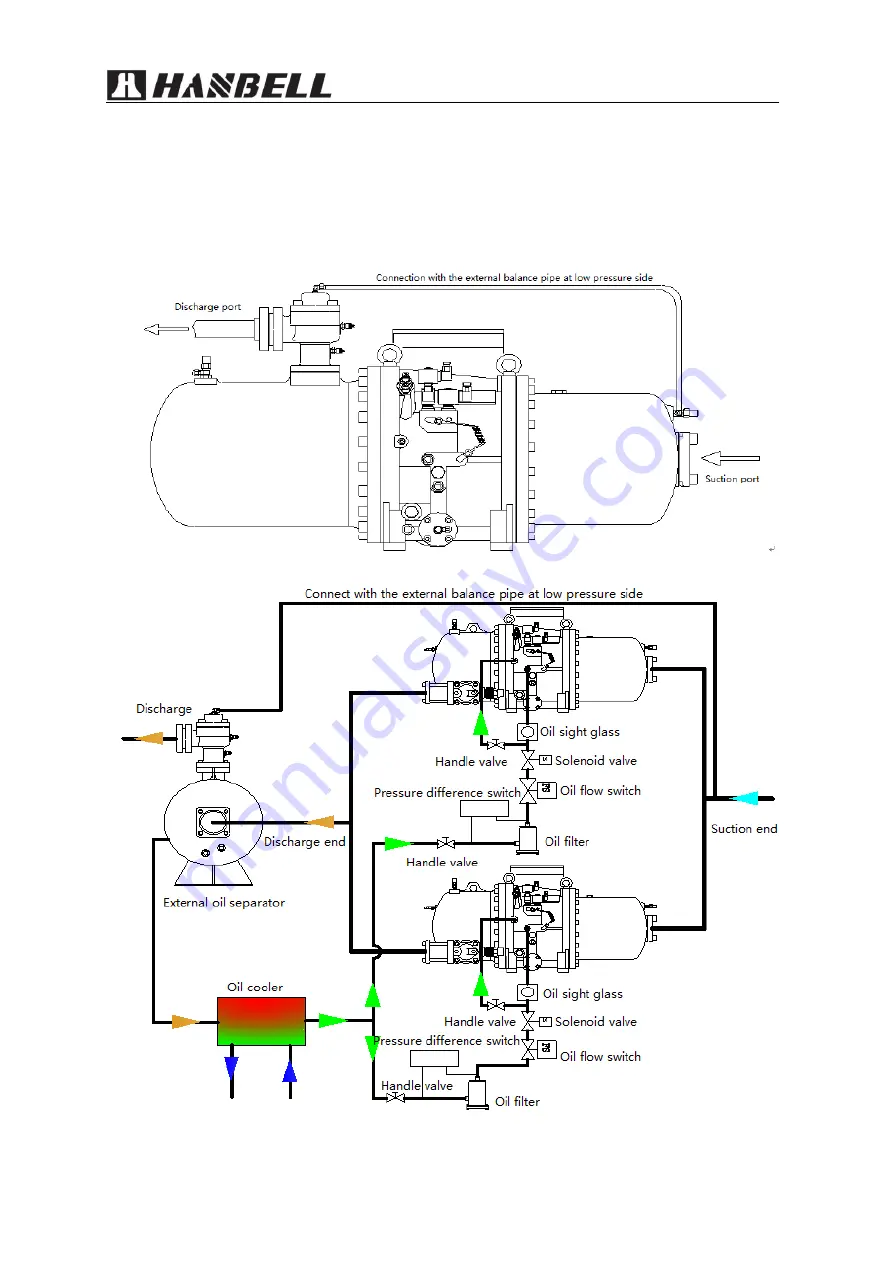
RC2-D Technical Manual
33
7.2
Application of pressure maintaining valve
When the difference between oil pressure and suction pressure is less than 4 bars, it may lead to
capacity-control system failure, insufficient lubrication, and serious damage to the compressor, so the
pressure maintaining valve is recommended to be installed. In addition to the installation of pressure
maintaining valve, it is also recommended to install high and low pressure difference switches. If
necessary, please contact hanbell for specific information.
Application of pressure maintaining valve - Single compressor
Application of pressure maintaining valve - Parallel connection
Summary of Contents for RC2-D
Page 27: ...RC2 D Technical Manual 2 RC2 200 470 D S P terminal box 3 RC2 510 930 D S P terminal box ...
Page 45: ...RC2 D Technical Manual 47 RC2 180D S Drawing ...
Page 46: ...RC2 D Technical Manual 48 RC2 200 620D S Horizontal suction port Drawing ...
Page 48: ...RC2 D Technical Manual 50 RC2 620 930D S Vertical suction port Drawing ...
Page 49: ...RC2 D Technical Manual 51 10 2 RC2 100 930D P Drawing RC2 100 140D P Drawing ...
Page 50: ...RC2 D Technical Manual 52 RC2 180D P Drawing ...
Page 51: ...RC2 D Technical Manual 53 RC2 200 620D P Drawing ...
Page 53: ...RC2 D Technical Manual 55 RC2 620 930D P Drawing ...