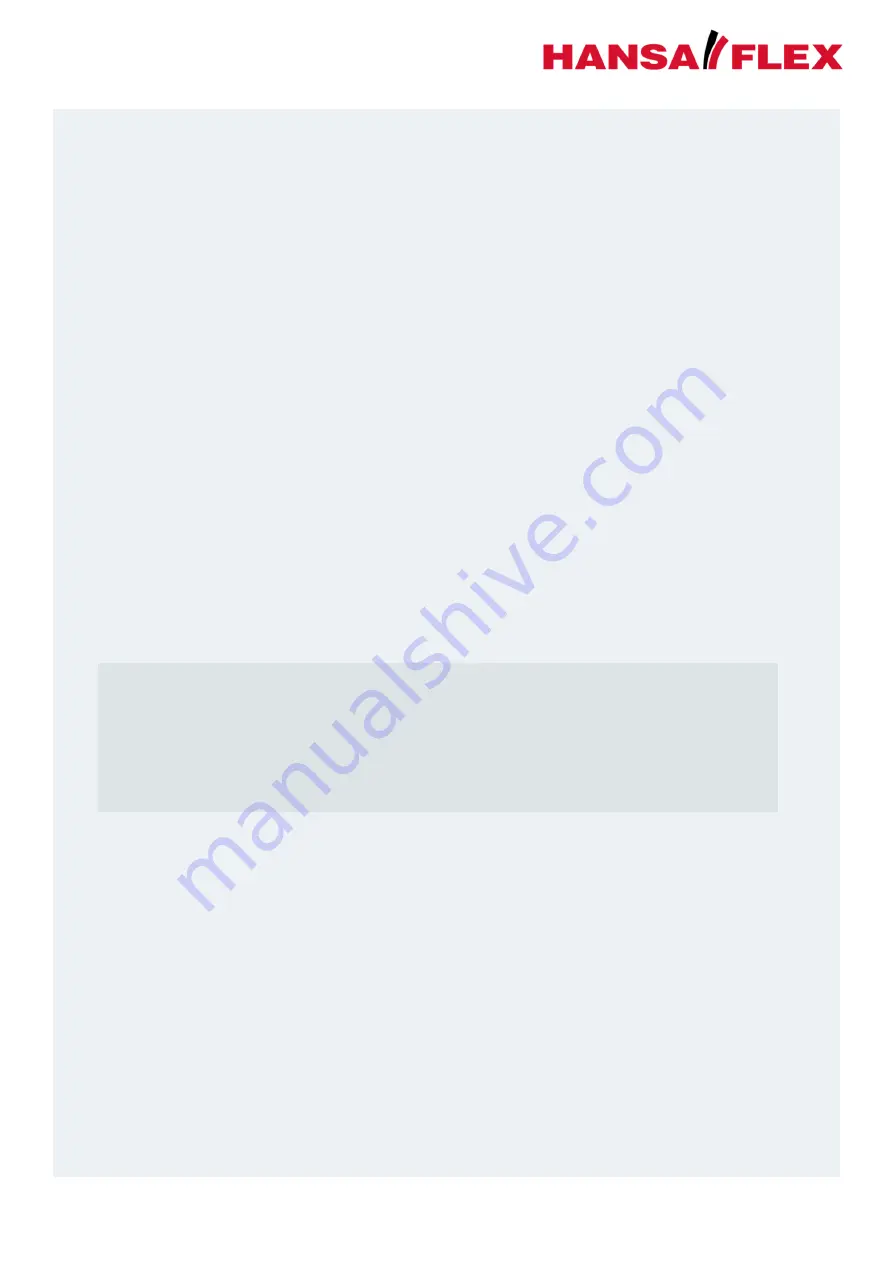
Valid from: 15.02.2021 / Source: VAM-UM-00551-EN-04
Despite careful checking, we cannot exclude the possibility of errors in this document and we accept no liability for the information it contains.
Page 15
Test sequence
1.
The power meter (4) is connected on the input side (IN) to the pressure line of the pump (1),
which is safeguarded by means of a pressure relief valve (PRV) (3).
2.
With a fully opened loading valve (4.3), the hydraulic oil is returned to the tank on the
output side (OUT). Please note the value displayed on the scale (4.4) of the volume flow
meter [l/min] (LPM). Observe the pressure [bar] on the pressure gauge (4.1).
3.
Slowly closing the loading valve (4.3) generates a steadily rising load pressure p that is
displayed on the pressure gauge (4.1) / ((3.1) if present) in [bar].
4.
The volume flow Q of the pump is now displayed as a function of the load pressure (4.1) on
the scale of the volume flow meter (4.4) in [l/min] (LPM).
5.
As the load pressure (4.1) starts to get close to the pressure that is currently set for the PRV
(3), some of the volume flow from the pump starts to flow into the tank via the PRV (3).
6.
The value displayed on the scale (4.4) of the volume flow meter reduces.
7.
Increase the set value for the PRV (3). Keep an eye on the scale (4.4), the value displayed on
the volume flow meter will increase roughly up to the value noted in step 2.
8.
Repeat steps 3-6 above until the volume flow that is noted under step 2 is achieved as a
function of the max. desired system pressure (3.1) / (4.1).
Please note:
Note the specifications of the pump (slipping/leakage) and the performance of the pressure
relief valve (early opening, p/Q characteristic curves).
In practice, the system PRV is generally set approx. 10-20 bar higher than the max. load
pressure. The documentation from the manufacturer of the hydraulic system/component
should be noted.