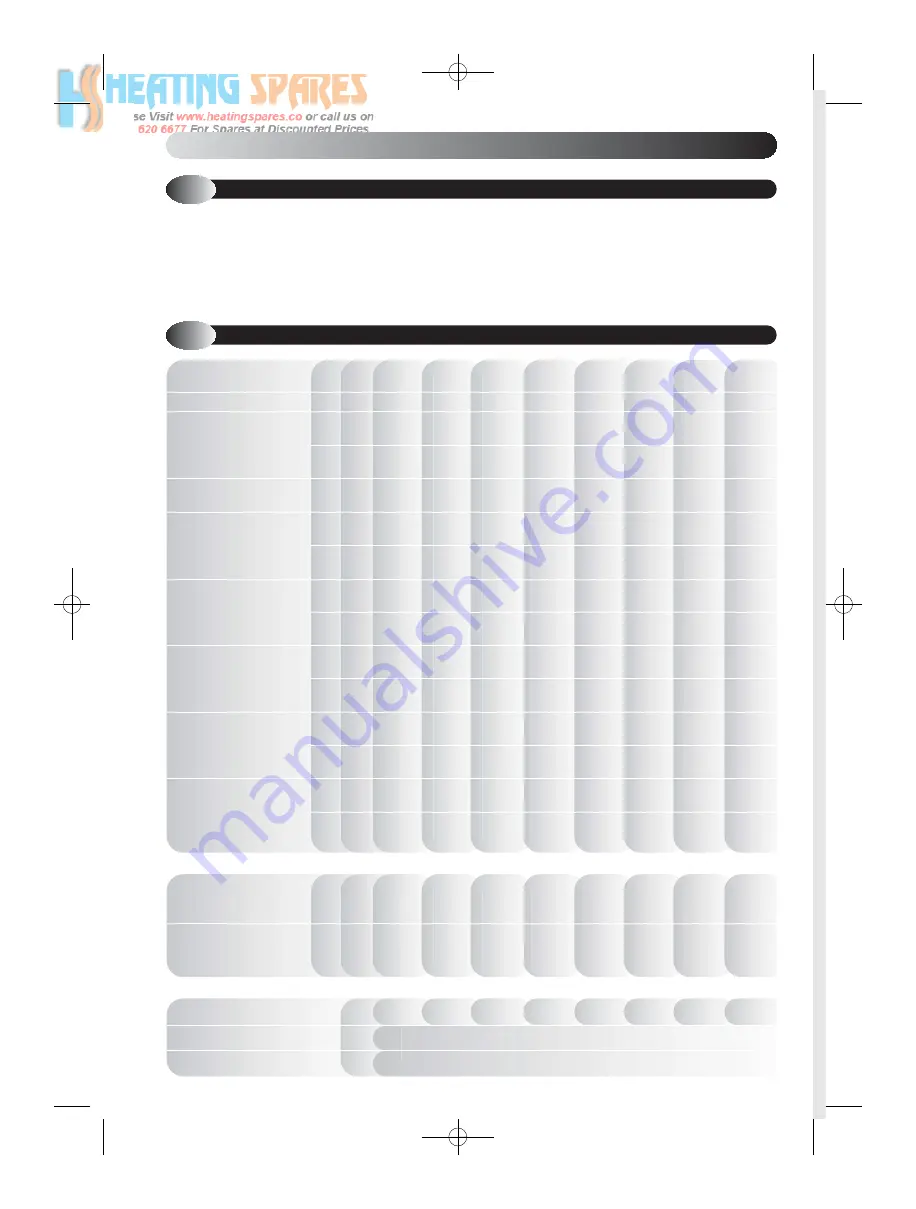
Supplied By www.heating spares.co Tel. 0161 620 6677
2
TECHNICAL SPECIFICATIONS
GAS CATEGORIES
2.1
PERFORMANCE DATA
2.2
These appliances are certified to comply with the requirements of EN
483, EN 677, and EN 625 for use in GB and IE (Great Britain and Ireland)
using the following gas categories:
Eden CBX 38, Eden CBX 32, Eden CBX 24, Eden SBX 30:
II
2H3P
(G20 with a governed gas supply at 20 mbar (8 in.wg) inlet
pressure).
