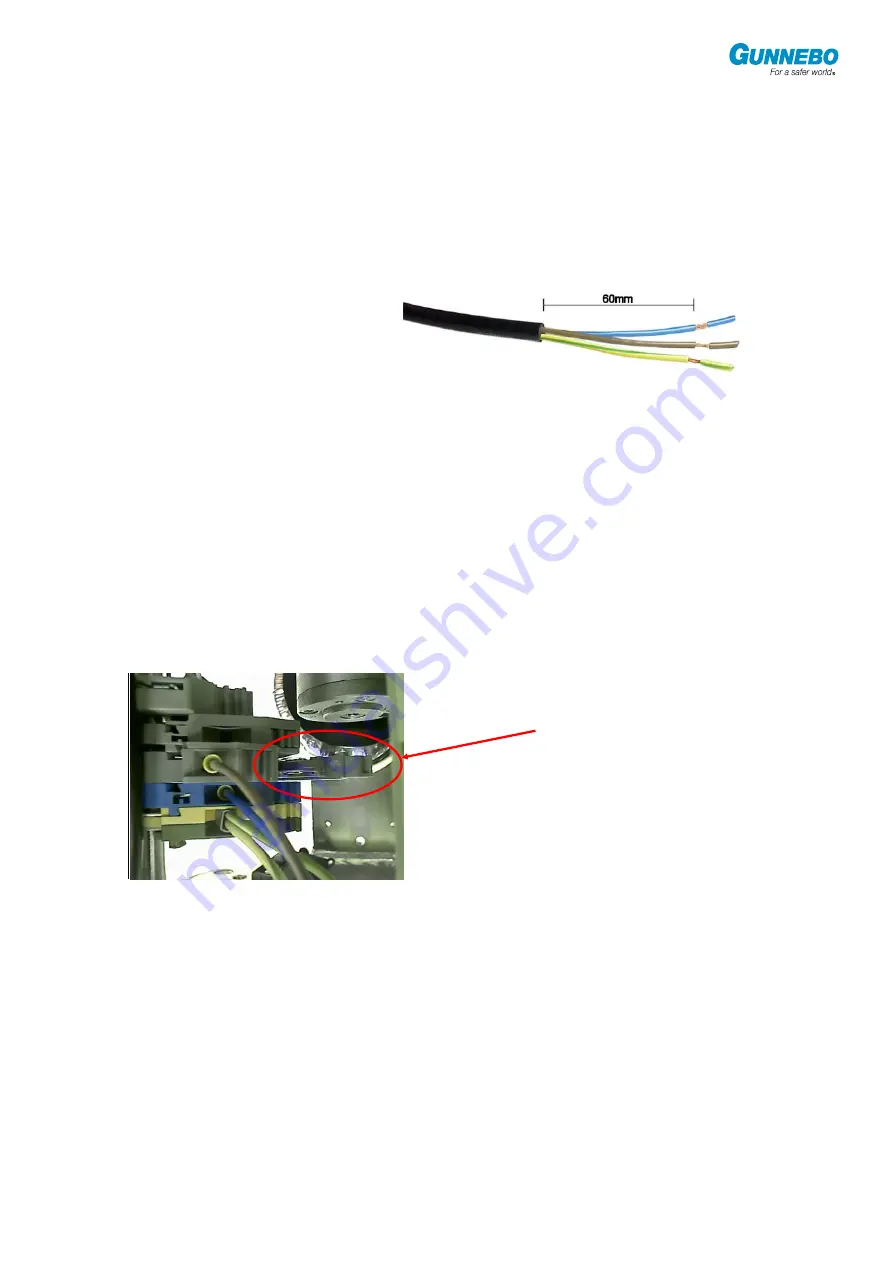
29
.............................
CCEC/ OM Manual GlasStile GSR 1.6 EN
07
.2009
Main power supply
110 to 230 VAC single phase 1.0 A, 250W.
Connection
Check that mains power is off with a certificated and calibrated voltage meter
– when it‟s safe to
do so, connect the Earth first, and then the Neutral and then the Live connection last.
Three-core cable with a conductor area of 1.5mm (min), approved for the specific installation.
1. Strip the sheath to expose 60mm
2. The power cable must be laid so that its sheath is secured in the clamp. See Fig 5.7a.
3. Connect the cores to the terminal block placed on one of the vertical bars, see Fig 5.7.
4. Ensure all connections are secure.
5. Ensure all the cables are contained within the centre column.
Disconnection
Check that mains power is off with a certificated and calibrated voltage meter
– when it‟s safe to
do so, remove the live connection first, then the Neutral and then the Earth.
To switch of the power locally in the unit you can simply unclip the glass fuse breaker as shown
in the image below
Glass Fuse Holder
5 x 20 LBC 2A