Unit mm Tolerance 0 2 12 Appendix...
Page 158: ...154 Outline Drawings...
Page 161: ...16 01 EN...
Page 162: ......
Page 163: ......
Page 164: ......