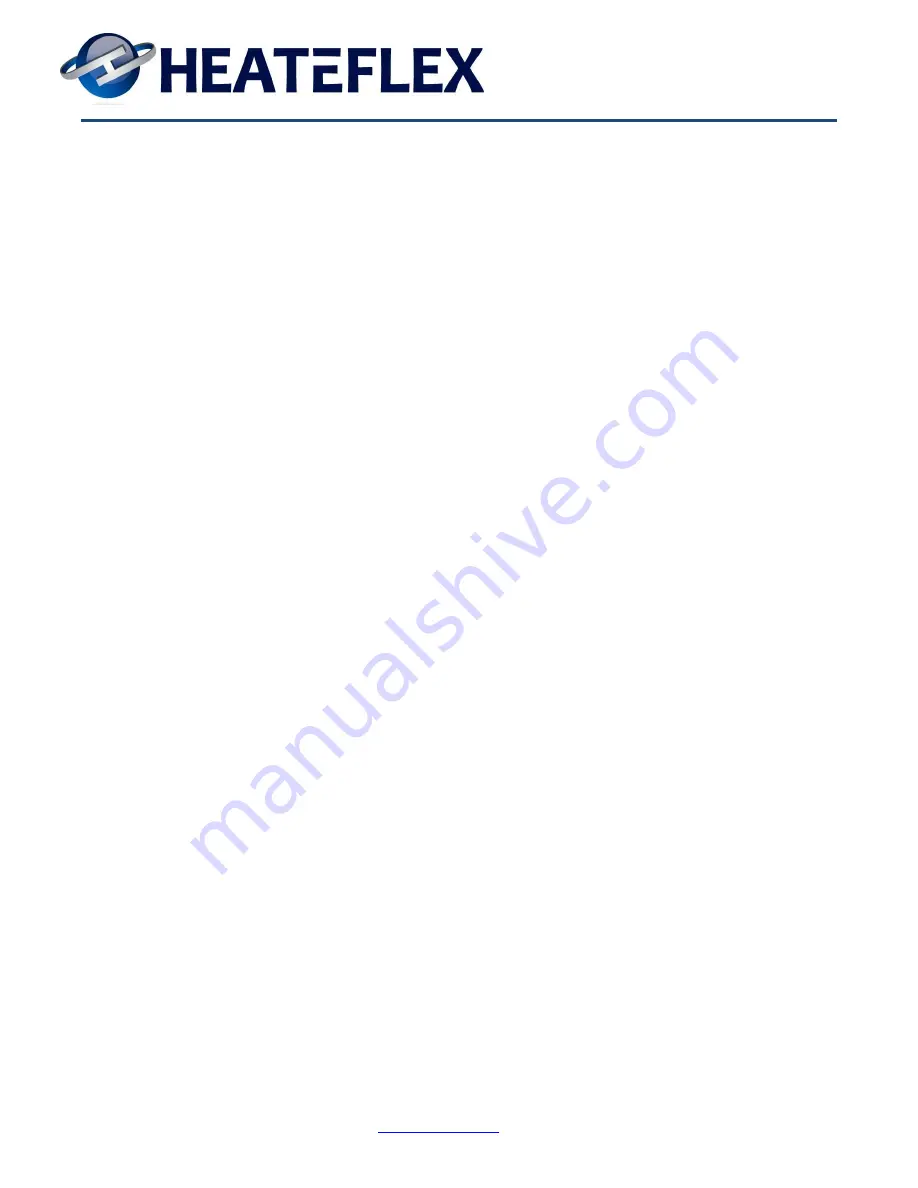
World Leaders in Ultra-Pure Heating
Revision 10
www.heateflex.com
01/17/13
405 E. Santa Clara St.
Arcadia, CA 91006-7218
Tel: (626) 599-8566 Fax: (626) 599-9567
2.0 Theory of Operation
__________________________________________________________
2.1 System Overview
The Fluidix PC Series D.I. Water Heating System combines a steam-powered PFA heat
exchanger with a process temperature-control system to provide a "turn-key" D.I. water-
heating system.
All wetted surfaces are virgin PVDF, PFA and PTFE with elastomeric PTFE for piping seals
for no measurable change in TOC, particles ≥0.06µ or bacteria, and less than 0.1 ppb ionic
contamination from the process inlet to the process outlet. Each system is computer designed
to ensure sufficiently high water velocity to prevent bacteria growth, particularly in the inlet
region of exchanger tubing where the water is warm but not yet sufficiently hot to kill the
bacteria. During a period of low or no flow, the D.I. water in the tubing quickly rises to
sterilization temperatures.
The exchanger is a kettle-type configuration with a PFA tube bundle wound helically around a
central support, which is mounted to the exchanger cover. Removal of this exchanger cover
gives complete access to the Fluidix tube bundle for inspection of all its components. The
vessel and its cover comprise a pressurized system where steam is introduced through a
flanged inlet mounted at the side of the exchanger vessel, and where steam condensate is
drained at the bottom.
The exchanger bundle utilizes a sanitary head design such that continuous lengths of tubing
pass through the vessel cover and connect to pipe headers above the exchanger cover (See
Appendix). This configuration provides that there are no welds or connections in the tubing
within the exchanger vessel, which could potentially leak. If a tube fitting on a pipe header
develops a leak, it can be easily accessed and tightened after the unit is cooled down.
Temperature control, independent of flow rate, is accomplished by means of two mixing
valves, which blend ambient-temperature water with the hot exchanger effluent water to yield
the desired output temperature. A thermocouple temperature sensor monitors the outlet
temperature whose signal along with that of a shedding-vortex flow meter is then used by the
PLC controller to position the mixing valves as needed.