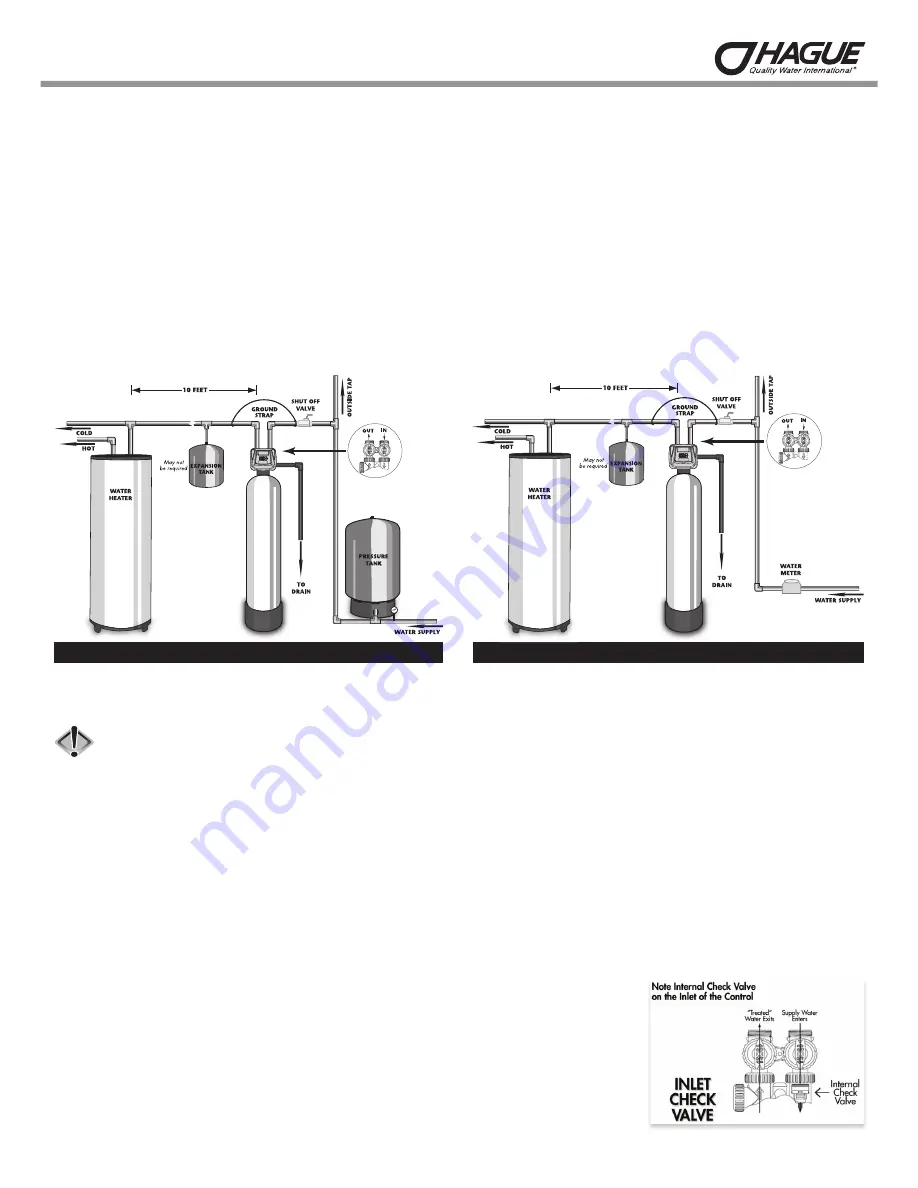
5
Hague Filter Owner's Manual
GENERAL INSTALLATION & SERVICE WARNINGS
The control valve, fittings and/or bypass are designed to accommodate minor plumbing misalignments . There is a small amount of “give” to properly
connect the piping, but the water treatment unit is not designed to support the weight of the plumbing .
Do not use Vaseline, oils, other hydrocarbon lubricants, or spray silicone anywhere . A silicone lubricant may be used on black “O” Rings, but is not
necessary .
Avoid any type of lubricants, including silicone, on red or clear lip seals.
Do not use pipe dope or other sealants on threads.
Teflon® tape must be used on the threads of the 1” NPT inlet and outlet, the brine line
connection at the control valve, and on the threads for the drain line connection . Teflon® tape is not used on the nut connections or caps because
“O” Ring seals are used . The nuts and caps are designed to be unscrewed or tightened by hand or with the special plastic Service Wrench,
#CV3193-02 . If necessary, pliers can be used to unscrew the nut or cap . Do not use a pipe wrench to tighten nuts or caps .
Do not place screwdriver
in slots on caps and/or tap with a hammer.
SITE REQUIREMENTS
• Water pressure – 25-100 psi
• Current draw is 0 .5 amperes
• Water temperature – 33-100°F (0 .5-37 .7°C)
• The plug-in transformer is for dry locations only
• Electrical – 115/120V, 60Hz uninterrupted outlet
• The tank should be on a firm level surface
1 . The distance between the drain and the water conditioner should be as short as possible (see #7) .
2 . It is NOT recommended to install any water treatment unit with less than 10 feet of piping between its outlet and the inlet of a water heater .
CAUTION: To protect the unit in the event of a hot water heater backup, the manufacturer recommends the use of an expansion tank
on the outlet side of the unit (see diagram).
3 . Do not locate unit where it or its connections (including the drain and overflow lines) will ever be subjected to room temperatures under 33°F .
4 . Do not subject the tank to any vacuum as this may cause an “implosion” and could result in leaking . If there is a possibility a vacuum could
occur, please make provision for a vacuum breaker in the installation .
5 .
INLET/OUTLET PLUMBING:
Be sure to install Bypass Valve onto main control valve before beginning plumbing . Make provisions
to bypass outside hydrant and cold hard water lines at this time . Install an inlet shutoff valve and plumb to the unit’s bypass valve inlet
located at the right rear as you face the unit . There are a variety of installation fittings available . They are listed under the Installation
Fitting Assemblies section of the manual . When assembling the installation fitting package (inlet and outlet), connect the fitting to the
plumbing system first and then attach the nut, split ring and “O” Ring . Heat from soldering or solvent cements may damage the nut, split
ring or “O” Ring . Solder joints should be cool and solvent cements should be set before installing the nut, split ring and “O” Ring . Avoid getting
solder flux, primer, and solvent cement on any part of the “O” Rings, split rings, bypass valve or control valve . If the building’s electrical system
is grounded to the plumbing, install a copper grounding strap from the inlet to the outlet pipe . Plumbing must be done in accordance with all
applicable local codes .
When installing an air regenerating filter the customer may experience, under certain conditions, small
amounts of air (cloudy water) at the taps . This is normal . On rare occasions, this may result in “shots of
air” at a particular fixture . By installing a loop or “U” on the outlet side of the unit, this will act as an air
trap and improve this situation .
An internal check valve is located inside the inlet on air filtration units
(see diagram at right)
. This check
valve holds the air in the system, preventing its escape from the tank . Plumbing codes may require the
installation of a thermal expansion tank on the outlet side of the system to prevent a water heater backup
condition .
WELL WATER INSTALLATION
MUNICIPAL INSTALLATION
Installati on