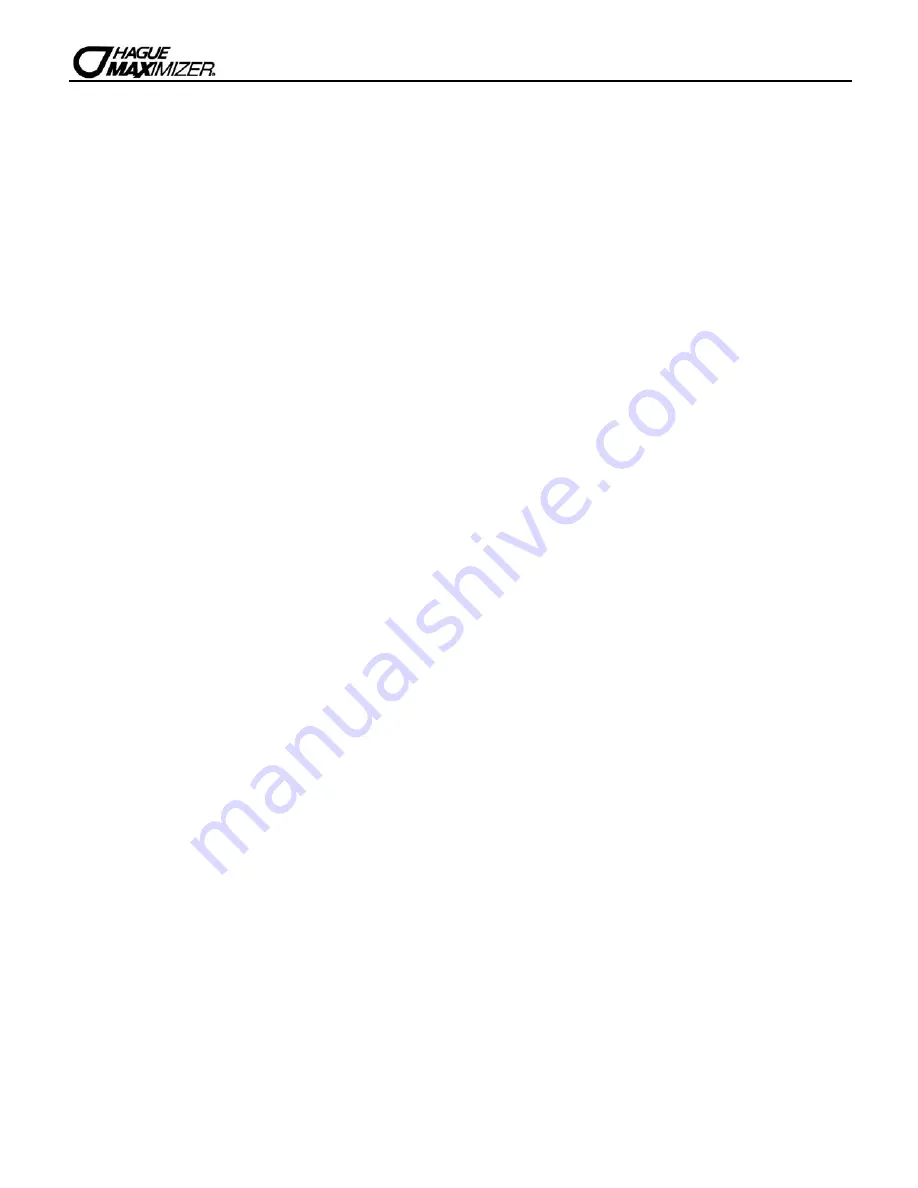
PART NO. QTY
ITEM
DESCRIPTION
93583
1 Drive End Cap
Seals the two openings on the Main Valve Body. The larger diameter opening is
sealed with an O-ring used as an axial or "face" seal. The O-ring sits in a groove in
the Drive End Cap. This groove must be free of defects such as pits or scratches
and also free of debris. The smaller diameter seal is accomplished with an O-ring
used as a radial seal. The O-ring should be placed on the male boss on the Drive
End Cap. When assembling the Drive End Cap to the Main Valve Body, care should
be taken to make sure the small O-ring is aligned with the opening in the Main
Valve Body and that the large O-ring stays in the groove in the Drive End Cap. If
misaligned, the O-rings can become pinched and leak.
90217
1 Drive Motor
The Drive Motor is held in place by two 1/2" screws. The screws should be "snug."
The brass pinion gear on the Drive Motor should engage the plastic Drive Gear.
The wires should be securely fastened to the Control.
93216
1 Piston Slide
The Piston Slide should move freely inside the Drive End Cap Housing. The
stainless steel threaded stud should be pointing toward the Main Valve Body.
93217
1 Piston Slide Cam
This is the “heart” of the drive system. There is a threaded stainless steel shaft that
runs through the main drive axle. The Drive Gear is attached at the short end and
the Magnet Disc at the other end. The Piston Slide Cam is assembled inside of the
Piston Slide (93216). This Cam Shaft should turn freely before the Drive Motor is
assembled.
93219
1 Piston Slide Cam
The cover secures the Piston Slide Cam (Part No. 93217) in place and acts as a
Cover
bushing for the Cam Shaft.
95521
1 Magnet Disc
The Magnetic Disc is assembled to the Piston Slide Cam by means of a "keyed"
Assembly
opening to ensure proper orientation.
90802
2 Screw
93601-JG
1 Brine Valve
Attaches to the Drive End Cap with two 3/4" thread cutting screws and has one
Housing
O-ring seal. When assembling, the O-ring should be placed in the Drive End Cap
Assembly
groove and be lubricated with silicone grease. (See Fig. 8 for more details.)
90828
1 O-ring
93238
1 Drive Gear
The Drive Gear is assembled to the Piston Slide Cam by means of a "keyed"
opening which transfers the "torque" generated by the Drive Motor to the rest of
the drive system. If the drive system becomes jammed, this opening can become
"rounded" causing the gear to turn, but not the Piston Slide Cam. If this occurs,
clear the jam and replace the Drive Gear and Piston Slide Cam (Part No. 93217).
90818
2 Screw
90809
2 Screw-cam cover
93808
1 End Cap O-ring
93522-A
1 Piston Assembly
The Piston should be screwed onto the Piston Slide Cam until it "bottoms out," but
care should be taken not to overtighten. The white Teflon Hydro-slide O-ring covers
should be free of defects such as indentations and cuts. The Drain Gasket should
slide - there will be some friction - without binding on the Piston shaft. When
assembling, care should be taken to insert the Piston into the Main Valve Body
without excessive side-to-side or up/down motion.
90821
1 Brine Valve
Housing O-ring
93891
2 1/4” Nyloc Hex
Nut
93839
1 Drain Gasket
Series 96 Owner’s Manual
26