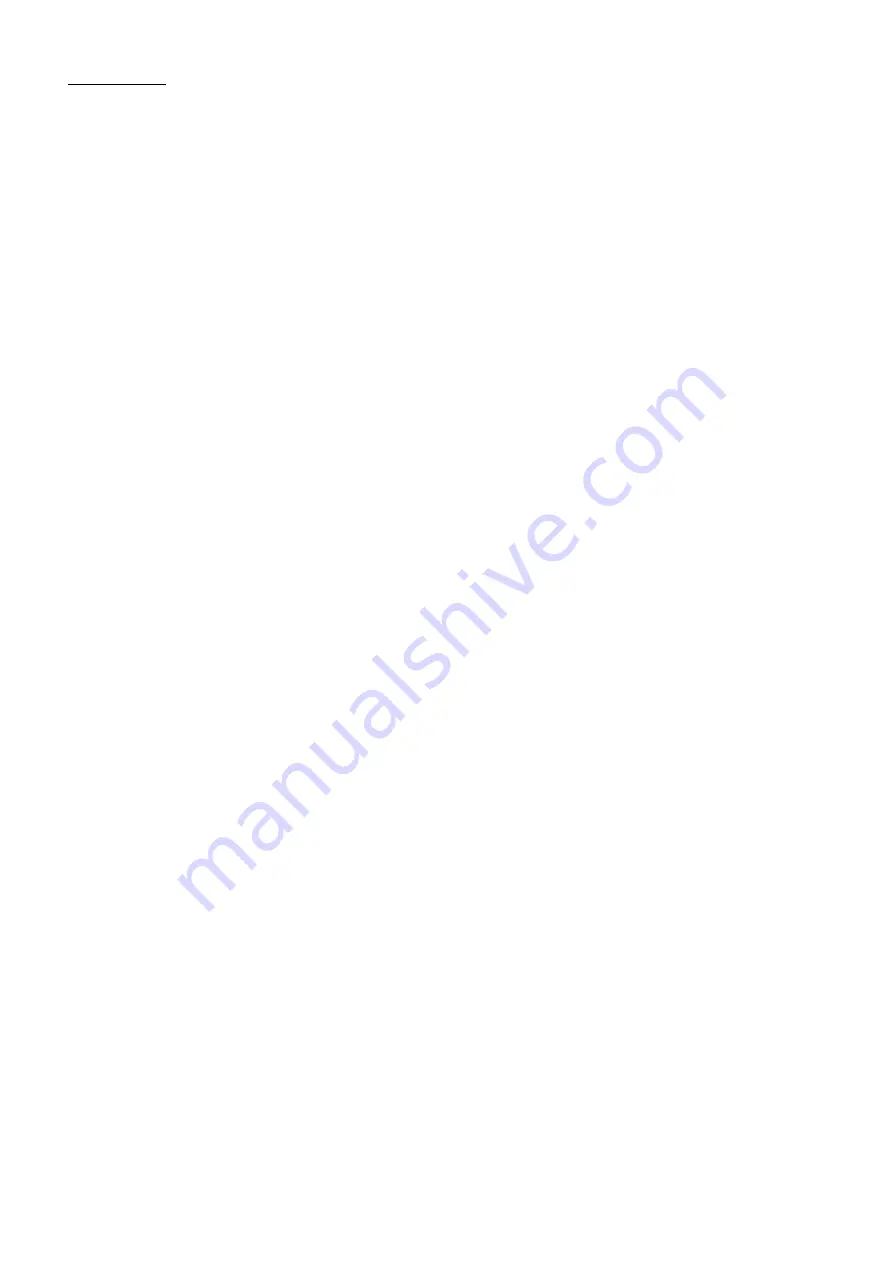
HAMWORTHY HEATING LTD
30
SHERBORNE
500001167/E
10 SERVICING
A competent person, registered for working on non domestic gas appliances, should check & ensure that the flue, its
support & terminal, the ventilation to the boiler house, safety valve, drain, water filter if fitted, pressure gauge, etc.; are in a
serviceable & working condition & still comply with the relevant standards & codes of practice - see Section 4.
