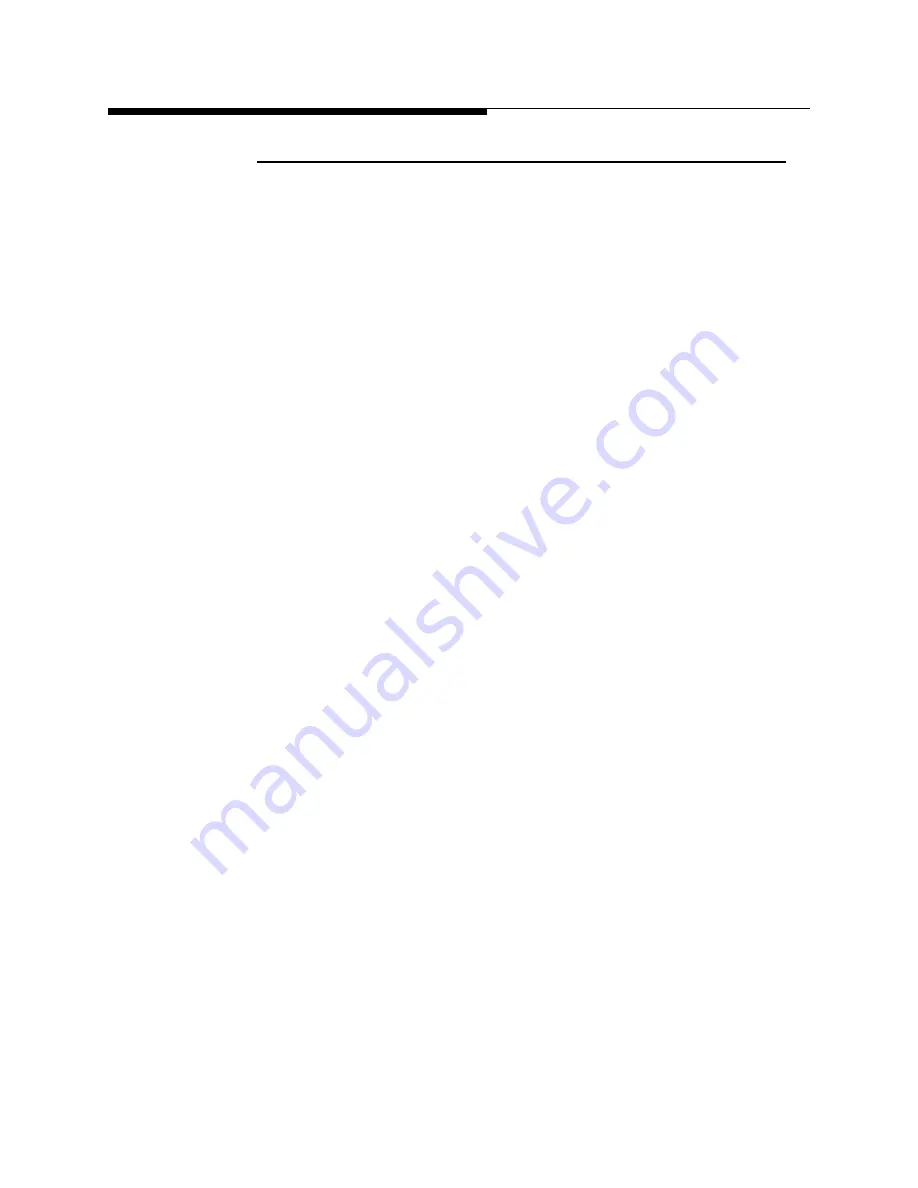
2-14
888-2629-200
10/6/10
WARNING: Disconnect primary power prior to servicing.
Section 2 Installation
Maxiva ULX COFDM Series
2.5.6
Liquid Cooling System Plumbing Installation
Install components as described in the Liquid Cooling System Diagram. Globe or ball
valves should be used in the supply side of each cabinet. Globe valves allow for fine
adjustment of coolant flow through components. Gate or ball valves should be used on
the return line side of cabinets and component.
The pump module has a 1/2” NPT fill and drain valves (3/4" female garden hose
connections). The heat exchanger is fitted with 1/2" bleed and drain valves. An air
purger and automatic air vent (return side) are incorporated into the unit for removal of
air bubbles, which are induced in the system during filling. Additional air bubbles will
continue to be purged and vented as the system operates at higher temperatures.
The main system air purger must be located inside the building, preferably within view
of the transmitter, at the highest point of the plumbing installation. The system air
purger will be equipped with a sight tube to allow the operator to monitor coolant level
and formation of air bubbles that may indicate that the system needs to be charged with
additional coolant. Drain valves should be located at all low points in the system to
allow the system to be fully drained.
A closed expansion tank is provided in the pump module unit utilizing a rubber
diaphragm to compensate for surges in the system. The diaphragm is actuated by air
pressure (approximately 12 PSI charged); a valve is located on the top of the tank for
changing the air charge. Charging the expansion tank is not normally required in the
field. The tank is pressurized at the factory prior to shipment. Contact Harris Field
Service if you feel there is a need to change the air pressure in the expansion tank.
STEP 1
Install supply and return plumbing
. Carefully locate and solder
(copper fittings) or clamp (hoses) to all pipe, valves, plugs, meters,
elbows, adapters, and hose, to the transmitter, pump module, heat
exchanger, reject and test loads according to the drawings (see
"Appendix B" section for this step). Supply and return hose should be
installed without sharp bends. Hose should be supported frequently to
avoid excessive movement as pumps turn on and off. Hose should be
supported using padded clamps.
STEP 2
On long runs of pipe or hose, slope the run (toward a drain point) at
a rate of 1 to 2 inches per 100 feet to facilitate draining the system or
bleeding air from it when filling it.
STEP 3
Install the system (automatic) air purger, shown in Figure 5-23 on
page 5-36, it should be installed at the highest point in supply line.
The system air purger should be visible from the transmitter area since
it will need to be monitored frequently for cooling fluid level and air
bubbles.
Summary of Contents for Maxiva ULX COFDM Series
Page 2: ...ii 888 2629 200 10 6 10 WARNING Disconnect primary power prior to servicing ...
Page 4: ...iv 888 2629 200 10 6 10 WARNING Disconnect primary power prior to servicing ...
Page 6: ...MRH 2 888 2629 200 10 6 10 WARNING Disconnect primary power prior to servicing ...
Page 8: ...viii 888 2629 200 10 6 10 WARNING Disconnect primary power prior to servicing ...
Page 9: ...10 6 10 888 2629 200 ix WARNING Disconnect primary power prior to servicing ...
Page 10: ...x 888 2629 200 10 6 10 WARNING Disconnect primary power prior to servicing ...
Page 12: ...xii 888 2629 200 10 6 10 WARNING Disconnect primary power prior to servicing ...
Page 14: ...xiv 888 2629 200 10 6 10 WARNING Disconnect primary power prior to servicing ...
Page 18: ...Table of Contents Continued 4 ...