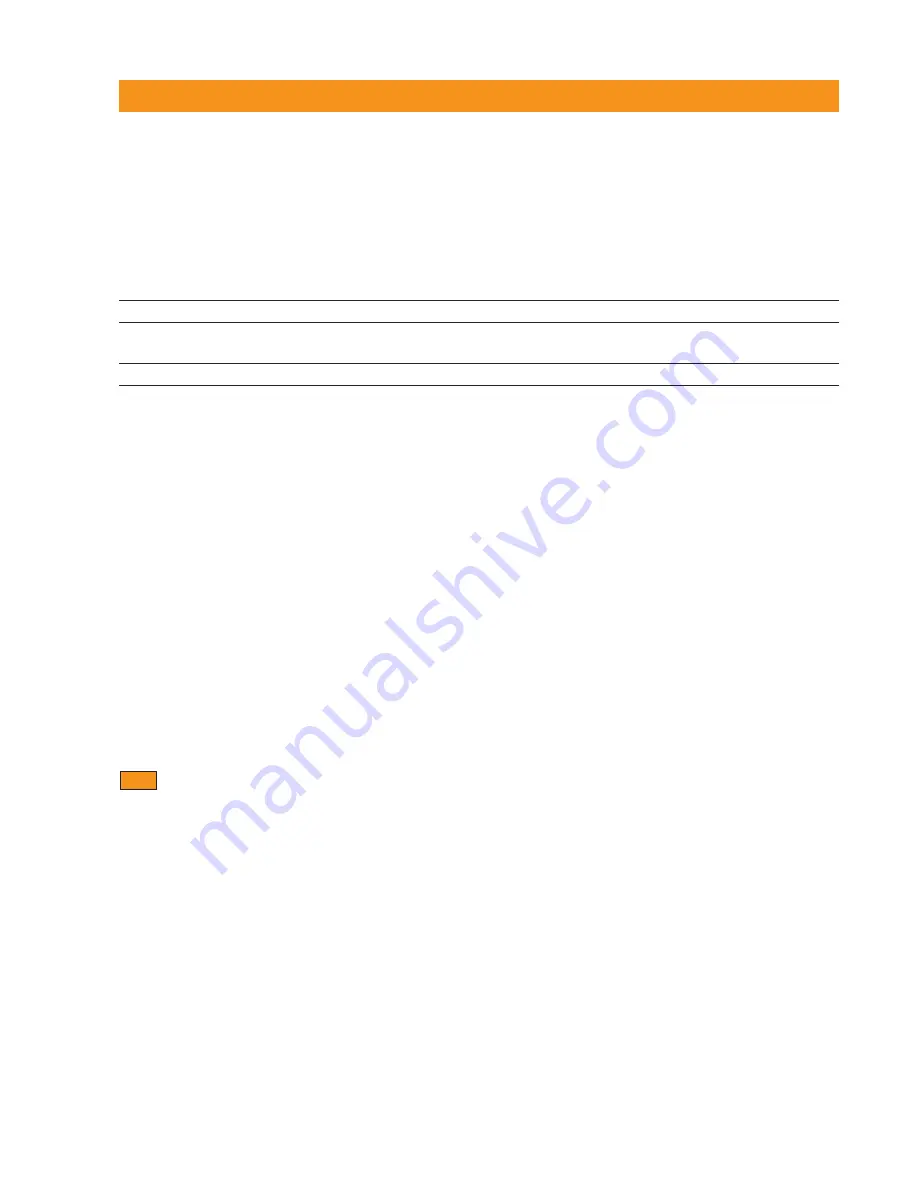
Operation
Operating hours counter
After switching on, the total number of hours that the
saw head has been in operation is displayed.
Power indicator
The actual power input is displayed during operation
of the saw (in %).
Supply voltage
During operation, turn starting switch
to “Start”
(voltage is displayed).
Fault indicator
The code displayed can help to localize a possible
fault (e.g. Er01).
Speed indicator
Can be adjusted by the knob at position
.
21
Warning
Operation of the saw without blade guard and end
stops fitted is not permissible!
22
Recommended speed range
-NOTE-
To read the mains input voltage while the saw is in operation, proceed as follows:
1. Turn the starting switch
to the “Start” position and hold it there.
2. The voltage reading is shown in the display
in volts.
To read the mains input voltage while the saw is stationary, proceed as follows:
1. Turn the starting switch
to the “I” position.
2. Set the saw blade speed control knob
to the maximum speed position.
3. Turn the starting switch
to the “Start” position and hold it there.
4. The voltage reading is shown in the display
in volts.
The procedure described below can be used to reverse the positions of the switch controlling direction of advance:
1. Turn the starting switch
to the “I” position.
2. Set the advance speed control knob
to the zero position.
3. Set the saw blade speed control knob
to the maximum speed position.
4. Operate the direction of movement control switch
or
.
5. Turn the starting switch
to the “Start” position and hold it there.
6. When reversal of control direction has been successful, “L__R” is shown in the display
.
Operating the saw
1. Use the plunge
and advance
controls and the speed regulation knob
to move the saw head along the
rail to where the cut is to be started and then return all switches / knobs to the “Neutral” or “Zero” position. For
rapid movement, turn the speed regulation knob
to the right, beyond the pressure point
, as far as it will go.
2. Switch on the cooling water
.
3. Switch on the saw blade drive
and then use the speed control
to set the desired speed (please observe rec-
ommended speeds). Wait until the blade runs up to speed.
4. Select the direction of plunge movement
and advance speed
and then bring the blade slowly to the desired
cutting depth (cut into the concrete). Set the plunge movement
and speed regulator
back to the “Neutral”
or “Zero” position when the desired depth has been reached.
5. Select the direction of longitudinal advance
and the desired speed
, e.g. 100%. Make the initial cut at reduced
power (60%).
6. At the end of the cut, turn the speed control
to the “Zero” position and switch off the longitudinal advance
.
7. Repeat steps 4 to 6 until the desired depth is reached.
8. Once the cut has been completed or the maximum depth reached, use the plunge movement direction control
to lift the saw blade out of the kerf while the blade is still rotating, bringing the saw and saw arm to the 90°
position.
5.3
25
Printed: 08.07.2013 | Doc-Nr: PUB / 5069686 / 000 / 01