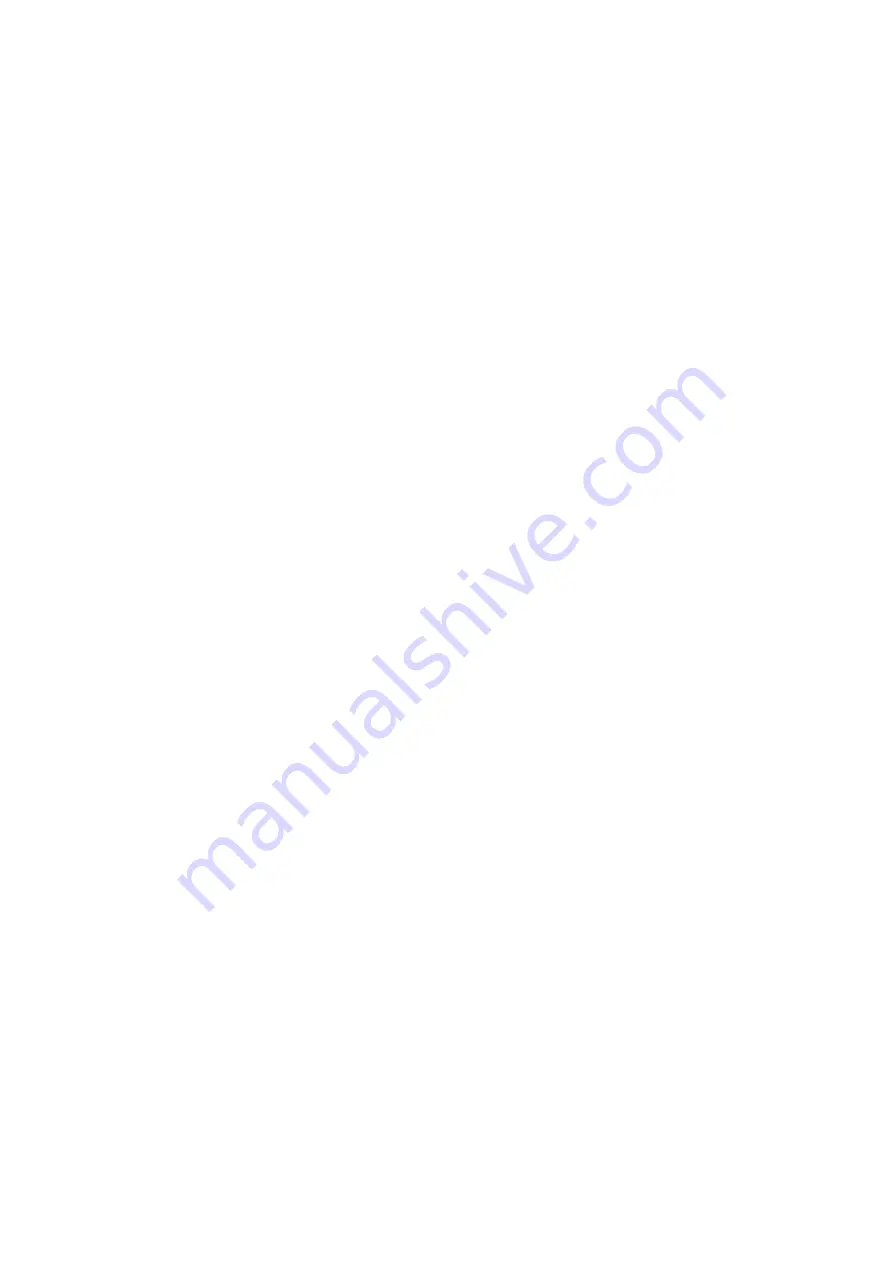
38
important. Improper maintenance has a bad effect on truck.
1) check the lubrication condition of pin axle, bearing and side shifter moving
surface of each hinged points regularly. Add lubrication grease if necessary.
2) check the clearance of side roller on inner and outer fork plate. Adjust
according to wear condition. Refer to the “adjusting of combined roller” for its
adjusting method and requirement.
3) Check the bearings at each hinged points and two sides of telescopic cylinder
regularly. When the bearing is worn out and the oil storage tank is worn flat, change
it.
4) Check the hydraulic pipelines of telescopic fork regularly to prevent pipeline
from aging.
4.8.11 Lifting chain maintenance
The lifting chain is very important part of truck. it is necessary to maintain the
lifting chain in order to truck safety working. Improper maintenance period will result
poor performance of chain.
4.8.12 Cleaning of lifting chain
Note: when delivery, the lubrication grease on the lifting chain is used to protect
it from corrosion. Please do not remove the lubrication grease on the lifting chain.
Note: lubrication frequency is different with working condition and ambient
condition.
4.8.13 Lifting chain lubrication
Please lubricate the lifting chain according to maintenance table to prolong chain
service life as far as possible. Apply lubrication grease between chain parts and on the
surface of chain so as to:
1) reduce the wear at contacting points;
2) prevent it from corrosion;
3) reduce the frequency of rotating pin;
Summary of Contents for CQD16X1
Page 1: ......
Page 9: ...5 II External View of Reach Truck Figure 2 1 External view of reach truck ...
Page 102: ...98 6 3 Lubricating chart ...
Page 105: ......