Regular servicing is recommended preferably by a Hamworthy appointed person & at least annually, to ensure trouble
free operation. For Sherborne, HHL would recommend an additional 6 monthly examination following commissioning,
acknowledging site conditions & running hours. Although cleaning of flueways may not be necessary on a yearly basis, it
is important that all controls & safety features are checked for correct operation.
Note:- Measuring flue gas CO
2
& gas temperatures will give an indication of the state of the boiler flueways & waterways.
Results should be compared with previously measured values to establish possible loss of efficiency.
Should remedial work be carried out on a module, then the non-firing module must be electrically isolated so as to prevent
accidental operation in the event that the installation is required for ongoing heating requirements.
10.2 Annual Service
10.2.1 Preliminary Checks & Cleaning
The procedure
MUST
be carried out on
ALL
individual modules which constitute an installation.
•
Isolate all electrical supplies
•
Turn off the gas service valve
•
Remove the screw on the bottom of the cover & pull the cover up & off the hooks on the wall frame.
•
Unplug the condensate trap and clear out any debris found
•
Disconnect all the electrical from the control panel & the air pressure hose from the condensate trap
•
Remove the 2xM10 nuts & washers securing the control panel to the heat exchanger & remove it.
•
Disconnect the pressure feedback tube from the gas valve.
•
Remove the 4 screws/nuts securing the fan/venturi/gas valve assembly to the transition duct.
•
Withdraw the assembly from the air inlet duct.
•
Remove the 2 screws securing the venturi/gas valve assembly to the fan. Cleaning impellor & venturi tube
with a soft brush if necessary.
•
Remove the 2 nuts securing the burner to the heat exchanger & carefully remove the burner assembly.
•
Remove the single socket cap head screws securing the igniter & flame probe to the burner flange.
•
Withdraw the igniter & probe.
•
Remove the loose flange & Mica sight glass noting the position for re-assembly.
•
Check condition of the igniter assembly & probe for damage, clean or replace as required.
•
Remove the 2xM6 nuts securing the transition duct to burner & separate the components.
•
Check the burner & clean using a soft brush if required (if possible use compressed air to blow out the dust
inside the burner tube). Alternatively the burner tube can be washed using a soapy water solution.
•
Tap the burner flange firmly downwards on a block of wood to dislodge residual debris from inside the burner
tube. A damaged burner should be replaced.
•
Re-assemble in reverse order checking the condition of gaskets & replace if necessary.
•
Fit the igniter & probe to the burner flange to check the respective positions - See section 11.1.
•
Refer to Section 7 & test all gas joints broken or disturbed for soundness before firing.
•
Carry out a combustion check by testing the flue gas CO
2
& CO levels as detailed in Section 7.
10.2.2 Heat Exchanger Cleaning
The heat exchanger should be cleaned using the following procedure at least every 4 years. It may be necessary to carry
out this procedure more regularly. Measuring flue gas CO
2
& gas temperatures will give an indication of the state of the
boiler flueways & waterways. Results should be compared with previously measured values & values shown in the
appendix c of this manual to establish the necessity for heat exchanger cleaning.
10.2.2.1 SE64he
If a high pressure hose is available then the following procedure can be used:
•
Support the sump & remove the 4xM6 securing nuts. Lower the sump to expose heat exchanger & baffles.
•
To clean the heat exchanger(s), the use of a high pressure water hose (40-80 psi) is recommended with the
resultant discharge being collected in a suitable receptacle.
•
Using the high pressure hose, insert the cleaning nozzle into the burner opening. Switch on the pump &
traverse the full length & circumference of the heat exchanger to remove any deposits.
If a high pressure hose is not available then the SE71c procedure must be used.
Summary of Contents for Sherborne Series
Page 2: ......
Page 10: ...HAMWORTHY HEATING LTD 8 SHERBORNE 500001167 E 4 Boiler Layout Description 4 1 Accessory Pack...
Page 27: ...HAMWORTHY HEATING LTD 25 SHERBORNE 500001167 E...
Page 29: ...HAMWORTHY HEATING LTD 27 SHERBORNE 500001167 E 8 9 Wiring Diagram...
Page 30: ...HAMWORTHY HEATING LTD 28 SHERBORNE 500001167 E 8 10 Wiring Diagram LMU...
Page 53: ......
Page 54: ......