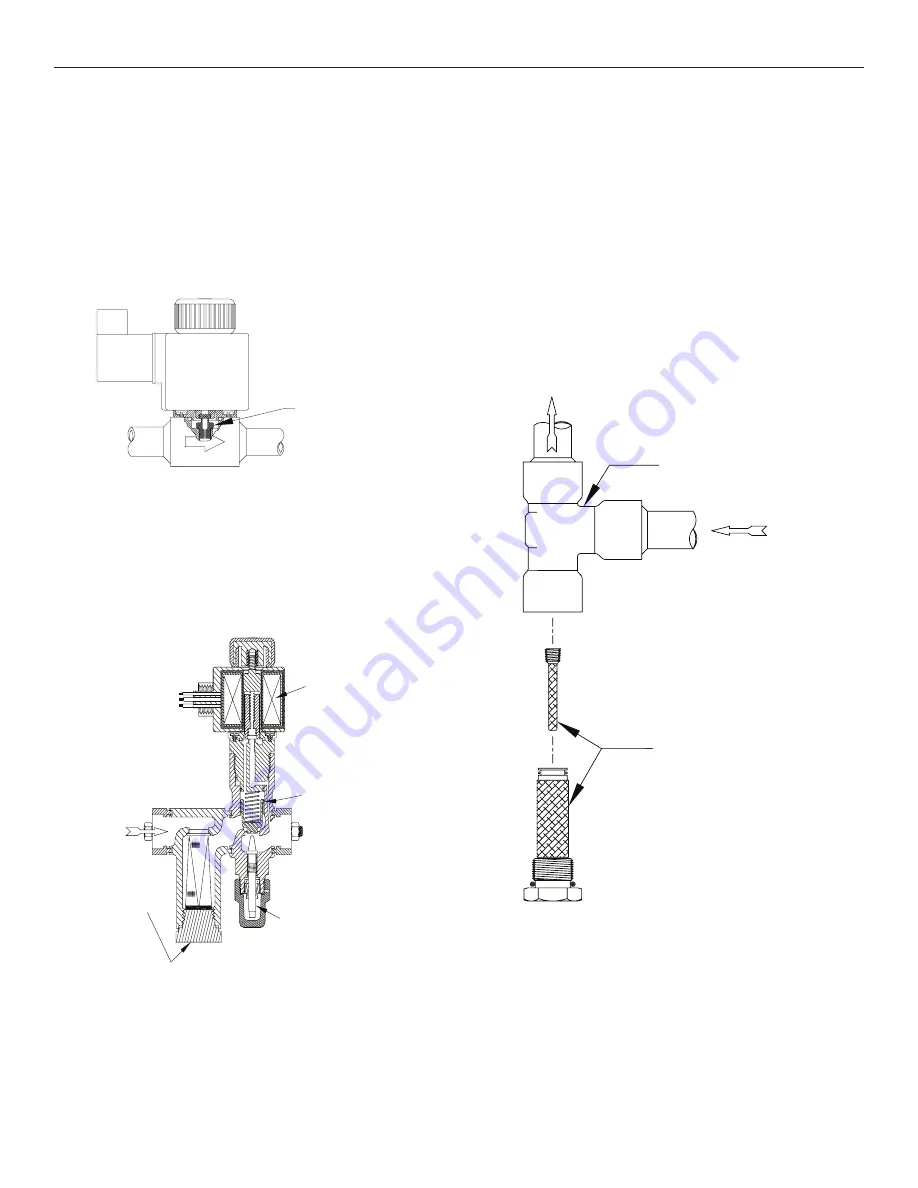
8
APM-001e
AUG 2015
SOLENOID VALVES
The APM is equipped with four solenoid valves. These are:
the liquid drainer solenoid valve (A), the liquid line solenoid
valve (B), the purge gas solenoid valve (C), and the water
solenoid valve (D). See Figure 11. With the exception of the
water solenoid valve, each is directly welded in-line and
has a stainless steel removable seat/orifice (see Figure 8).
The removable seat/orifice facilitates easy access to the
orifice for inspection or replacement. If necessary, the
water solenoid valve (D), whose brass body has threaded
ends, can easily be replaced or parts thereof changed.
Figure 8
LIQUID DRAINER
The liquid drainer removes any condensed liquid that trickles
from the foul gas line into the purger. This enables the
purger to always be condensing gas, rather than having
liquid entering the condensing section of the purger and
limiting proper operation. The drainer solenoid valve (A)
will open to empty a reasonable amount of excess liquid
directly to the flooded evaporator. However, if too much
liquid comes down the foul gas line, due to improperly
piped condensers, corrective action must be taken. See
the Foul gas piping section on page 3.
STRAINER/ORIFICE
The strainer/orifice meters condensed liquid refrigerant
from the high-pressure side of the purger into its flooded
evaporator. It features a dual filter arrangement to reduce
potential orifice blockage. This dual filter (strainer) removes
particles and houses the integral orifice (strainer/orifice
screen assembly). See Figure 10.
In addition, separate remote point solenoid valves are
required, one for each enabled purge point. These are not
included with the APM. The Hansen type HS8 solenoid
valve having a ½” (13mm) port and a stainless steel piston
is recommended. Below is a typical purge point solenoid
valve with close-coupled strainer (Figure 9).
Figure 9
REMOVABLE
SEAT/ORIFICE
CHECK VALVES
There are three check valves on the purger. An 80 psid
(5.5 bar) differential check valve is installed on the purge
gas line to prevent any possibility of reverse flow of water
into the purger. A 225 psid (15.5 bar) differential relief
check valve leads from the condensing coil inlet to the
suction line; this prevents excessive purger pressure. A
third check valve is installed from the liquid drainer to the
evaporator coil to prevent reverse flow with a temporary
loss of foul gas pressure.
WATERTIGHT
ENCAPSULATED
COIL
STAINLESS
STEEL PISTON
MANUAL OPENING
STEM
CLOSE-COUPLED
STRAINTER
REMOVABLE SEAT
ORIFICE
WATER BUBBLER
The APM is equipped with a water bubbler which eliminates
any water bottle attention. Purge gas (noncondensibles)
from the purger flows into the bottom of the water bubbler
where residual ammonia can be absorbed into the water.
The water with absorbed ammonia flows to a drain. The
water solenoid valve (D) opens to automatically replenish
water to the bubbler each time the purge gas solenoid
valve (C) energizes. A 30-second delay keeps the water
solenoid valve (D) open after the purge gas solenoid valve
(C) de-energizes to refill water bubbler. Proper release of
noncondensibles through the bubbler is usually indicated
by large, 1/2" (13mm) diameter bubbles.
STRAINER/ORIFICE
SCREEN ASSEMBLY
STRAINER/ORIFICE
BODY
STRAINER/ORIFICE
BODY
STRAINER/ORIFICE
SCREEN ASSEMBLY
SECTION 2 ELECTRICAL INSTALLATION & OPERATION
Figure 10