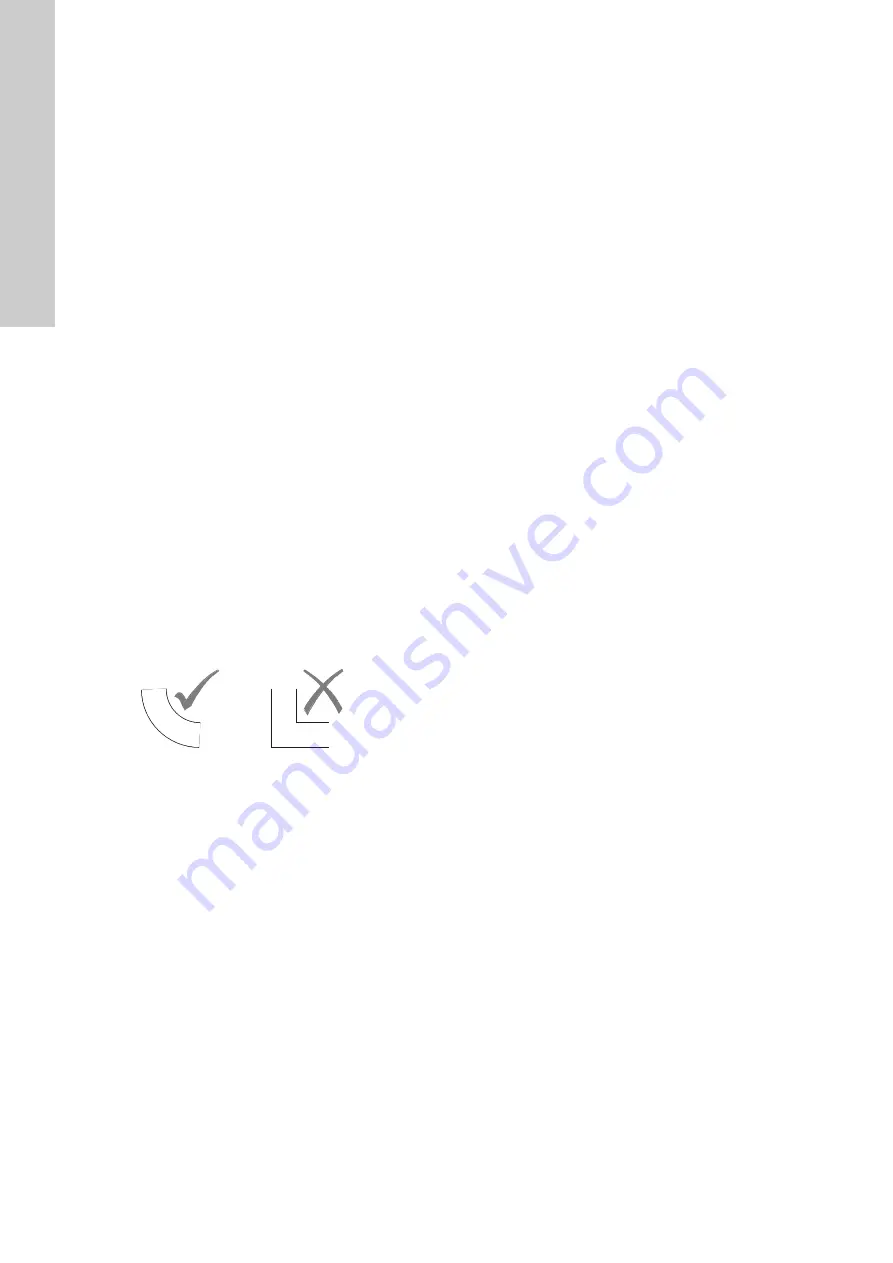
English (GB)
20
6.5.3 Checking the product (NaClO solution)
We recommend to perform this check with the Grundfos
Selcoperm test kit. See section
1. Put on protective clothing, safety goggles and gloves.
2. Put a clean 500 ml vessel under the product sample valve (H).
3. Slowly open the sample valve (H) and fill the vessel with 500
ml NaClO solution to flush the sample line.
