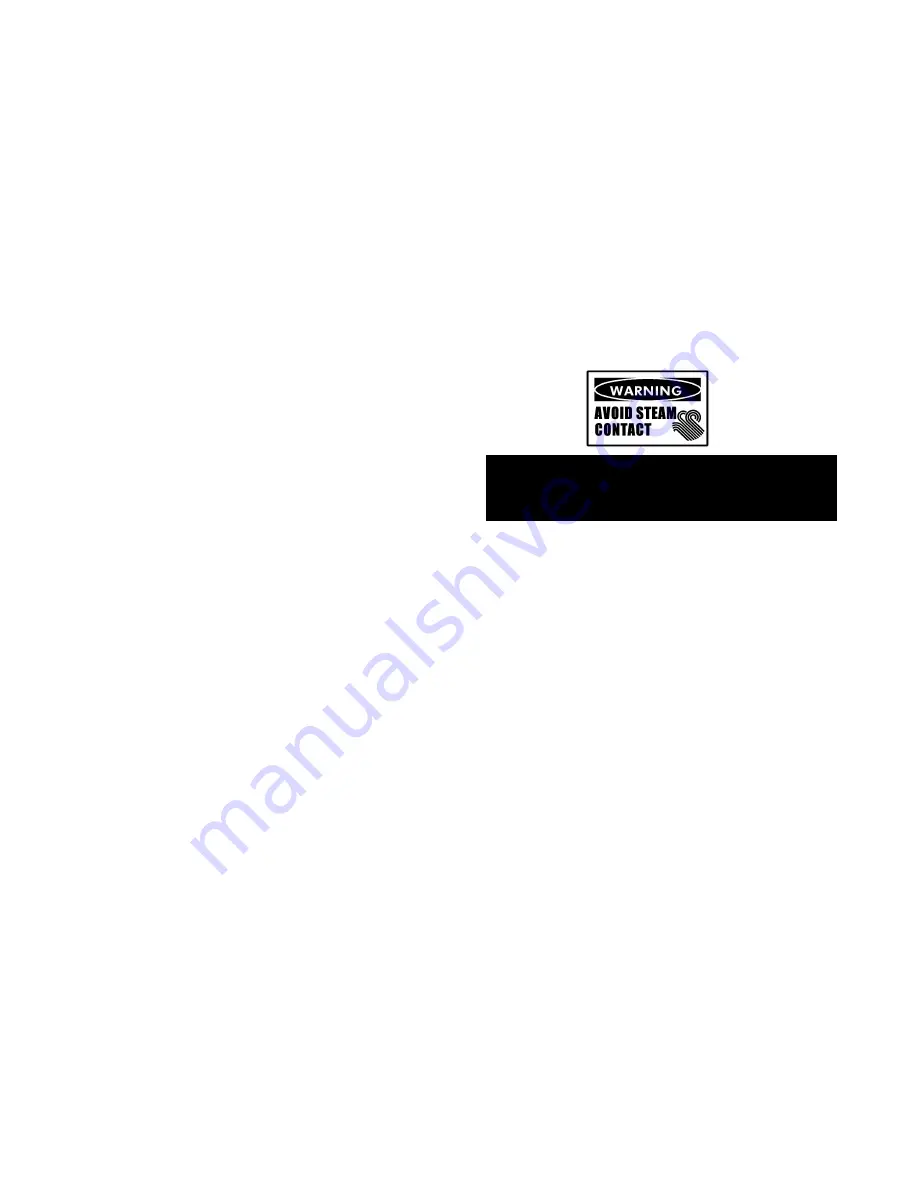
OM/SM-TDH-CE
9
3. Servicing and Conversion
Important
Before attempting any servicing, ensure that the
gas isolating cock is turned off and cannot be
inadvertently turned on. Disconnect the
electricity supply.
After any maintenance task, check the appliance
to ensure that it performs correctly. Carry out
necessary adjustments as detailed in Section 1.
After any servicing or exchange of gas carrying
components:
ALWAYS CHECK FOR GAS SOUNDNESS
NOTE
:
When replacing wiring connections refer to
the wiring diagram contained on the unit and in this
manual.
After Servicing
a) Test for gas soundness as specified in IGE/UP1
as appropriate after any gas connection has
been disturbed.
b) Check for correct operation, as appropriate (see
commissioning of appliance).
Regular Servicing Procedures
The following must be serviced at regular intervals.
Burners
The burner should be cleaned periodically to
maintain maximum performance. Burners are best
cleaned with a wire brush. Any blocked parts are
best cleaned with a metal broach, taking care not to
damage the burner head.
The injector orifice should be cleaned with a wooden
splinter. Metal reamers could distort or increase the
orifice size and should be avoided.
Gears
The gear housing has fittings for lubrication of
moving parts. Because the gears do not run in oil,
periodic lubrication with grease is necessary.
Lubrication frequency depends on operating
conditions, but should be performed at least once
every six months. A #2 grade LGI lithium grease is
recommended. Add grease through the Zerk fittings
on the gear housing until grease flows out of the
bearings around the shaft. Put a liberal amount of
grease on the gear to cover the arc of contact with
the gear.
Safety Valve
At least twice monthly the safety valve requires
checking to ensure that it works correctly. With the
gauge pressure at about five PSIG, lift the valve level
enough to vent steam, then quickly let it snap back
into place.
WARNING
AVOID ANY EXPOSURE TO THE STEAM
BLOWING OUT OF THE SAFETY VALVE.
This procedure should be explained to the user,
since it is to be carried out at least twice a month.
Relevant safety procedures and requirements should
also be explained to the user when carrying out the
procedure.
3.1
Conversion
See Paragraphs 1.8 and 1.9 for important
information about gas conversion. Verify the
type of gas to be used. All conversions must be
for approved gas in countries listed in Paragraph
1.9.
To change from natural gas to propane gas or vice
versa change
Burner Injector
Pressure Setting
Data Plate
Pilot Orifice
The governor spring does not require changing, only
the pressure setting.
IMPORTANT
This appliance was fitted with gas injectors for
type G20 natural gas at the factory. Injectors for
type G25 natural gas are shipped as an
accessory. Prior to installing equipment, or
when converting to another gas, verify that the
injector gas size marking on the injector matches