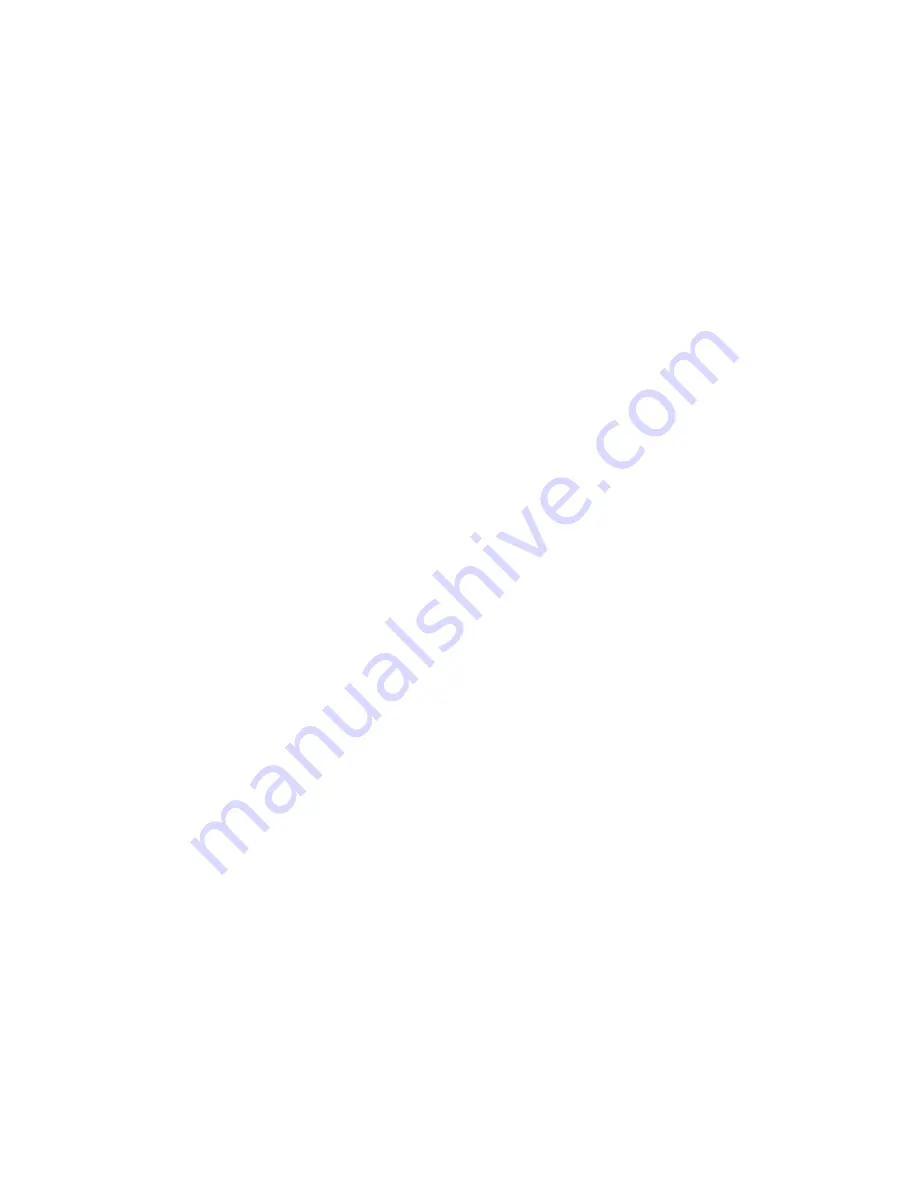
Figure 1
Frame
ITEM #
PART #
DESC.
1
GM72
Frame
2
GM73
Hitch Shaft
3
GM74
Hitch
4
GM396
Jack
5
12N13
Jack Pin & Chain
6
T151
1" Nut
7
GM76
Tank Side Support
8
GM77
Tank Back Support
*
F97
SMV Bracket
9
GM78
Oil Tank Bracket
10
GM79
Spindle
11
B90
Seal
12
B91
Inner Bearing
13
B91A
Inner Race
14
26G5A
Stud 5/8"-18
15
26G4A
Hub (821)
16
B94A
Outer Race
17
B94
Outer Bearing
18
B4
Washer
19
B3
Nut
20
B31
Cotter Pin
21
B2
Hub Cap
22
RG73
Wheel (W-51350)
*
GM394
Tire (15 X 12.5L 20 Ply)
23
26G6A
Lug Nut 5/8"-18
24
GM80
1" x 5" GR 5 Bolt
25
DWM171
1" Lock Washer
26
GM397
Flow Control Bracket
27
GM398
Screen Holder
28
X193
Latch Keeper
29
X192
Rubber Latch
30
X194
Latch Mounting Bracket
31
X195
Latch Pin
32
GM399
Screen Holder Strap
33
B10
1/2" x 4" GR. 5 Bolt
34
G89
Grease Zerk (#1641)
35
GM424
1/4"-28 Grease Line Adapter
36
GM440
Grinder Hose Holder
37
42N2
PTO Holder
38
42N3
Spring (MB1000-035)
39
GM183
3/4" X 4-1/2" GR 5 Bolt
40
GM417
3/4"-10 Nut
41
RG199
3/4" Lock Washer
-53-
Summary of Contents for GM 170
Page 6: ... 4 ...
Page 8: ... 6 ...
Page 11: ... 9 SAFETY INFORMATION ...
Page 12: ...SAFETY INFORMATION 10 ...
Page 13: ...SAFETY INFORMATION 11 ...
Page 14: ...SAFETY INFORMATION 12 ...
Page 16: ... 14 ...
Page 53: ...SERVICE PARTS NOTES 51 ...
Page 81: ... 79 ...
Page 82: ...FIGURE 20 OPTIONAL LIGHTS FENDER 1 2 3 4 5 6 7 7 7 7 8 8 9 9 10 11 11 12 80 ...