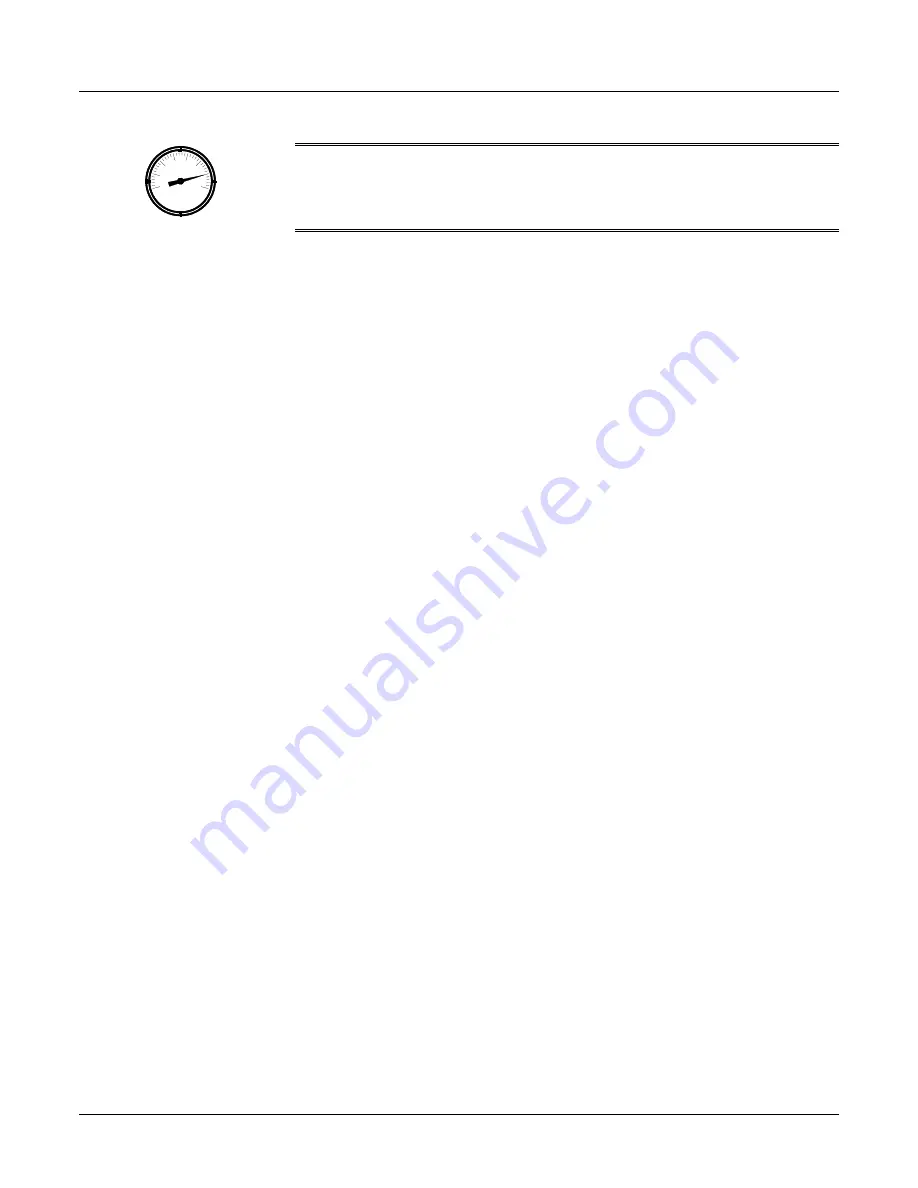
Operating Manual
Maintenance
12/19/02
43
P
UMP
B
ASES
WARNING:
B
OTH PUMP BASES OPERATE UNDER HIGH PRESSURE
. T
O AVOID SERIOUS
BODILY INJURY
,
USE EXTREME CAUTION TO ENSURE ALL PRESSURE FROM BOTH THE SUPPLY
AND DELIVERY SIDE OF THE PUMP BASE HAVE BEEN BLED TO ZERO BEFORE SERVICING THE
PUMP BASE ASSEMBLY
.
Disassemble and clean both Pump Bases annually as follows:
(Refer to the Pump Base Assembly section of the Parts I.D. for reference.)
1. De-pressurize the system.
2. Using the supply ball seat removal tool, (5/8 hex stock) unthread and remove the
supply ball seat. Using the discharge ball seat removal tool (P/N 17928A), unthread
and remove the discharge ball seat.
a) Clean the gasket seating surfaces on the underside of the seats and inside the
pump base cavities.
b) Inspect the seat gaskets and replace as required.
c) Inspect the ball seats for nicks or scratches. Replace as required.
d) Thoroughly clean the threads on the seats before replacement. Coat the threads
thoroughly with lubricant.
e) Install each seat and gasket by threading the seat into the base by hand until the
gasket bottoms inside the pump base. Use a 6” adjustable wrench to snug the
seats approximately ¼ turn.
f) DO NOT OVERTIGHTEN. It may be necessary to periodically retighten each
seat throughout the life of the gasket.
3. Wipe the valve balls clean and inspect for nicks. Replace as required and complete
the Pump Base Assembly.
Inlet Strainer Screen
A strainer screen in each proportioning pump filters out solid matter that could adversely
effect the operation of the ball check valves in the pump base. You will note that the
Daily Start-up procedure indicates these screens should be inspected daily.
For the first week or so of operation, you should clean both pump screens on a daily basis.
The Isocyanate component can crystallize from either moisture contamination or from
freezing. If you follow proper storage, transfer, and operating procedures, and if the
chemicals you receive are clean, you should have little problem with the Isocyanate
screen. In practice though, it is good preventative maintenance to clean the Isocyanate
screen daily. NEVER clean the Isocyanate pump screen during the shutdown operation.
This is because the cleaning of the screen exposes it and its related parts to moisture and
solvent, which can cause the Isocyanate to crystallize. Cleaning the Isocyanate screen
during the start-up procedure will minimize contamination problems because dispensing
will immediately flush out any Isocyanate residue.
Remove and clean the strainer screen as follows:
1. Close the material supply valve at the inlet of the appropriate proportioning pump.
This prevents material being pumped when the strainer screw is removed.