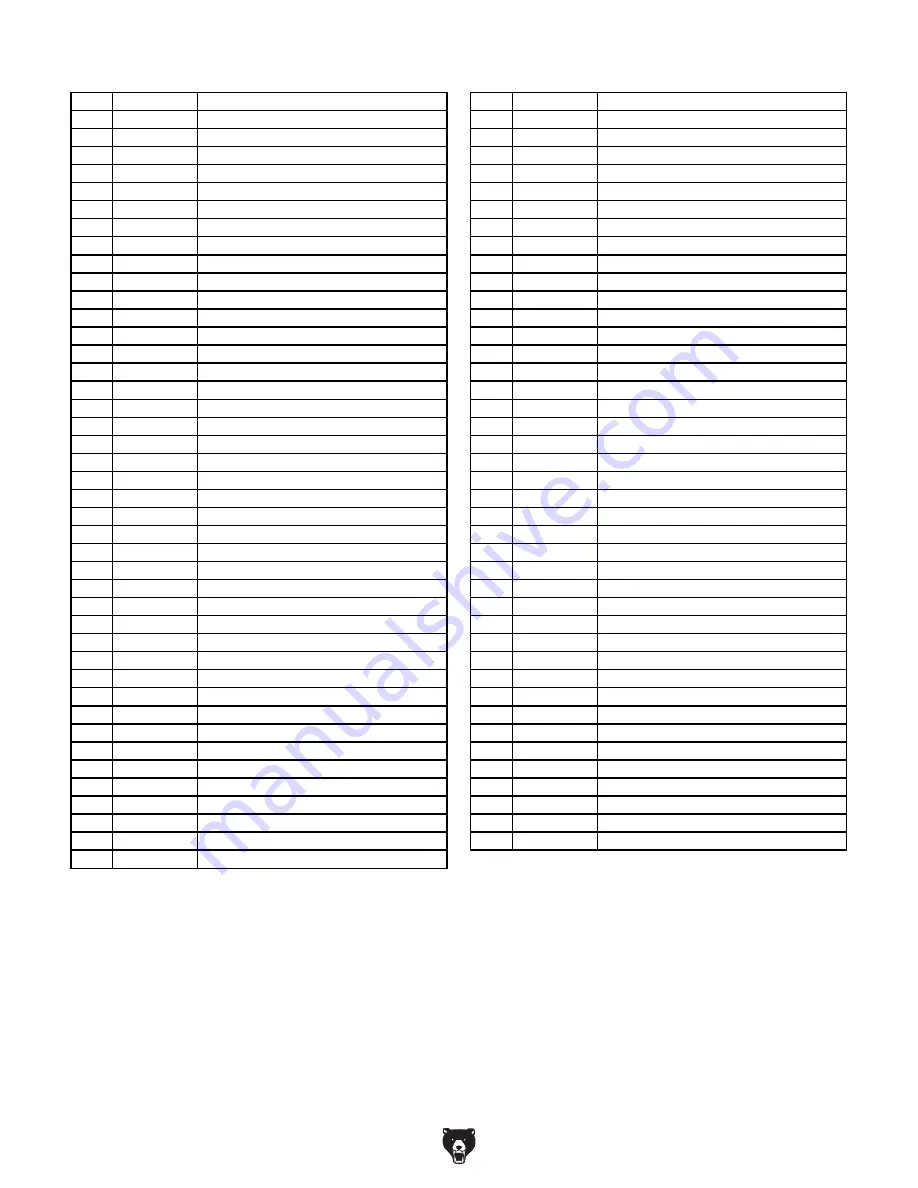
-44-
Model G0832 (Mfd. Since 04/17)
REF PART #
DESCRIPTION
REF PART #
DESCRIPTION
91
P0832091
BUSHING
134
P0832134
CAP SCREW M5-.8 X 20
92
P0832092
CAP SCREW M5-.8 X 10
135
P0832135
STEEL BALL 6MM
93
P0832093
OUTFEED ROLLER (REAR)
136
P0832136
COMPRESSION SPRING 32 X 5 X .7
94
P0832094
INFEED ROLLER (FRONT)
137
P0832137
ROLL PIN 4 X18
95
P0832095
COMPRESSION SPRING 26 X 15.5 X 2.2
138
P0832138
SIDE COVER, RIGHT
96
P0832096
COMPRESSION SPRING 26 X 15.5 X 1.8
139
P0832139
DEPTH STOP KNOB
97
P0832097
PILLOW BEARING BLOCK
140
P0832140
HEX NUT M8-1.25
98
P0832098
GIB
141
P0832141
LOCK WASHER 8MM
99
P0832099
SCREW CAP
142
P0832142
SPACER
100
P0832100
INDICATOR HOUSING
143
P0832143
EXT RETAINING RING 9MM
101
P0832101
PHLP HD SCR M4-.7 X 10
144
P0832144
ROLL PIN 3 X 14
102
P0832102
STEEL BALL 12MM
145
P0832145
THREADED ROD M5-.8 X 16
103
P0832103
INDICATOR HOUSING BRACKET
146
P0832146
LEVER LOCK ROD
104
P0832104
BUSHING
147
P0832147
LOCK ROD HANDLE CAP
105
P0832105
POINTER
148
P0832148
LEADSCREW LOCK PLATE
106
P0832106
FLAT WASHER 4MM
149
P0832149
COMPRESSION SPRING 25.2 X 18 X 1.8
107
P0832107
DEPTH INDICATOR TORSION SPRING
150
P0832150
LOCK PLATE ROD
108
P0832108
BUSHING
151
P0832151
LOCK ROD PIVOT BRACKET
109
P0832109
PHLP HD SCR M4-.7 X 14
152
P0832152
TAP SCREW M4 X 10
110
P0832110
INDICATOR HOUSING COVER
153
P0832153
PHLP HD SCR M5-.8 X 8
111
P0832111
SIDE COVER, LEFT
154
P0832154
FLAT WASHER 5MM
112
P0832112
COLUMN
155
P0832155
EXTENSION TABLE, REAR
113
P0832113
