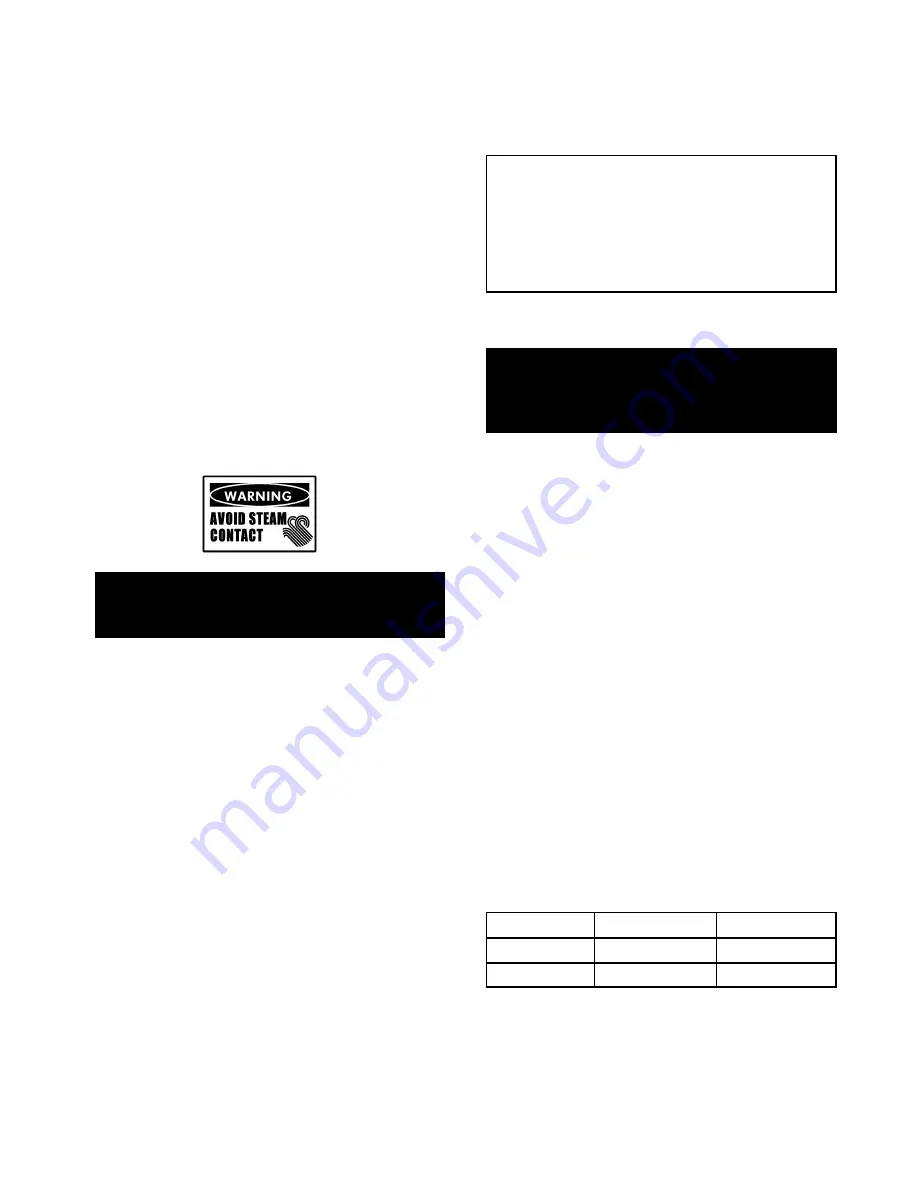
OM/SM-TDH-CE
10
information on the data plate for the type of gas
being used.
3.2
Jacket Vacuum
When the kettle is cold, a positive reading or a
reading near zero on the pressure vacuum gauge
indicates excess air in the jacket. Air in the jacket
slows down kettle heating.
To remove air:
a) Light the unit (Paragraph 2.5.1).
b) When the pressure/vacuum gauge reaches a
positive pressure reading of five PSIG, release
entrapped air and steam by lifting the lever on
the safety valve for about one second. Repeat
this a few times. Let the valve snap back into the
closed position.
WARNING
AVOID ANY EXPOSURE TO THE STEAM
BLOWING OUT OF THE SAFETY VALVE.
3.3 Jacket Filling
The jacket has been charged at the factory with the
proper amount of treated, distilled water. You may
need to restore jacket water to its proper level, either
because water was lost as steam during venting or
by draining.
To add water:
a) If you are replacing water lost as steam use
distilled water. If you are replacing treated water
that ran out of the jacket, prepare more treated
water (Paragraph 3.4).
b) Let the kettle cool completely. Turn the safety
valve elbow anti-clockwise (to avoid thread
damage) until it faces upward.
c)
Open the globe valve and pour distilled or
treated water into the elbow inlet.
d) Hold the safety valve open while you pour to let
air escape from the jacket. Air introduced during
filling must be removed to obtain efficient heating
(Paragraph 3.2).
CAUTION
TDH STEAM JACKETED KETTLES ARE
DESIGNED TO USE TREATED, DISTILLED
WATER ONLY. USE OF ANY OTHER WATER
CAN CAUSE LIME ACCUMULATION ON
INTERNAL SURFACES, AND WILL VOID ALL
WARRANTIES.
3.4
Water Treatment Procedure
WARNING
READ AND FOLLOW ALL PRECAUTIONS
STATED ON THE WATER TREATMENT
COMPOUND LABEL TO AVOID INJURY.
a) Fill the mixing container with the measured
amount of water required (See Table below).
Use distilled water only.
b) Hang a strip of pH test paper on the rim of the
container, with about 1"(25 mm) of the strip
below the water surface.
c)
Measure the water treatment compound (e.g.,
add the compound to the water from a small
measuring cup).
d) Stir the water continuously while you slowly add
water treatment compound, until the water
reaches a pH between 10.5 and 11.5. Judge the
pH by frequently comparing the color of the test
strip with the color chart provided in the pH test
kit.
e) Record the exact amounts of water and
treatment compound used. These amounts may
be used again if the same sources of water and
compound are used in the future. However, it is
advisable to check the pH every time water is
prepared. For optimum performance, use
correctly treated distilled water.
Model
Kettle Capacity Jacket Capacity
TDH-20
18.9 Litres
6.6 Litres
TDH-40
37.9 Litres
8.5 Litres