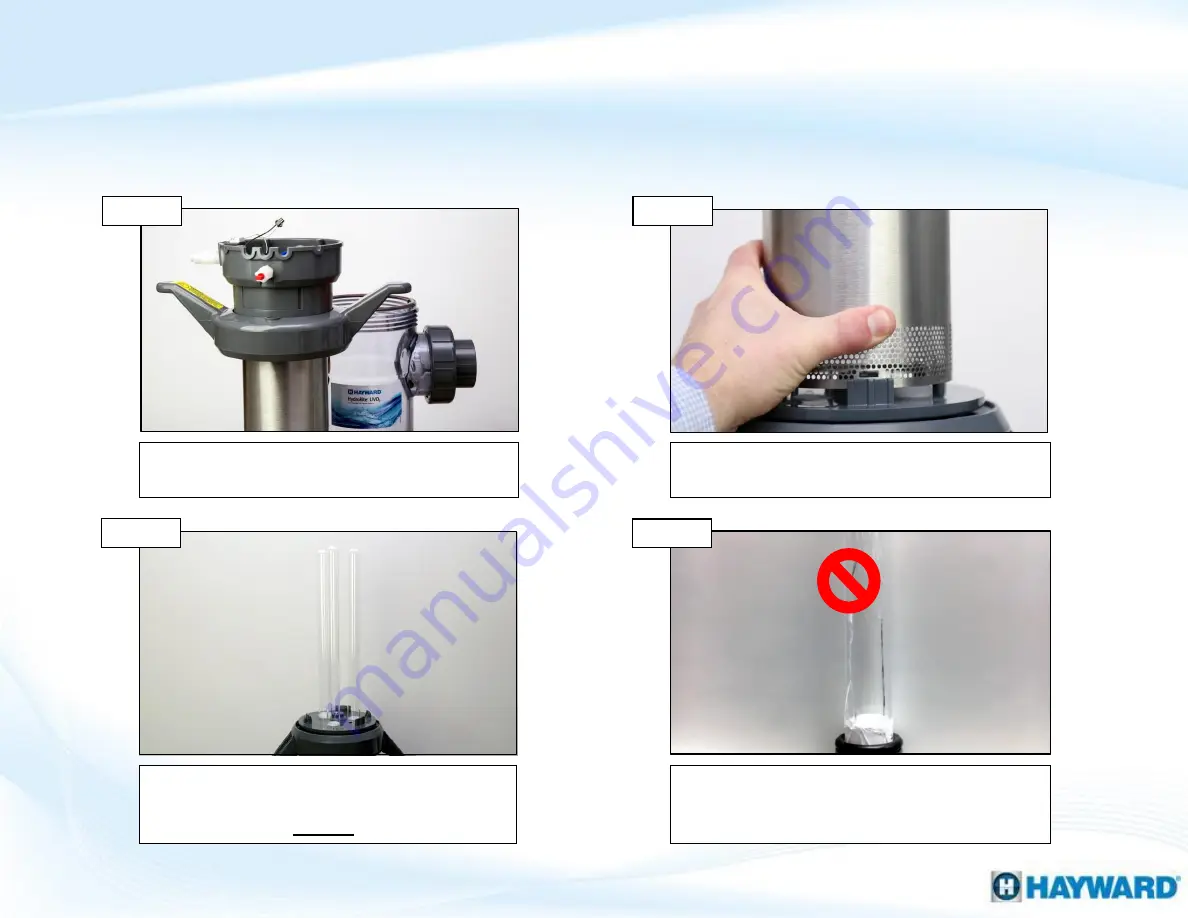
24
IF calcium deposits are encountered, rinse quartz sleeves with tap water, then clean
with Lime-A-Way®, Muriatic Acid (4 parts water – 1 part acid), or isopropyl alcohol.
Loosen the vessel lock nut, rotating counter
clockwise & pull the sleeve straight out.
Pinch the sleeve near the clips to spring it loose
& carefully slide it straight off.
Rinse/clean the outside of the quartz sleeve
ONLY
*
, then clean with rubbing alcohol or
muriatic acid DO NOT use abrasives.
Once dry, inspect the quartz sleeves for cracks,
IF any cracks exist immediately replace (DO
NOT install cracked quartz sleeves).
Step 9
Step 10
Step 12
Step 11
*IMPORTANT: DO NOT clean or get the inside of the quartz sleeves wet or dirty, inside the
sleeve is normally sealed and does not require cleaning.
Cleaning Quartz Sleeve & Lamp Sensor (cont.)
Summary of Contents for hydrorite uvo3
Page 7: ...HydroRite UVO3 Overview ...
Page 10: ...10 HydroRite Vessel Top ...
Page 17: ...HydroRite UVO3 How To ...
Page 26: ...HydroRite UVO3 Troubleshooting ...