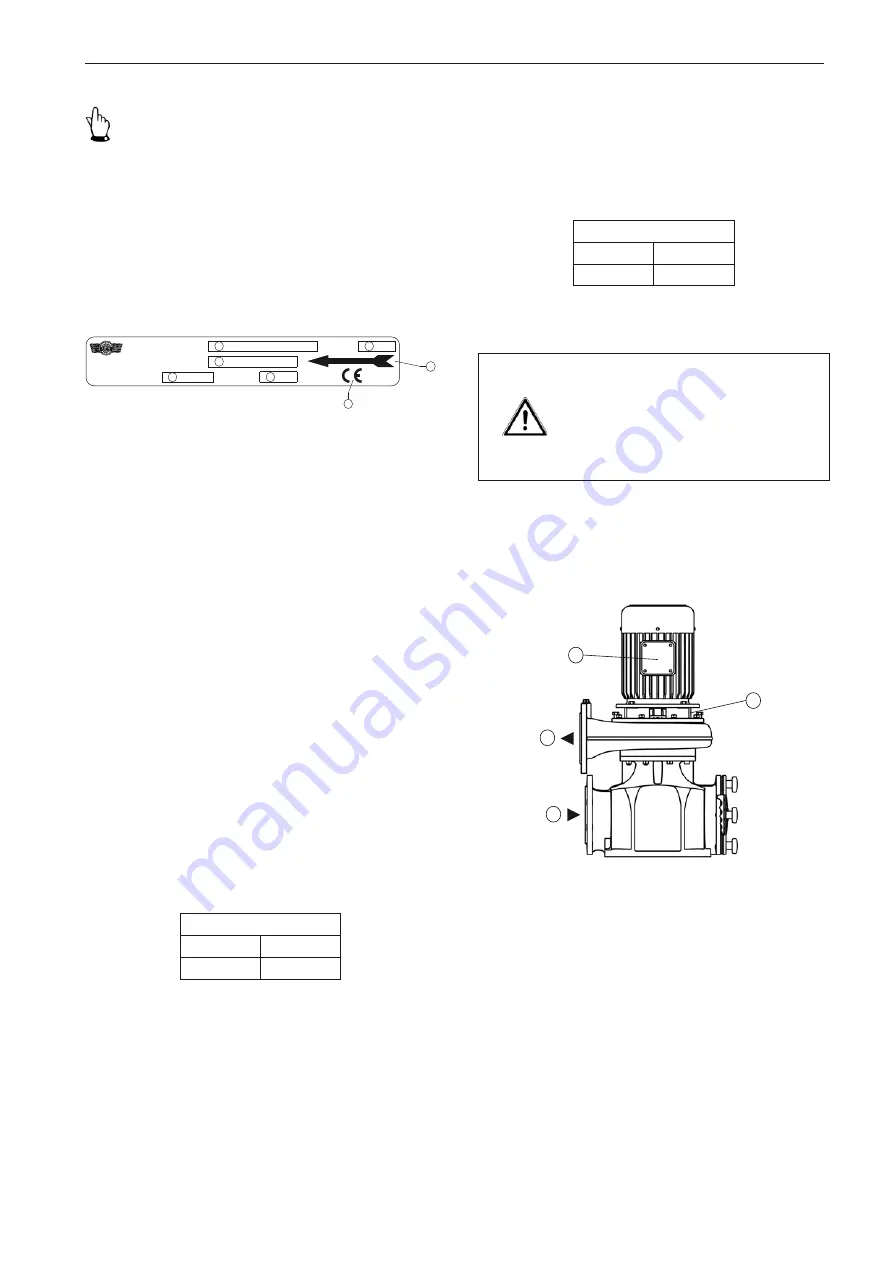
Safety
13
Figure 2 Name plate
Key to figure 2
1. Model designation
2. Year of manufacture/ month
3. Order No.
4. Nominal flow rate
[m
3
/h]
5. Nominal head
[m]
6. CE symbol
7. Observe the direction of rotation!
2.2
Integrated safety systems (optional)
Check the integrated safety devices in regular inspection
intervals
j
= annually.
The inspection methods applied here are:
S
= Visual inspection,
F
= Functional check.
Winding protection
If the pump is also equipped with thermal winding protec-
tion with direct temperature monitoring, this switches off the
pump's motor if it starts to get too hot.
Inspection
Interval
Method
j
S, F
Important!
When making any inquiries and ordering spare parts
please make sure you specify the pump type and the order
number.
Also observe the name plate on the motor.
The name plate is attached to the fan hood or the motor
housing (UNIBAD-XC).
ETS X4
An existing ETS X4 (electronic dry running protection system)
that uses a vibrating fork sensor prevents the dry running
of the slide ring seal. This protects the functionability of the
pump.
Inspection
Interval
Method
j
S, F
Caution!
Incorrect warming will damage the
three-phase motor.
Do not decommission safety equipment
or change its mode of operation.
2.3
Connections on the pump
Figure 3 Connections on the pump
The following connections are available on the pump:
1. Inlet connecting flange
2. Outlet connecting flange
3. Electric connection (terminal box)
4. Venting
1.
2.
3.
4.
Auftrag-Nr.
Q
Bj./ Mon.
m
m /h
3
1
3
4
5
2
6
UNIBAD
Pumpe
Herborner Pumpenfabrik
J.H. Hoffmann GmbH & Co. KG
Littau 3-5, DE-35745 Herborn
7
Summary of Contents for UNIBAD-X
Page 4: ......