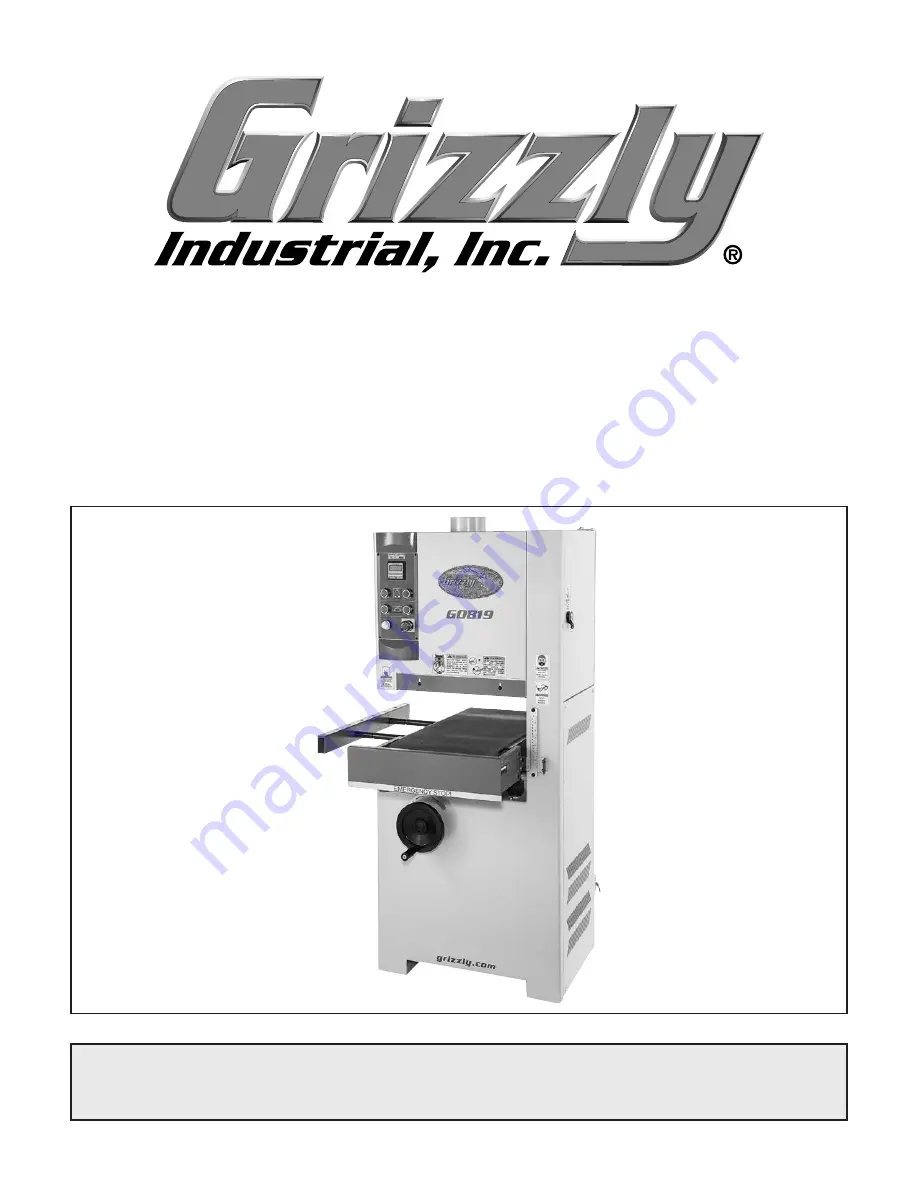
COPYRIGHT © MARCH, 2017 BY GRIZZLY INDUSTRIAL, INC.
WARNING: NO PORTION OF THIS MANUAL MAY BE REPRODUCED IN ANY SHAPE
OR FORM WITHOUT THE WRITTEN APPROVAL OF GRIZZLY INDUSTRIAL, INC.
#BLWK18649 PRINTED IN TAIWAN
V1.03.17
MODEL G0819
15" OPEN-END WIDE BELT SANDER
OWNER'S MANUAL
(For models manufactured since 09/16)
Summary of Contents for G0819
Page 84: ......