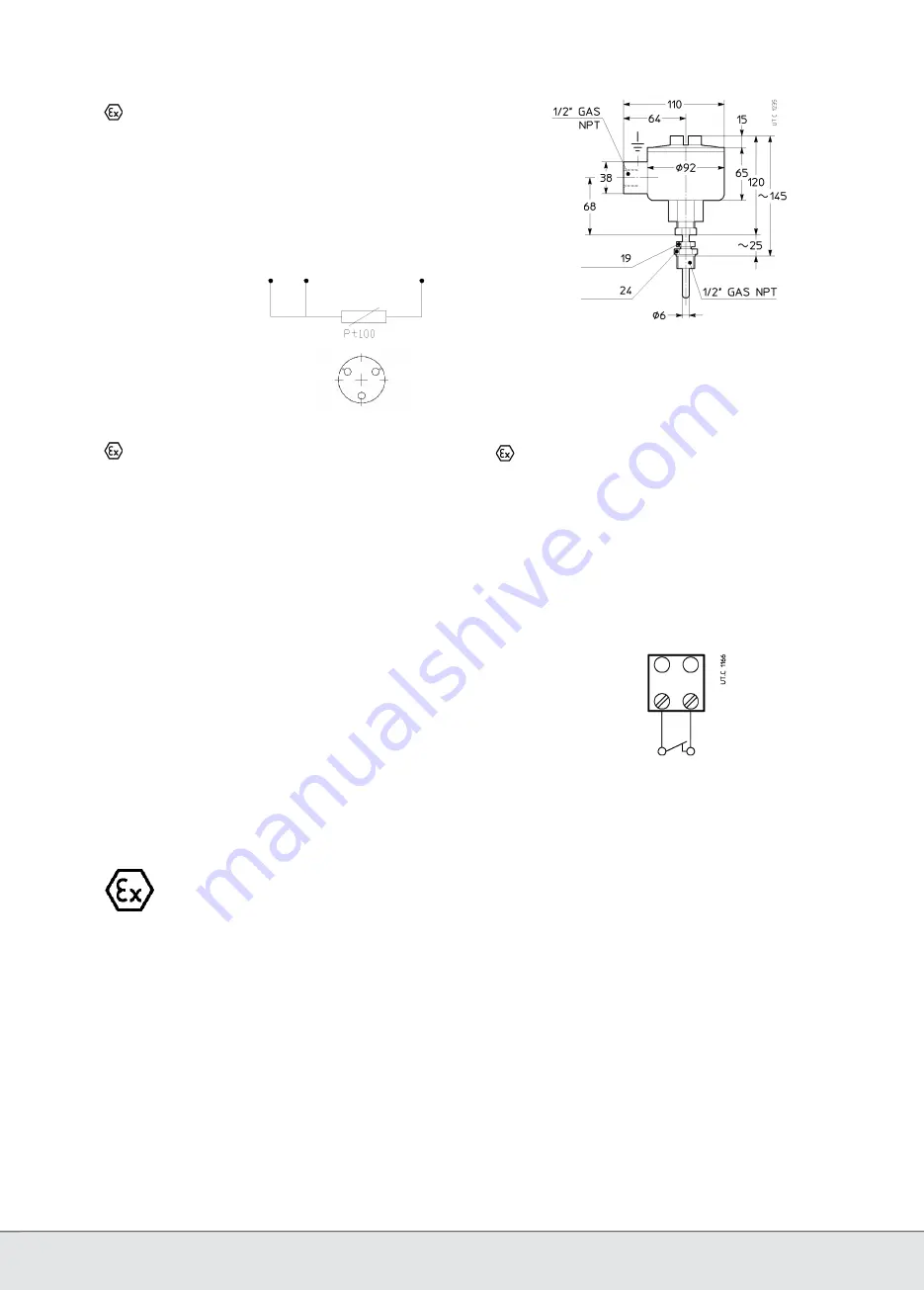
37
ROSSI
GEARMOTORS
UT.D 123 rev. 3
16.5 Overall dimensions
17 - “ON-OFF” oil level switch
II 1/2 G EEx d IIC T6
17.1 Specifications
It is a level control device with reed contacts in a supporting stem
moved by the magnetic field activated by the magnets included in
the float.
The float and the supporting stem are included in a hollow column of
not magnetic material connected to the gear reducer casing through
communicating vessels.
Connecting features:
- 2 wires (see Fig. 1)
- Max voltage: 350 V
- Max current: 1,5 A
- 1 cable input 1/2” UNI6125 – IP65
- G 1” brass joint.
17.2 Calibration
The switch is supplied ready for use; when level goes down approx
5 mm, the switch goes on and contact opens. When filling oil in the
gear reducer it is necessary
to verify that device is properly cali-
brated.
