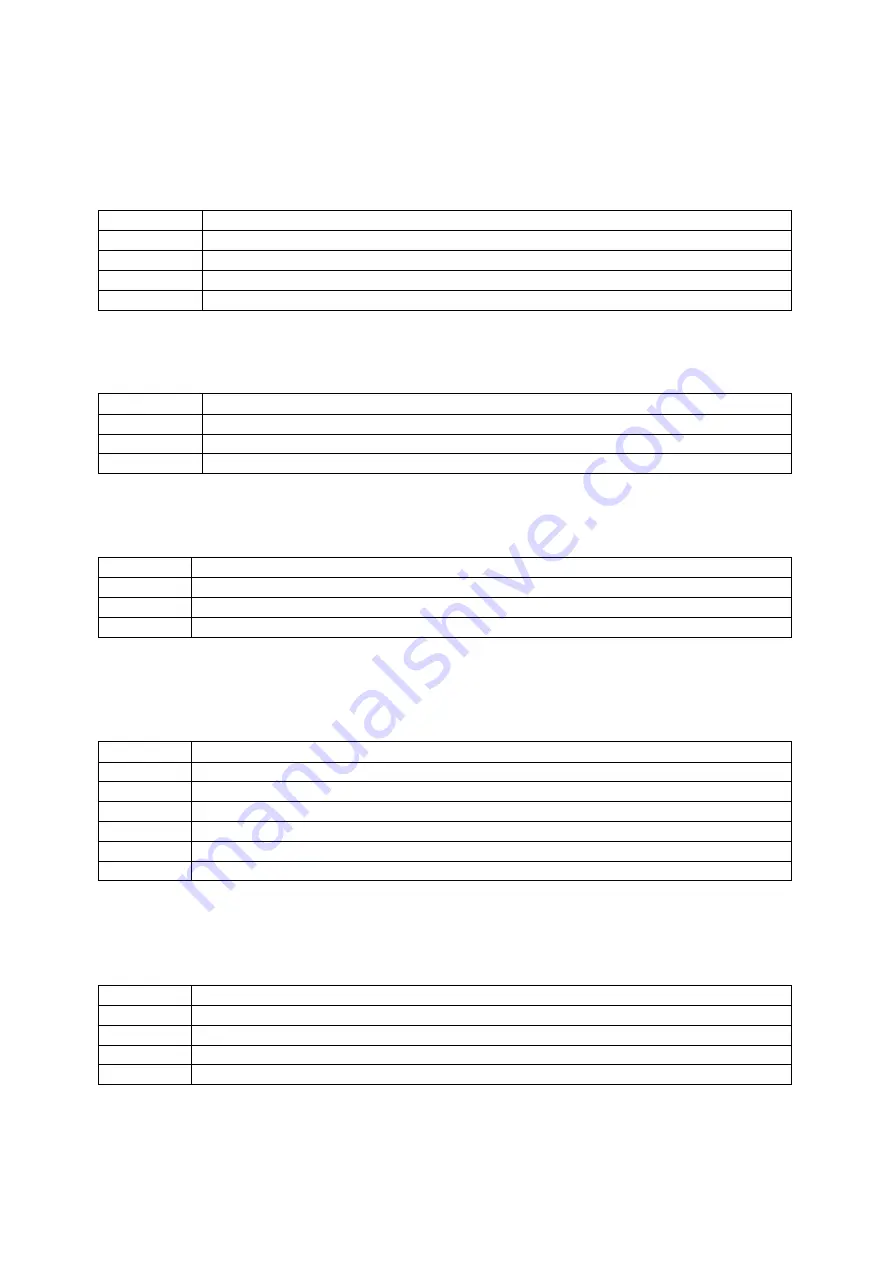
Flowplant Century Pump Manual
TABLE 2.1 CENTURY GEARBOXES
PART NO
DESCRIPTION
105-119
2.7:1 Gearbox Bare Shaft Century
105-120
2.25:1 Gearbox Bare Shaft Century
105-121
2.0:1 Gearbox Bare Shaft Century
105-125
1.86:1 Gearbox Bare Shaft Century
TABLE 2.2 COUPLING FOR CENTURY GEARBOXES
PART NO
DESCRIPTION
100-342
Output Coupling B200 Pt 1, Flex Bore 57 mm, Key 16 mm
100-366
Input Coupling B180 Pt 1, Flex Bore 45 mm, Key 14 mm Perkins 1000 Series
023-594
Input Coupling M200 - Iveco 7000 Series
TABLE 2.3 FLYWHEEL COUPLINGS PERKINS/FORD
PART NO DESCRIPTION
100-633
Coupling PT10 E180 CF - Perkins T6354.4/1006TG
100-367
Coupling PT10 E180 CF - Ford 2726T
023-593
Coupling PT10 E200 - Iveco 7675Si
TABLE 2.4 MOTOR HALF COUPLINGS FOR ELECTRIC MOTORS
(Metric Frame - Non-hazardous Types)
PART NO DESCRIPTION
100-487
37 kW/50 HP Motor Coupling B200 Pt 1
100-487
45 KW/60 HP Motor Coupling B200 Pt 1
023-304
55 KW/75 HP Motor Coupling B200 Pt 1
023-304
75 KW/100 HP Motor Coupling B200 Pt 1
023-304
95 kW/125 HP Motor Coupling B200 Pt 1
023-304
111 kW/150 HP Motor Coupling B200 Pt 1
TABLE 2.5 BELL HOUSINGS
PART NO DESCRIPTION
100-084
Diesel, Century Bell Housing
100-082
Bell Housing 37 kW - 111IkW, Electric
100-329
Adaptor Ring - must be used on 75 - 111kW electric motors
012-186
Adaptor Ring - must be used on diesel engines
27
Summary of Contents for CENTURY
Page 14: ...Section 1 Pump Technical Data 11 ...
Page 25: ...Section 2 Pump Installation 22 ...
Page 32: ...Section 3 General Operating Information 29 ...
Page 47: ...Section 4 Pump Maintenance and Overhaul Procedures 44 ...
Page 68: ...Fig 4 4 Century pump Assembly 65 ...
Page 69: ...66 ...
Page 77: ...Section 5 Warranty 74 ...