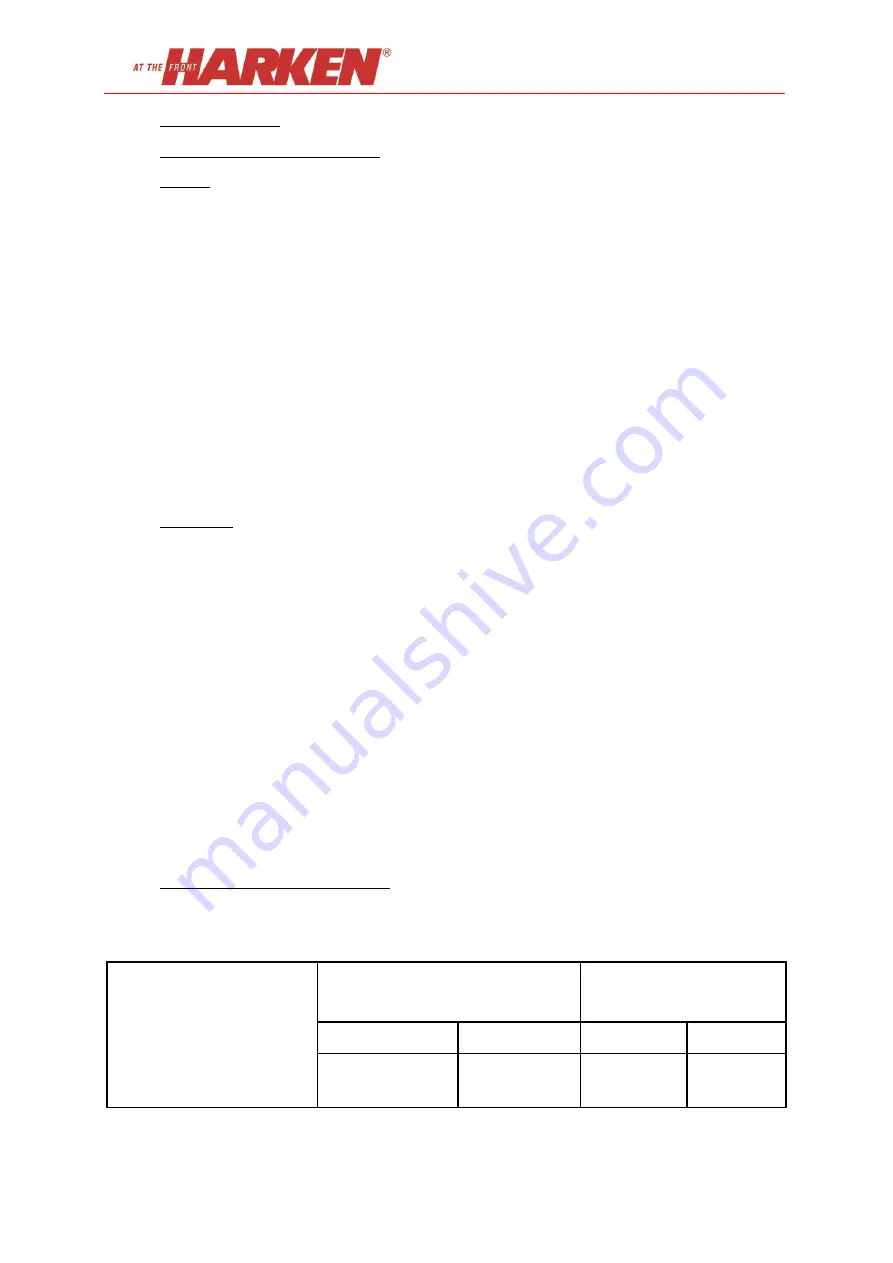
Rev.0
–
19/03/2021
16
9
Motorized use
9.1
Hydraulic equipment (HY)
9.1.1 Motor
Hydraulically operated, Tensioners have a load capacity proportional to the pressure set up
on the manifold, while the recovery speed of the Tensioner is proportional to the oil flow.
The hydraulic motor oil must reflect the ISO VG 46 characteristics. It must be filtered with a
maximum grade of 10 micron and with a contamination level equal to or inferior to class
(according to NAS 1638 or 22/18/15 according ISO/DIN 4406), the temperature range of the
hydraulic oil during operation have to be within 25°C and 90°C.
Motor ports that have to be connected to the manifold are 2 main ports:
-
Size: G 3/8”
-
Depth: 12mm
Motor displacement is 50cc.
9.1.2 Manifold
The Tensioner manifold is plumbed independently and does not rely on the winch for oil flow.
The manifold includes a solenoid valve that should be energized while paying-out (easing
out). The independence of this valve from the Captive winch directional valve, allows to
optimize timing between winch and Tensioner.
The Pay-out circuit includes a pressure-reducing valve, allowing the users to adjust
Tensioner pull force.
During pay-in (trimming in) the Tensioner motor is allowed to freewheel. The pay-in circuit
includes a low-pressure relief valve so the user can adjust drag while trimming in. This is
important when there is no sheet load to help prevent overrides on the winch drum.
All work ports are BSPP type (ISO/DIS1179-1).
All components and work ports are clearly marked with engraved labels.
9.1.2 Manifold performance data
Specifications of the hydraulic motors used to power the hydraulic Tensioner CT0:
Tensioner CT0
recommended pressure range
Max recommended
flow
PSI
bar
gal/min
l/min
From 725 to 2030 From 50 to 140
3,73
14
Summary of Contents for Tensioner CT0
Page 1: ...Rev 0 19 03 2021 1 Tensioner CT0 USER AND MAINTENANCE MANUAL ...
Page 12: ...Rev 0 19 03 2021 12 8 2 Hydraulic Tensioner Outline ...
Page 18: ...Rev 0 19 03 2021 18 9 1 5 Tensioner Manifold structure ...
Page 19: ...Rev 0 19 03 2021 19 9 1 6 Hydraulic Motor connections ...
Page 29: ...Rev 0 19 03 2021 29 10 2 3 Disassemble procedure Step 1 Step 2 Step 3 ...
Page 30: ...Rev 0 19 03 2021 30 Step 4 Step 5 Step 6 ...
Page 31: ...Rev 0 19 03 2021 31 Step 7 Step 8 Step 9 ...