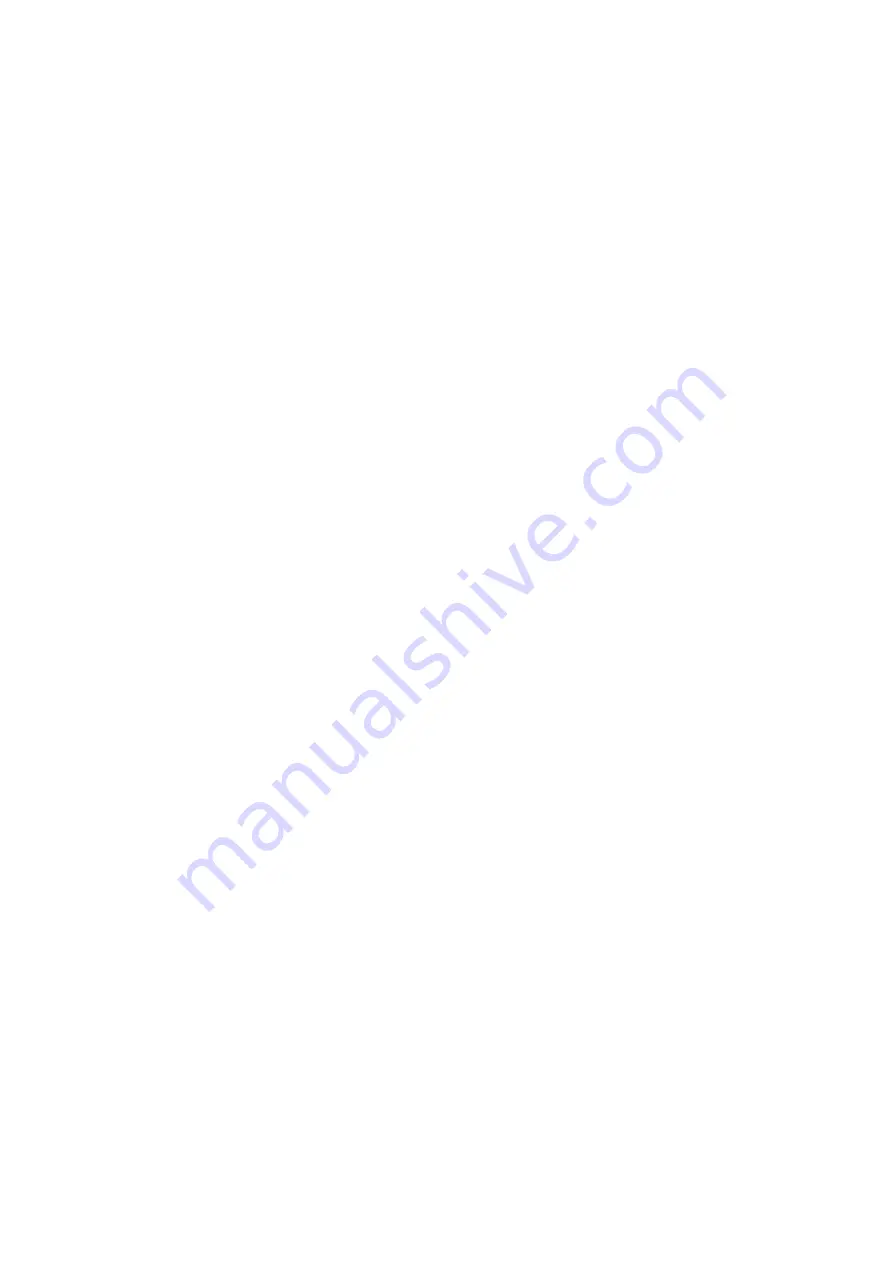
69
14. The use, Install and Safety Rules of attachment
HANGCHA will choose attachment that according with International standard ISO2328
《
Forklift
pothook fork and install size of carriage
》
,such as clamp, rotator, paper roll clamp, carrying ram,
side-shifter ect.
Attachment use
–
Know well the content of nameplate on attachment, read the instruction manual before
–
Usage.(Especially the manual from attachment company)Before operate the attachment, the
people should be trained and obtain the qualification.
–
It should be understand the basic capability and operate methods of attachment. Especially
the admit load, lift height, size of cargo and adapt range of attachment.
–
Operate the multi-functional attachment, such as with side-shifter, clamp or rotator, it is not
allowed that two action at one time. Operate one functional then do another one.
–
Prohibit the cargo at a high position when truck move with attachment. If the size of cargo is
too big, prohibit the truck move on. Transport the cargeo, make sure that the distance of
bottom of cargo and ground is less than 300mm and mast incline back.
–
The weight of cargo couldn‟t exceed the limited value of combination carrying capacity of
forklift and attachment. It is not allowed that partial load at high position. It is a short time work
for attachment with side-shifter. Partial load is around 100mm (Above 5 ton (including 5
ton),the side-shifter movable within 300mm.
–
In the range of the projection forth 2m of the lower of attachment and cargo, prohibit stand to
avoid the suddenness except the driver position under overhead.
–
It is not allowed that an emergency brake in moving. Run slowly with load.
–
Prohibit outside force when attachment working.
–
It couldn‟t be use at malfeasance situation and overstep normal work range.
–
When the attachment failure, prohibit use without check.
Check and maintenance:
–
Check the clearance of carriage beam and below catch of attachment if accord the
attachment manual.
–
Check the rise catch is right on the flute of fork carriage.
–
Use the auto currency lithic-grease per 500 hours to bearing surface.
–
If the tighten firmware become flexible.
–
Check the tie-in of hydraulic pressure loop, if tube attaint. Prohibit use after repair.
–
Check the drive of attachment timing or turn the component if fray or block, change betimes.
–
Check each element if in normal under load attachment is work in gear. If not, check the
hydraulic pressure loop, find out the broken part, change air poof or whole loop part.