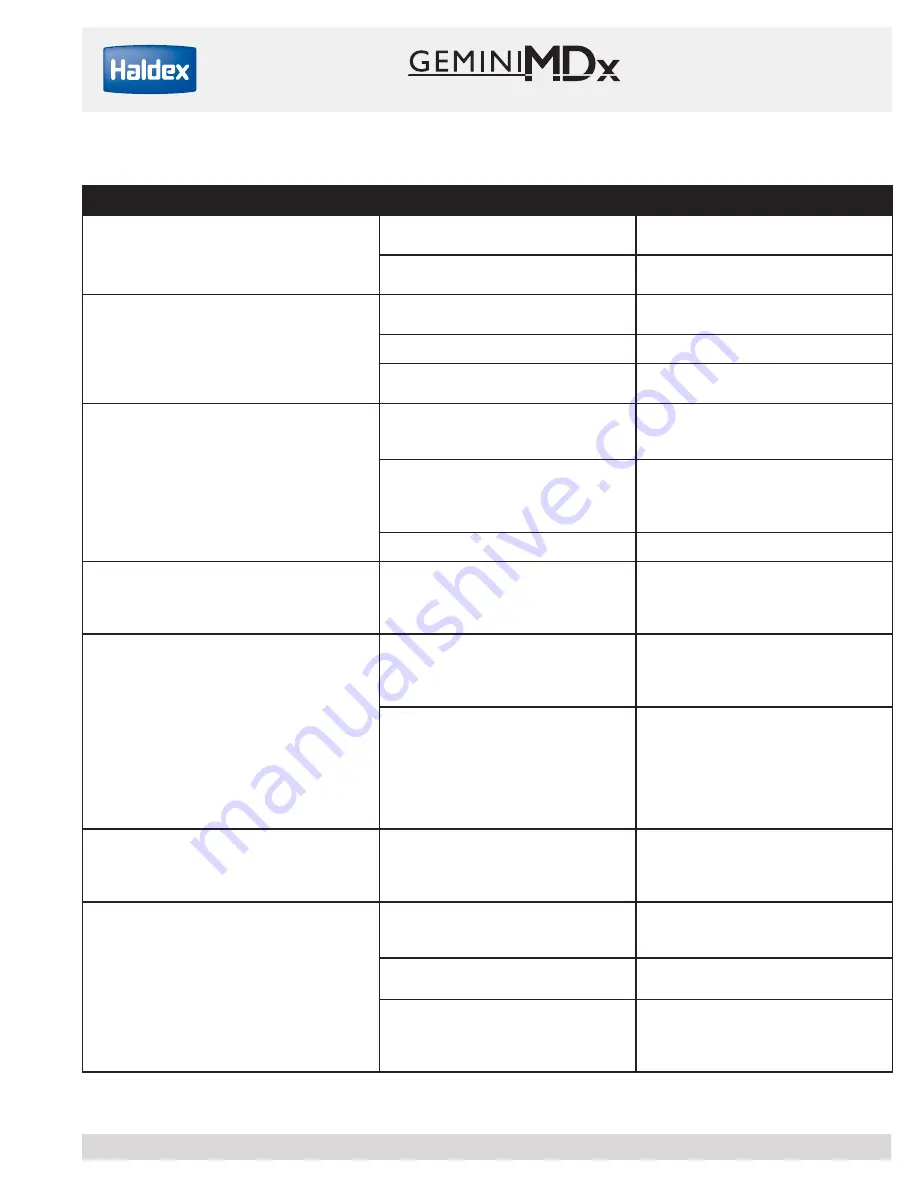
DUAL DRYER SYSTEM
INSTALLATION/SERVICE
MANUAL (L31279)
®
Troubleshooting
PROBLEM
CAUSE
REPAIR
Water in air system
Contaminants in desiccant
Change cartridge canister. Check
compressor for excessive oil passage.
Leaks in air system
Tighten air connections, soap
connection and recheck for leaks.
Excessive compressor cycling
Excessive leaks in air system
Tighten air connections, soap
connection and recheck for leaks.
Defective dryer outlet check valve
Clean check valve seat and replace.
Undersized compressor; duty cycle of
compressor should not exceed 25%
Reduce air demand or install greater
output compressor.
Safety valve is open
Cartridge canister is plugged
Excessive oil passage from compressor.
Check for worn compressor, replace if
necessary. Replace cartridge canister.
Ice block in air dryer
Check heater function. Check electrical
power to heater assembly. Refer to
Operational Check Section Page 12.
Replace heater assembly, if necessary.
Excessive system pressure
Repair or replace air governor.
Poor drying efficiency
Air at inlet of dryer exceeds 170°F
Extend length of compressor discharge
line.
The 170°F dryer inlet temperature
can usually be accomplished with 12’ to
15’ of compressor discharge line.
Short life of air dryer or cartridge canister
Air at inlet of dryer exceeds 170°F
Extend length of compressor discharge
line.
The 170°F dryer inlet temperature
can usually be accomplished with 12’ to
15’ of compressor discharge line.
Duty cycle of compressor does not allow
for sufficient time for desiccant regener-
ation
During normal operation the compressor
must remain unloaded for a minimum of
30 seconds to allow for sufficient purge.
Lengthy loading times must be avoided.
Air dryer must be “bypassed” in
applications with high air use such
as bulk unloading.
Water, oil or a mixture of both are present in air
system
Desiccant contaminated with oil
Inspect, clean or replace cyclone insert in
Consep. Replace cartridge canister. Drain
all air tanks. Inspect compressor for
correct operation.
Air pressure will not “build up”
Air leak from purge valve
Not a serviceable item. Refer to Valve Unit
with Integrated Purge Valve Section on
Page 19. Replace valve unit assembly.
Governor not operating
Check operation of governor and
replace if necessary.
Ice block in air line, Consep or dryer
Check heater function. Check electrical
power to heater assembly. Refer to
Operational Check Section Page 12.
Replace heater assembly, if necessary.
Page 13