4. Dispose of the sample in accordance with local regulations.
5. Take a 50-100 ml sample from sample valve (H).
6. Check the temperature and the concentration of the NaClO
solution according to the test kit operating instructions.
– The reading should not exceed 40 °C.
6.6 Voltage, amperage and air flow readings
The readings for the electrochlorinator can be taken from
display (28). Scroll down in main menu using [UP] and [DOWN]
keys until the present values are displayed. See required values
in section
.
6.7 Ventilation pipework
Ventilation pipework should be installed to the standards detailed
in section
. The air flow through the
electrochlorinator is key to the ATEX rating of the product. Key
components in the ventilation line, such as the Venturi tee and
ventilation hose must be installed correctly to ensure the correct
functioning of the system.
6.7.1 Visual inspection of ventilation pipework
• The pipework should be installed as direct and straight as
possible with no dips and no more than 10 m in length.
The run should rise continuously in an uphill direction towards
the safe discharge point.
• A minimum distance of 0.5 m should be allowed between the
product line and ventilation line at all times.
• The Venturi-tee outlet to the product line should be installed
downwards.
• Only smooth bends should be used for ventilation pipework.
See following figure:
• We suggest that a tee is fitted at the safe ventilation point to
encourage discharge from the ventilation line.
• The flexible vent hose should end outside the
electrochlorination room but not run to the safe ventilation
point. See figs.
.
6.8 Alarms
Before testing, enter service menu 1 (see section
). Set the alarm timer to 10 seconds. This will significantly
reduce the testing time. The alarm timer must be reset after
completion of testing. After the triggering of each alarm the
electrochlorinator will need to be reset at control (28).
6.8.1 Internal tray flood alarm
The internal tray flood switches (17) are situated at the base of
each chamber of the electrochlorinator. To test the alarm, lift the
float switches until the contact is broken. This will trigger the
alarm and stop the electrochlorinator.
6.8.2 Low water flow alarm
Slowly restrict the water flow at water flow adjustment valve (8)
until the floater falls below flowmeter switch (20). This will cause
an alarm at display (28) and stop the electrochlorinator.
6.8.3 Air flow alarm
The air flow alarm utilises an air flow sensor (13) to shut down the
electrochlorinator on low or high air flow.
High air flow alarm
Remove the cover from the electrolysis and degassing chamber.
This will allow the air flow to rise, and will shut down the
electrochlorinator on high air flow.
Low air flow alarm
Refit the cover and manually restrict the air flow at the safe
ventilation point. This will reduce the air flow below the low air
flow alarm point and shut down the electrochlorinator.
6.8.4 Volt alarms
There are many ways of triggering high and low volt alarms.
The fault finding (see section
) details the cause
and effect of these alarms. The best way to check the alarms is to
increase and decrease the water flow.
High volt alarm
Increase the water flow with water flow adjustment valve (8).
This will reduce the SG of the electrolyte. An alarm will be
displayed and the electrochlorinator will be stopped.
Low volt alarm
1. Mark the position of the flowmeter switch (20) so it can be
reset after the test.
2. To prevent a low water flow alarm, move the flowmeter
switch (20) downwards.
3. Decrease the water flow at water flow adjustment valve (8).
This will increase the SG of the electrolyte. An alarm will be
displayed and the electrochlorinator will be stopped.
4. Move flowmeter switch (20) to its original position.
6.8.5 High and low tank alarms
These alarms must be triggered by filling the product tank (M) to
its high alarm point and then emptying it to its low alarm point
while the system is inhibited. Or by disconnecting the level
sensor (25) and supplying a 0-10 V signal* (to contact X4:2) to
simulate the pressure sensor output.
* Only for product tanks from spring 2009 and newer
TM
04
84
50
46
11