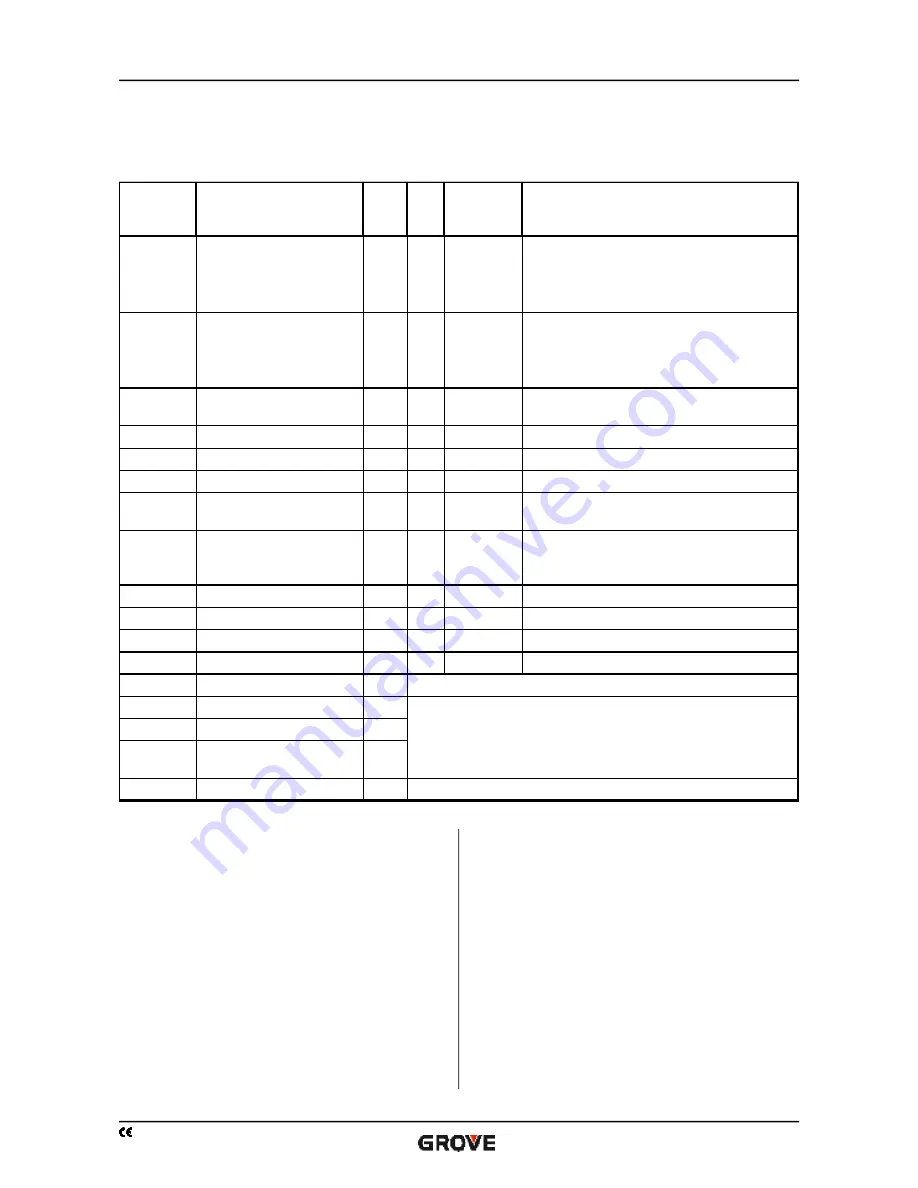
57
Models
Revision 02-2000
Toucan 1010
Description and parameters values for
Toucan 1010
models.
Calibrator use as measuring instrument :
BATT V :
The measure of battery voltage can be done at any time,
even when the work platform is in operation, thus
enabling analysis, if necessary, of the battery voltage
fluctuations.
MOTOR V :
The measure of the motor voltage in operation enables
the determination, for a chosen speed, of the voltage to
be applied at the motor terminals. The value of this voltage
calculated in percentage of the battery voltage determines
the speed setting.
MOTOR AMP. :
The measure of the current at the motor enables the
determination of the current limit value to which the
controller must be set when the machine is driven on a
ramp.
TEMP °C :
The measure of the temperature enables the analysis of
the controller temperature increases, therefore the
operating conditions of the work platform.
Parameter
Description
Unit Step
Values
Toucan
1010
Comments
Speed 1
Speed n°1 (variable)
%
1%
45
First gear drive speed.
Mast and jib lowering function speed
Swing movement speed from platform
controls.
Speed 2
Speed n°2 (variable)
%
1%
50
Jib raising function speed from platform
controls.
Mast raising function speed from ground
controls.
Speed 3
Speed n°3 (variable)
%
1%
80
Mast raising function speed from platform
controls.
Speed 4
Speed n°4 (variable)
%
1%
100
Drive speed in 2
nd
and 3
rd
gear.
Speed 5
Speed n°5 (variable)
%
1%
0
Not used.
Speed 6
Speed n°6 (variable)
%
1%
0
Not used.
Speed 7
Speed n°7 (fixed)
%
1%
45
Speed of movements from the emergency
control panel (Ground controls).
Speed 8 Speed n°8 (fixed)
%
1%
30
Pump speed for make-up flow to hydraulic
wheel motors.
Creep%VB
Starting threshold
%
1%
10
Ramp sec
Ramp shape
sec.
0,1
1
1 second max.
Extra %
Additional speed
%
1%
0
Not used.
Imax Amp.
Current limit
Amp. 10
400
Batt V
Battery voltage
Volt
Motor V
Motor voltage
Volt
Motor Amp.
Motor current
Amp.
Temp °C
Temperature of mosfet
radiator
°C
Test
Test Mode
-
Refer to "Calibrator use as operating control instrument"
Refer to "Calibrator use as measuring instrument"
MAINTENANCE
5
5
Summary of Contents for toucan 1010
Page 1: ...SERVICE MANUAL Revision 02 2000 MA 0235 01 English Toucan 1010 I...
Page 2: ......
Page 3: ...3 Models Revision 02 2000 Toucan 1010 MA0235 01 Models Toucan1010 _____ Toucan1010 I _____...
Page 8: ......
Page 18: ......
Page 20: ......
Page 26: ......
Page 38: ......
Page 40: ......
Page 64: ......
Page 68: ......
Page 69: ...69 Models Revision 02 2000 Toucan 1010 LUBRICATION 7 7 1 Lubrication points TABLE OF CONTENTS...
Page 70: ......