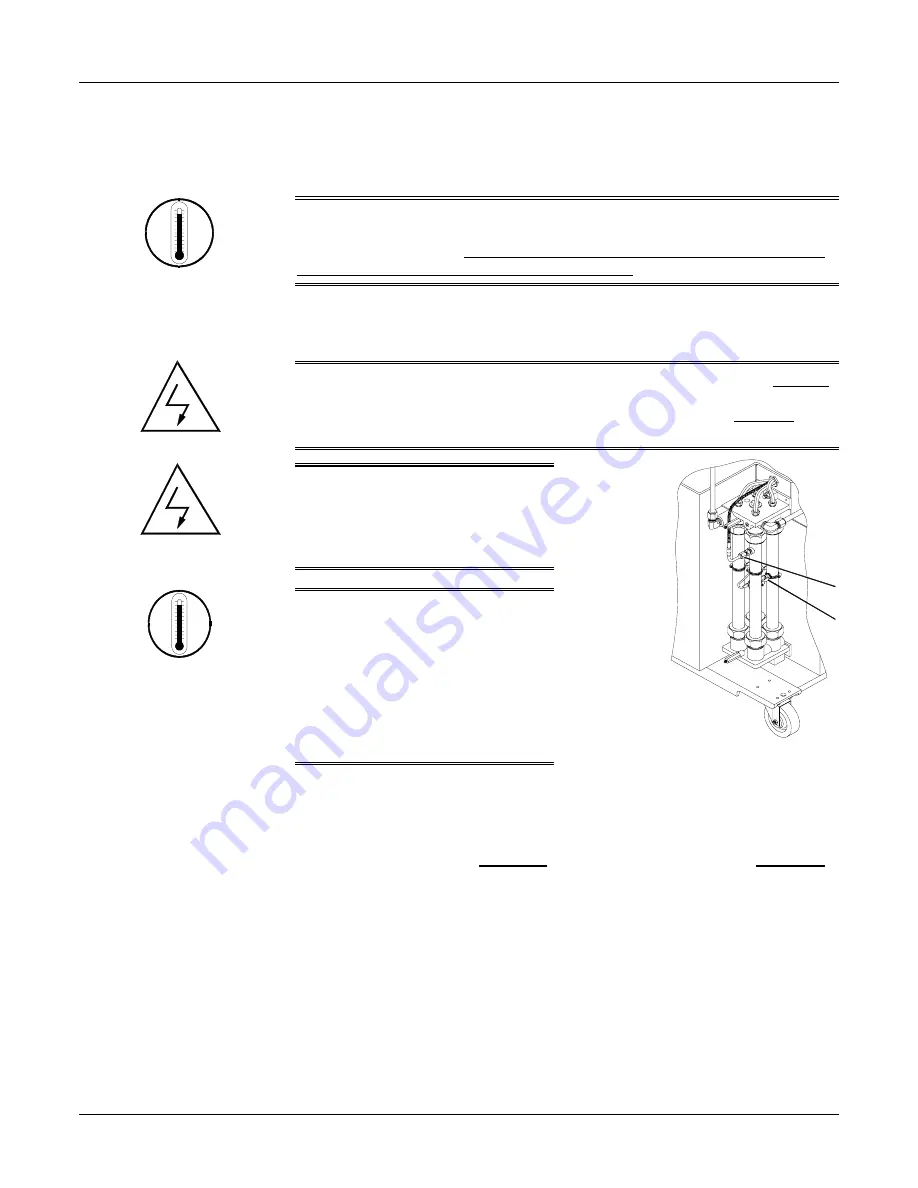
Operating Manual
Troubleshooting
12/19/02
33
c) Maintaining hose temperature now requires manual adjustment of the Hose Heat
Power Set. (See Figure 14) Adjust the control clockwise for initial warm up
and then adjust as required to maintain the hose temperature.
(Do Not exceed 50 Amps.)
WARNING:
T
HE TEMPERATURE MUST BE CLOSELY MONITORED DURING MANUAL CONTROL
OF THE
H
OSE
H
EAT
S
YSTEM AS THE HOSE CAN OVERHEAT AND CAUSE SERIOUS DAMAGE TO
PROPERTY AND PERSONNEL
. H
OSE TEMPERATURE
,
AS INDICATED BY A PROPERLY INSTALLED
H
OSE
T
HERMOMETER
, CANNOT
EXCEED
170
°
F (76
°
C).
Primary Heaters
WARNING:
T
O AVOID SEVERE BODILY INJURY OR DEATH FROM ELECTRIC SHOCK
, DO NOT
PERFORM THESE TROUBLESHOOTING PROCEDURES WITHOUT FIRST SWITCHING OFF THE MAIN
POWER DISCONNECT AND INTERRUPTING SUPPLY VOLTAGE AT THE SOURCE
. DO NOT
ENTER
THE ELECTRIC CONSOLE WITH THE MAIN POWER DISCONNECT ON
.
WARNING:
HIGH VOLTAGE EXISTS INSIDE
THE PRIMARY HEATER COVERS
. D
O NOT
REMOVE EITHER COVER BOX WITHOUT FIRST
SWITCHING OFF THE MAIN POWER
DISCONNECT
.
WARNING:
HIGH TEMPERATURE EXISTS
INSIDE THE PRIMARY HEATER COVERS
.
N
EVER OPERATE THE PROPORTIONING UNIT
WITH EITHER HEATER COVER BOX REMOVED
.
C
OOL THE FLUID IN THE HEATER BY
PUMPING UNHEATED FLUID THROUGH THE
HEATER WITH THE HEATER OFF TO AVOID
BODILY INJURY FROM HOT FLUID AND HOT
METAL
.
Figure 17. Primary Heater
Try the recommended solutions in the order given for each problem to avoid unnecessary
repairs. Also, determine that all circuit breakers, switches, and controls are properly set
and wiring is correct before assuming there is a problem.
Problems Solutions
Primary Heater Circuit Breaker trips.
1
Primary Heater does not heat; red LED light on the Primary Heater
Controller is ON.
2, 4, 3, 6
Primary Heater does not heat; Primary Heater Controller is ON.
4, 5
Primary Heater heats but red LED on the Primary Heater Controller is
ON continuously.
3, 4, 6
Primary Heater partially heats but red LED on the Primary Heater
Controller is ON continuously.
6, 7, 8
When flow starts the red LED on the Primary Heater Controller comes
ON and stays ON for 30 seconds or more.
6