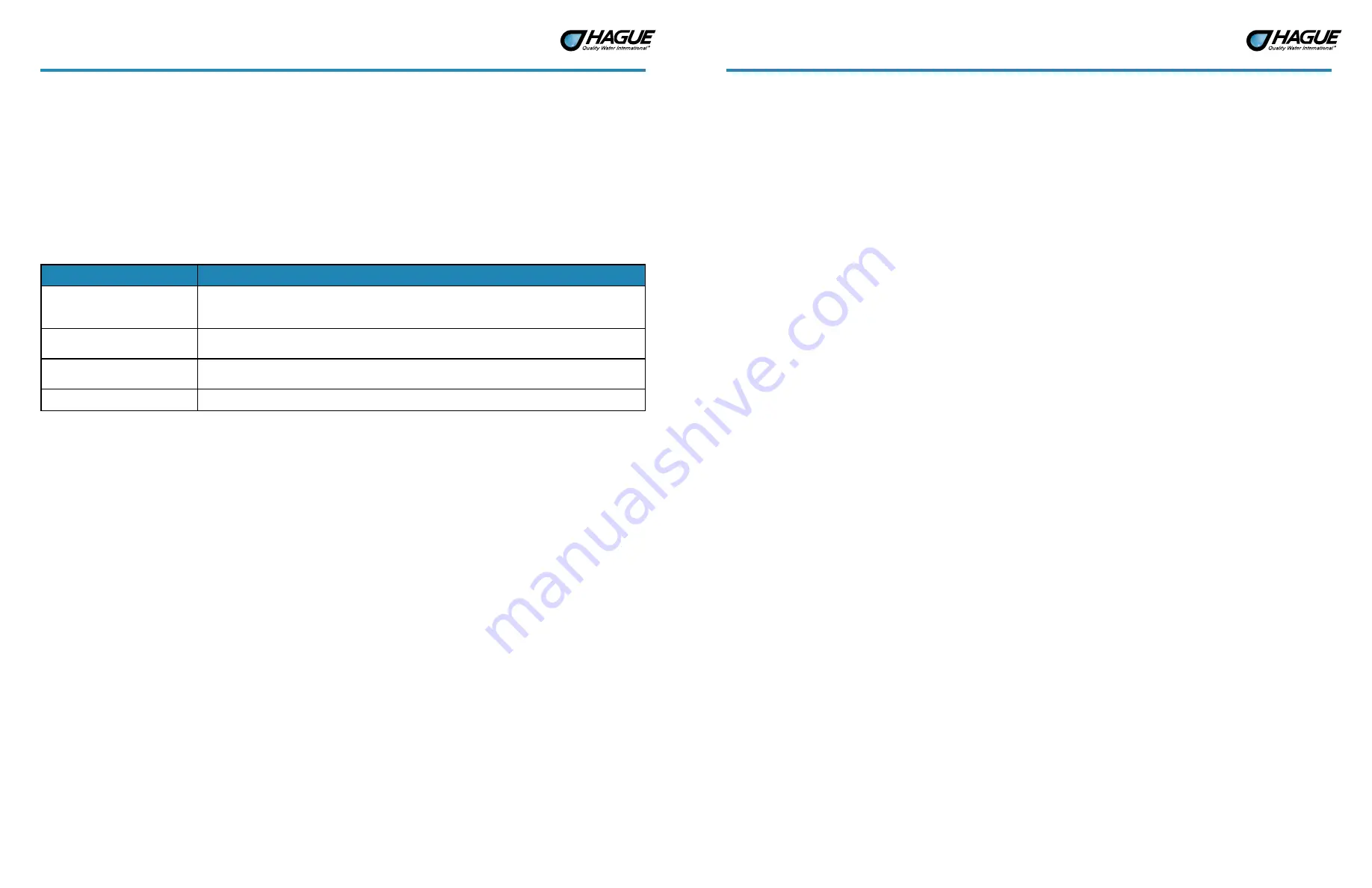
6
7
Checklist Before Installation
See this checklist before installation.
