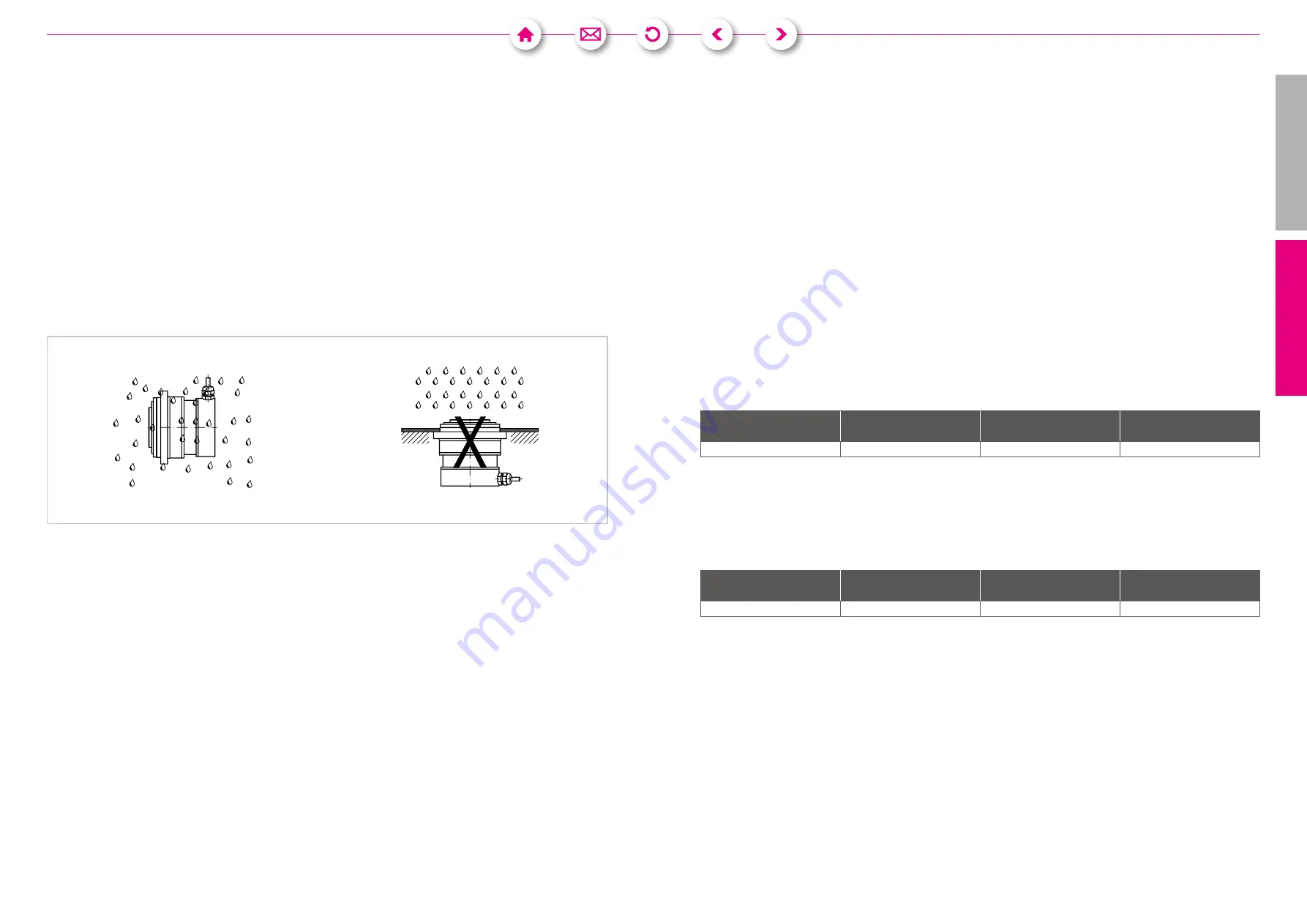
1056748 03/2023
1056748 03/2023
73
72
Protection from overheating
9. Protection from overheating
9.1 General
Ideally, motors and gears are protected against overheating by 3 measures:
•
Good thermal connection of the actuator to the machine frame or a cooling surface
•
Protection by monitoring the temperature with sensors
•
Protection through monitoring of overload currents and overload times
9.2 Specification temperature sensors
Temperature sensors are integrated into the stator windings to protect the servo actuators and motors from temperature
overload. The temperature sensors installed in the drive system vary depending on the servo actuator.
9.2.1 Integrated system IHD and servo actuators BHA
The motor windings of the integrated system IHD and the servo actuators BHA are equipped with a linear temperature
sensor of the type PT1000. The temperature sensor is double base insulated and complies with EN-61800-5-1.
In the integrated system IHD, the temperature sensor is evaluated directly in the integrated servocontroller.
Integrated switching thresholds IHD
Table 20
Sensor type
Unit
Warning
Switch off
PT1000
[C°]
105
115
In the BHA Servo Actuators, the PT1000 temperature sensor is connected to the 8-pin motor connector as standard.
The exact pin assignments are listed in the Mechatronics catalogue in the chapter BHA - Electrical connections.
Here, the motor temperature must be evaluated by a servo controller or external electronics. The same switching
thresholds apply as with the integrated system IHD:
Recommended switching thresholds BHA
Table 21
Sensor type
Unit
Warning
Switch off
PT1000
[C°]
105
115
8. Sealing and protection against corrosion
The performance data and protection class must be observed and the suitability for the conditions at the installation site
must be checked. Suitable design measures must be taken to ensure that no foreign media (water, drilling or cooling
emulsion, chips or similar) can penetrate the housing.
When the connectors and mating connectors are mounted and plugged in, the product achieves the degree of
protection according to the Mechatronics catalogue in the chapter "Technical Data" if the recommended mating
connectors are plugged in and the environmental conditions (liquids, gases, dew formation) do not cause corrosion on
the running surfaces of the radial shaft seals.
Special versions may differ from the above protection class.
Sharp edged or abrasive parts (chips, splinters, metal dust, minerals, etc.) must not come into contact with radial shaft
seals.
A film of liquid permanently standing on the radial shaft seal must be prevented.
Background: As a result of changing operating temperatures, pressure differences occur in the actuator which can lead
to the liquid standing on the shaft seal being sucked in.
Illustration 4
Countermeasure: If necessary, an additional shaft seal on the customer side or a sealing air connection.
Specification sealing air: constant overpressure in the actuator; the supplied air must be dried and filtered. Overpressure
max. 10
4
Pa (0.1 bar).
Deutsch
English
Assembly Instructions Servo Actuators