LEADSCREW, RIGHT
156
P0832156
BASE
114
P0832114
LEADSCREW, LEFT
157
P0832157
ELEVATION BLOCK (LEFT)
115
P0832115
GIB
158
P0832158
PHLP HD SCR M5-.8 X 12
116
P0832116
HEX NUT M12-1.75
159
P0832159
SET SCREW M5-.8 X 10
117
P0832117
PHLP HD SCR M5-.8 X 10
160
P0832160
ELEVATION BLOCK (RIGHT)
118
P0832118
SPRING PLATE
161
P0832161
SET SCREW M5-.8 X 20
119
P0832119
HEX NUT M6-1
162
P0832162
DEPTH STOP LABEL
120
P0832120
HEX BOLT M6-1 X 20
163
P0832163
SCALE
121
P0832121
TABLE SUPPORT BRACKET
164
P0832164
DUST SEAL 10 X 8 X 320MM
122
P0832122
CHAIN #35-87
166
P0832166
MAGNET 6 X 4MM
123
P0832123
BEARING RETAINER
167
P0832167
MAGNET HANDLE
124
P0832124
SPACER
168
P0832168
T-HANDLE WRENCH 4MM
125
P0832125
SPROCKET 10T
169
P0832169
FLAT WASHER 5MM
126
P0832126
FLAT WASHER 4 X 16 X 2
170
P0832170
CRANK HANDLE COVER
127
P0832127
CAP SCREW M4-.7 X 12
171
P0832171
LOCK WASHER 5MM
128
P0832128
HEX NUT M10-1.5
172
P0832172
FLAT WASHER 8MM
129
P0832129
TABLE ADJ SCREW M10-1.5 X 25, 36L
173
P0832173
GEAR (LARGE)
130
P0832130
EXT RETAINING RING 8MM
174
P0832174
HEX NUT M5-.8
131
P0832131
DEPTH STOP SHAFT BRACKET
175
P0832175
TORSION SPRING
132
P0832132
DEPTH STOP PIVOT BLOCK
176
P0832176
RUBBER PLUG
133
P0832133
POSITION BLOCK SHAFT
Please Note: We do our best to stock replacement parts whenever possible, but we cannot guarantee that all parts shown here
are available for purchase. Call
(800) 523-4777 or visit our online parts store at www.grizzly.com to check for availability.
Summary of Contents for G0832
Page 52: ......