If any problems occur during this operation contact ROSSI
MOTORIDUTTORI.
17.3 Installation and maintenance
The accessories used for cable input and for covering unused holes
must be certified according to EN 50014 and EN 50018 standards.
The level switch must be installed and maintained according to plant
and maintenance standards for environments classified to explosion
proof for the presence of gas (i.e.: EN 60079-14, EN 60079-17 or
other national standards). The level switch box must be earth con-
nected. Only proper tools have to be used for installing and disas-
sembling the level switches. Never use electrical connections for
manual installation.
The level switch cables must be installed in mechanical protections
such as conduit pipes with separating joints at the top and the end
of the pipes.
It is recommended to use cables of 0,22 mm
2
section.
All active/passive safety barriers and connected devices (insulated
amplifiers, relays) if any must be certified according to EN 50020
standards with [EEX ia] IIC protection and have to be installed in
a safe area. The contacts are “REED” type and can carry up to ca.
100 000 000 operations during their life cycle. The switch power is
relatively low (30-100 VA/W depending on application). For the safe
use of the contacts it is recommended to drive inductive/capacitive
power-loads through auxiliary relays or to use transient dampers/
suppressors.
spanner
spanner
Fig. 1 Terminal box connections
16 - (Oil or bearing) temperature probe
16.1 Specifications of «EEx d» explosion-proof probe
II 2 GD EEx d IIC TX IP65
It is a thermistor Pt 100 featuring:
- platinum wire with 100
Ω
at 0° C
- precision class B
- max current 40 mA
- max power at temperature probe 0,5 W
- max power at connection head, supply signal 1 W
- connection with 3 wires according to IEC 751 (see Fig. 1)
- gaiter AISI 316 diameter 6 mm
- alluminium case supplied without cable gland
- coupling with sliding probe and 1/2” NPT-M thread
16.2 Specifications of «EEx ia» fail-safe probe
II 2 GD EEx ia IIC TX IP6x
It is a thermistor Pt 100 featuring:
- platinum wire with 100
Ω
at 0° C
- 3 wire connection according to IEC 751 (see fig.1)
- gaiter AISI 316 diameter 6 mm
- alluminium case supplied without cable gland
- coupling with sliding probe and 1/2” NPT-M thread
For the electric specifications and connection wires refer to the specific
instructions relevant to the probe and to the internal transmitter, if any,
at 4 ... 20 mA.
16.3 Installation and maintenance
Fit the coupling with sliding probe into the appropriate threaded hole of
the gear reducer (for the position refer to the attached drawing SPT ...)
by using a spanner key 24, loosen the hexagon using a 19 mm spanner
and slide the probe of the thermometer in (up to the point of contact
when the head of the probe to be checked is closer to gear reducer.
The electrical connections must be made with copper shielded “twisted”
wires separated from power cables. Earth connections must be made
according to current regulations, connecting the internal and external
earth connections.
The body of the probe must be protected against all risks of damage.
Connect the probe to a
temperature control device
with 2 operating
threshold or similar device.
Periodically verify that:
– there is no erosion/corrosion of the gaiter
– the whole equipment is working efficiently by inserting into the circuit
a resistance of a known value and simulating a known temperature.
Attention! Assemble and disassemble the probe with gear reducer
without oil
.
16.4 Calibration
Two operating thresholds are foreseen:
-
Alert
: anomalous increase of temperature, consult table
19 and identify the possible overheating causes. If no
intervention is possible, please start with the machine stop
procedure.
-
Stop
: achieving the maximum temperature allowed, start immediately
with the machine stop procedure, exclude the gearmotor from the
power supply. Consult table 19 and check according to table 15.
If not differently stated in the additional documentation attached to pre-
sent manual, please procede as follows:
- Calibration of oil temperature probe
At commissioning end (see ch. 7) when gear reducer or gearmotor achi-
ves steady thermal conditions, measure oil temperature T
oil
and ambient
temperature T
amb
and calibrate the
operating temperature
(alert) of the
device connected with the oil probe at the lowest temperature between
the following two:
Calculated temperature [°C] = T
oil
[°C] – T
amb
[°C] + 45 [°C]
T
alert
= 85 [°C]
The temperature of
machine stop
may not exceed
T
stop
= 100 [°C]
.
- Calibration of bearing temperature probe
Calibrate the operating temperatures (alarm and stop) of the device
connected to the bearing probe as follows:
T
alert
= 100 [°C]
T
stop
= 110 [°C]
Fig. 1 Diagram
Fig. 2 Diagram
Red
Red
White
Red
Red
White