Water Quality —
If the water supply contains sand, sulfur, bacteria, iron bacteria, tannins, algae, oil, acid, or other
unusual substances, consider pre-treating the water to remove these contaminants before the water supply enters the
appliance, unless the appliance is represented as being capable of treating these contaminants in its specifications.
The appropriate Hague Water Filter can address these water shortcomings. See
Filter Specifications
for details on
each filter.
Iron —
A common problem found in many water supplies is iron. It is important to know what type of and how much
iron is in the water supply.
Iron Type
Function
Ferrous Iron*
(sometimes called clear water
or dissolved iron)
Only type of iron that can be treated with a water softener
Ferric Iron
Insoluble and the particles can eventually foul a resin bed. It should be filtered out before the
water reaches the softener
Organic Iron or Bacterial Iron
Attached to other organic compounds in the water. Additional treatment is needed to remove this
type of iron
Colloidal Iron
Not dissolved, yet stays in suspension. A softener cannot remove this type of iron
* If the water supply contains ferrous iron, a commercially available resin bed cleaner should be used every six months. Follow the instructions on
the container.
Water Characteristics —
The conditioner requires a pH of 7 or above to function properly. An iron test to determine
iron levels is also necessary. An Acid Neutralizing Filter may be necessary if pH levels are below 7.
Water Pressure —
Not less than 20 psi or greater than 80 psi (1.4–5.5 bar) constant. If water pressure exceeds 70
psi (4.8 bar), a pressure regulator is recommended.
Water Supply Flow Rate —
A minimum of 3 gallons (11 liters) per minute or equal to the backwash flow rate of the
particular model is recommended. For the purposes of plumbing sizing, only the rated service flow rate and corre
-
sponding pressure loss may be used. Prolonged operation of a water conditioner at flow rates exceeding the tested
service flow rate may compromise performance.
Water Temperature —
Not less than 40° or greater than 120°F (4°–49°C).
Drain —
Drain the appliance to an appropriate drain, such as a floor drain or washer drain that will comply with all
local and state plumbing codes. To prevent back-siphoning, provide an adequate air gap or a siphon break. See
Installation Steps and Start-Up Procedures
.
Electricity —
The transformer supplied is for a standard 115 volt, 60-cycle AC outlet for locations in North America or
220 volt, 50-cycle AC outlet for locations outside North America.
Precautions
Do
1.
Comply with all state and local, building, plumbing, and electrical codes.
2.
Install the appliance before the water heater.
3.
Install the appliance after the pressure tank on well-water installations.
4.
Install a pressure-reducing valve if the inlet pressure exceeds 70 psi (4.8 bar).
5.
Examine the inlet line to ensure water will flow through it freely and that the inlet pipe size is sized correctly. For well
water with iron, the recommended minimum inlet pipe size 3/4-inch I.D. and for municipal water the recommended
minimum inlet pipe size is 1/2-inch I.D.
6.
Install a gravity drain on the cabinet elbows. See Step 5 of
Installation Steps and Start-Up Procedures
.
7.
Secure the drain line on the appliance and at the drain outlet. See Step 6 of
Installation
Steps and Start-Up
Procedures
.
8.
Allow a minimum of 8 to 10 feet (2.4 to 3.0 m) of 3/4-inch pipe from the outlet of the appliance to the inlet of the water
heater.
Do Not
1.
Do not install if checklist items are not satisfactory.
See Checklist Before Installation
.
2.
Do not install if the incoming or outlet piping water temperature exceeds 120°F (49°C). See
Water Conditioner Speci-
fications
.
3.
Do not allow soldering torch heat to be transferred to valve components or plastic parts when using the optional cop-
per adapters.
4.
Do not over-tighten the plastic fittings.
5.
Do not plumb the appliance against a wall that would prohibit access to plumbing. See
Installation Steps and
Start-Up Procedures
.
6.
Do not install the appliance backward. Follow the arrows on the inlet and outlet.
7.
Do not plug the transformer into an outlet that is activated by an On/Off switch.
8.
Do not connect the drain and the overflow (gravity drain) lines together.
9.
Do not use to treat water that is microbiologically unsafe or of unknown quality without adequate disinfection before or
after the appliance.
10.
Do not allow your appliance or drain line to freeze.