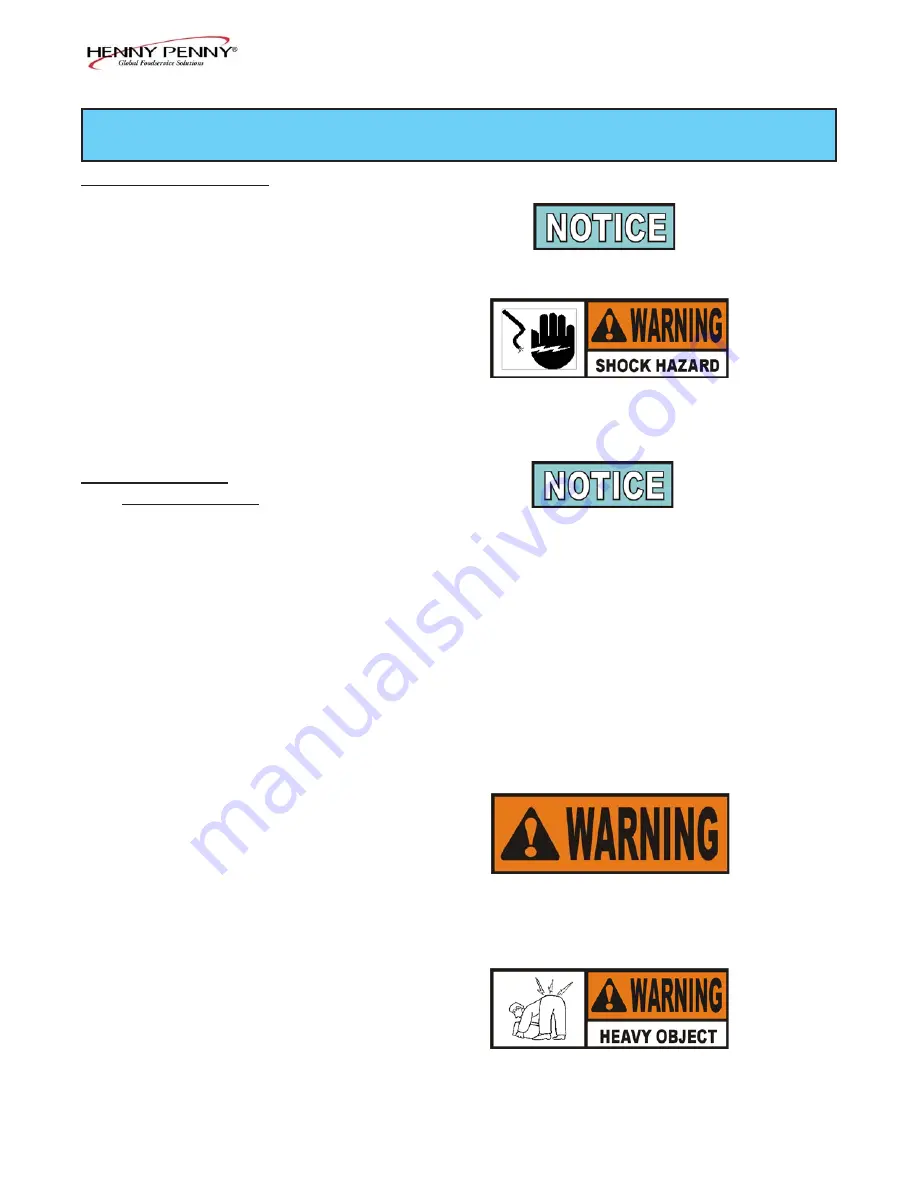
Model OFG- 390
SECTION 2. INSTALLATION
This section provides the installation and unpacking instructions for
the Henny Penny OFG-390, open fryer.
Installation of this unit should be performed only by a qualified
service technician.
Do not puncture the unit with any objects such as drills
or screws as component damage or electrical shock
could result.
Any shipping damage should be noted in the presence of the
delivery agent and signed prior to his or her departure.
1.
Cut and remove the metal bands from the carton.
2.
Remove the carton lid and lift the main carton off the fryer.
3.
Remove corner packing supports (4).
4.
Cut the stretch film from around the carrier/rack box and
remove it from the top of the fryer lid.
4.
Cut and remove the metal bands holding the fryer to the
pallet.
All counterweights must be loaded before unlatching the
lid, or personal injury could result.
5.
Remove the fryer from the pallet.
Take care when moving the fryer to prevent personal
injury. The fryer weighs approximately 670 lbs.
(304 kg).
2-1. INTRODUCTION
2-2. UNPACKING
INSTRUCTIONS
803
2-1
Summary of Contents for OFG-390
Page 1: ...OPERATOR S MANUAL Henny Penny Open Fryer Model OFG 390 ...
Page 2: ......
Page 10: ......
Page 13: ...Model OFG 390 OptionalRampUnloading 703 2 3 ...
Page 14: ...Model OFG 390 2 4 908 ...
Page 18: ...Model OFG 390 2 8 303 ...
Page 22: ......