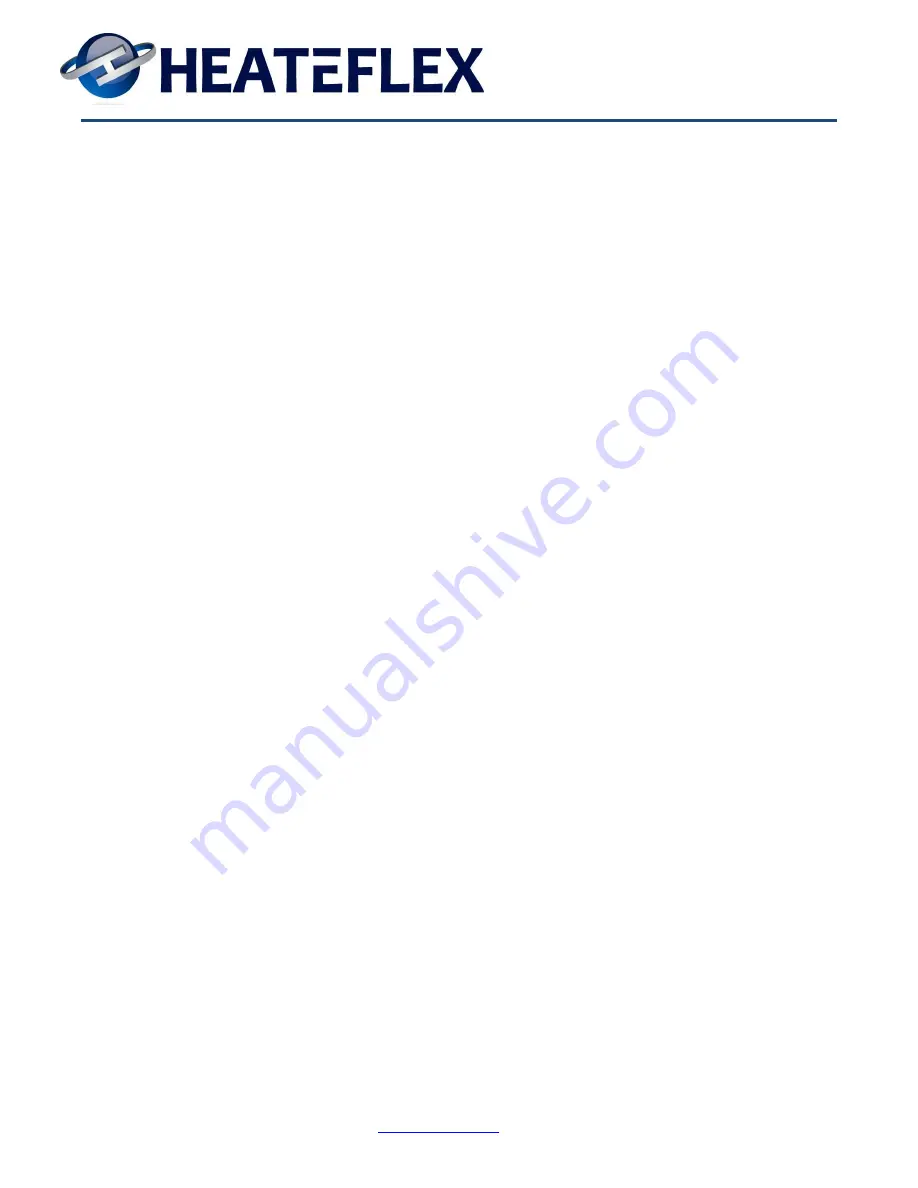
World Leaders in Ultra-Pure Heating
Revision 10
www.heateflex.com
01/17/13
405 E. Santa Clara St.
Arcadia, CA 91006-7218
Tel: (626) 599-8566 Fax: (626) 599-9567
Close the customer‟s steam supply valve if it is open at this time, and then press the Auto
switch under “Steam Valve” and observe that the position indicator on the steam-valve actuator
rotates to an open position.
At this point, check that the customer‟s steam trap and condensate return system is activated
and that the vessel drain valve is closed. If there is a bypass valve around the steam trap it can
be opened at this point so that air trapped in the exchanger vessel will be expelled quickly
when the steam enters the exchanger vessel. Begin introducing steam into the unit by slowly
opening the customer‟s steam supply valve a small amount, monitoring the pressure gauge on
the exchanger vessel until it stabilizes, and watching for any steam leaks. Repeat this process
by opening it a little more each time and again waiting until the pressure again stabilizes. If
the steam pressure ever rises above 15 psig be ready to close the unit‟s steam supply valve by
pressing the Close switch under Steam Valve on the System Status screen or by pressing the
EMO switch on the front of the electrical enclosure. This should be done before the pressure
reaches 15 psig or the steam pressure-relief valve will vent, unless it is desired to test the steam
pressure-relief valve itself. Note that the steam supply valve should automatically shut down if
there is a pressure relief venting.
The facility steam regulator (if steam is being throttled down from a higher-pressure steam
system) should be adjusted at this point to read right at 15 psig on the pressure gauge on the
exchanger vessel. If steam is being supplied from a low pressure boiler then a minimum of 12
psig will be necessary to obtain the full output rating of the unit.
__________________________________________________________
6.3 Adjusting Temperature Control Parameters
Referring to sections 3.2.3, 3.2.4, and 3.2.5 of the manual, make the following adjustments as
needed. Adjust the D.I. Process Temperature Set Point and the look-up table values for the
Look-Up Table located in the Recalibration screen. Set the desired alarm set points and alarm
delays in the Diagnostic Information screens of the Low Process Temperature, Process Over
Temperature, Low Process Pressure alarm screens. Adjust the trimmer-function parameters.
The “Time Interval” and “Actuator Increment” can be found in the Recalibration screen. In
most cases the unit has been run at the factory using customer provided data on the flow
regimen and temperatures that the unit is intended for and the program parameters are already
resident in the controller memory. Contact the factory if there is any question and a technician
can assist on a step-by-step basis.
At this point run the process flow regimen (flows and durations) as close to that expected to be
used by the host process tools and use the Temperature Trending screen to access the
temperature control variation over that flow regimen. A ±2°C maximum variation from set
point should be achievable if everything is adjusted to an optimal setting. If there is more
deviation, contact the factory for assistance on further adjustments.