Eden CBX 38 Propane, Eden CBX 32 Propane,
Eden CBX 24 Propane, Eden SBX 30 Propane:
II
2H3P
(G31 (Propane) with a regulated gas supply at 37 mbar (14.9 in.wg)
inlet pressure).
The appliance classification (as defined in EN 483) may be any of the
following depending on the chosen flue option: C
13
, C
33
, C
53
, or B
23
Appliance
CBX38
CBX32
CBX24
SBX30
CBX38
CBX32
CBX24
SBX30
Propane
Propane
Propane
Propane
Mode
Rate
Central Heating Output
Max
kW
30.0
24.0
18.0
30.0
30.0
24.0
18.0
30.0
(non-condensing)
(Btu/h) (102400)
(81900)
(61400)
(102400)
(102400)
(81900)
(61400)
(102400)
(80 - 60 °C)
Min
kW
9.0
7.9
5.9
8.2
9.0
7.9
5.9
8.2
(Btu/h)
(30700)
(27000)
(20100)
(28000)
(30700)
(27000)
(20100)
(28000)
Central Heating Output
Max
kW
32.1
25.7
19.3
32.1
32.1
25.7
19.3
32.1
(condensing) (50 - 30 °C)
(Btu/h) (109500)
(87700)
(65900)
(109500)
(109500)
(87700)
(65900)
(109500)
Net
kW
30.6
24.5
18.4
30.4
30.6
24.5
18.4
30.4
Central Heating Input
(Btu/h) (104440)
(83600)
(62800)
(103700)
(104440)
(83600)
(62800)
(103700)
Max Rate
Gross
kW
34.0
27.2
20.4
33.8
33.2
26.6
20.0
33.0
(Btu/h) (116000)
(92800)
(69600)
(115300)
(113400)
(91000)
(68300)
(112700)
Net
kW
9.2
7.3
5.5
7.6
9.2
7.3
5.5
7.6
Central Heating Input
(Btu/h)
(31400)
(24900)
(18800)
(26000)
(31400)
(24900)
(18800)
(26000)
Min Rate
Gross
kW
10.2
8.2
6.1
8.4
10.0
7.9
6.0
8.3
(Btu/h)
(34800)
(28000)
(20800)
(28600)
(34000)
(27000)
(20500)
(28300)
Max
kW
38.0
32.0
24.0
38.0
32.0
24.0
Domestic Hot Water Output
(Btu/h) (129600)
(109200)
(81900)
(129600)
(109200)
(81900)
Min
kW
9.0
7.9
5.9
9.0
7.9
5.9
(Btu/h)
(30700)
(27000)
(20100)
(30700)
(27000)
(20100)
Net
kW
38.8
32.7
24.5
38.8
32.7
24.5
Domestic Hot Water Input
(Btu/h) (132300)
(111600)
(83600)
(132300)
(111600)
(83600)
Max rate
Gross
kW
43.1
36.2
27.2
42.1
35.5
26.6
(Btu/h) (146900)
(123500)
(92800)
(143600)
(121000)
(90800)
Net
kW
9.2
7.3
5.5
9.2
7.3
5.5
Domestic Hot Water Input
(Btu/h)
(31400)
(24900)
(18800)
(31400)
(24900)
(18800)
Min rate
Gross
kW
10.2
8.2
6.1
10.0
7.9
6.0
(Btu/h)
(34800)
(28000)
(20800)
(34000)
(27000)
(20500)
Central Heating Gas Rate
m3/h
3.24
2.59
1.95
3.22
(after 10 min operation - hot)
Max (ft3/h)
(114.4)
(91.5)
(68.9)
(113.7)
kg/h
2.2
1.9
1.43
2.36
Domestic Hot Water Gas Rate
m3/h
41.0
3.46
2.59
(after 10 min operation - hot)
Max (ft3/h)
(144.8)
(122.2)
(91.5)
kg/h
2.8
2.55
1.9
Seasonal Efficiency
%
90.2
90.8
90.2
90.4
92.3
92.2
92.2
92.4
Seasonal Efficiency (SEDBUK)
Band
“A”
Nox Classification
Class
“5”
2
751030 MANUAL (NEW) 21/9/10 08:39 Page 6