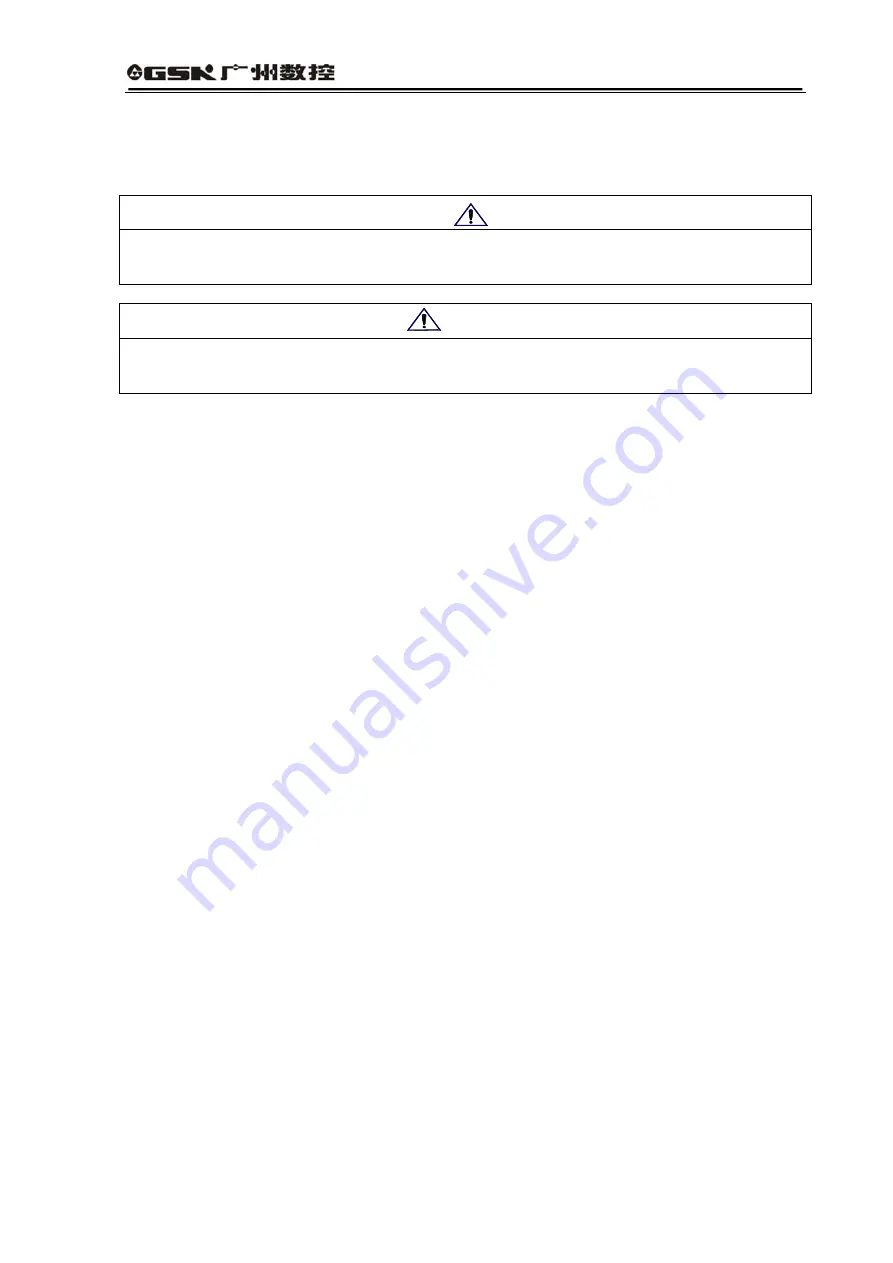
DA98D User Manual
10
Chapter Three Wiring
●
Personnel involved in wiring or examination must possess sufficient abilities in this task.
●
Wiring and examination must be conducted 5 minutes after the power is off for preventing electric
shock.
●
The wires must be connected according to terminal voltage and electrode to prevent the
equipment from being damaged or personnel from being hurt.
●
The drive unit and servo motor must have good ground contact.
3.1 Standard Wiring
External connection of the drive unit is related to the control modes.
1
)
Position Control Mode
Fig. 3.1 shows standard wiring for the position control mode.
2
)
Speed Control Mode:
Fig. 3.2 shows the standard wiring for the speed control mode.
3
)
Wire Distributing
(
1
)
Power Terminal TB
z
Wire cross-sectional area: Terminals of R, S, T, PE, U, V and W have an area
1.5mm
2
(AWG14-16) and more while terminals of r and t have an area 1.0 mm
2
(AWG16-18) and more.
z
Grounding: the grounding wire shall be as thick as possible. The servo driver and
motor has ground contact at the point of PE terminal with a grounding resistance
less than 100
Ω
.
z
Terminal connection adopts SVM2-4 pre-insulation cold pressing terminal. The
connection must be fastened.
z
It is recommended to supply power with three-phase isolating transformer, which
will reduce the possibility of electric shock.
z
It is recommended that the power supply gives power through noise filter for
enhancing anti-jamming ability.
z
Please install non-fuse breaker (NFB) in order to cut off external power supply
when the driver breaks down.
(
2
)
CN2Contrl Signal CN1 and Feedback Signal CN2
z
Wire material selecting: employ shielding cable (best with inter-twisted shielding
cable), the cross-section area of the core shall be 0.12mm
2
(AWG24-26) and more.
The shielding layer shall be connected with FG terminal.
z
Wire and cable length: wire and cable shall be as short as possible; control signal
CN1 shall not be longer than 3 meters while the feedback signal CN2 cable shall not
be longer than 20 meters.
z
Wire laying: Wire shall be laid far away from the power circuit to prevent jamming.
Attention
Warning
Summary of Contents for DA98D
Page 1: ...DA98D Digital AC Servo Drive Unit User Manual V5 00 ...
Page 15: ...DA98D User Manual 4 Fig 1 1 Appearance of Servo Drive unit 2 Servo motor appearance ...
Page 16: ...DA98D User Manual 5 Fig 1 2 Servo Motor Appearance ...
Page 23: ...DA98D User Manual 12 Fig 3 1 Standard Wiring for Position Control Mode AM26LS32 Receiver ...
Page 24: ...DA98D User Manual 13 Fig 3 2 Standard Wiring for Speed Control Mode AM26LS32 Receiver ...
Page 71: ...DA98D User Manual 60 Installation Dimension Drawing for BS 120 Model ...
Page 72: ...DA98D User Manual 61 Installment Dimension Drawing for BS 200 Model ...
Page 73: ...DA98D User Manual 62 Installment Dimension Drawing for BS 300 Model ...
Page 74: ...DA98D User Manual 63 Installment Dimension Drawing for BD 80 Model ...
Page 75: ...DA98D User Manual 64 Installment Dimension Drawing for BD 120 Model ...