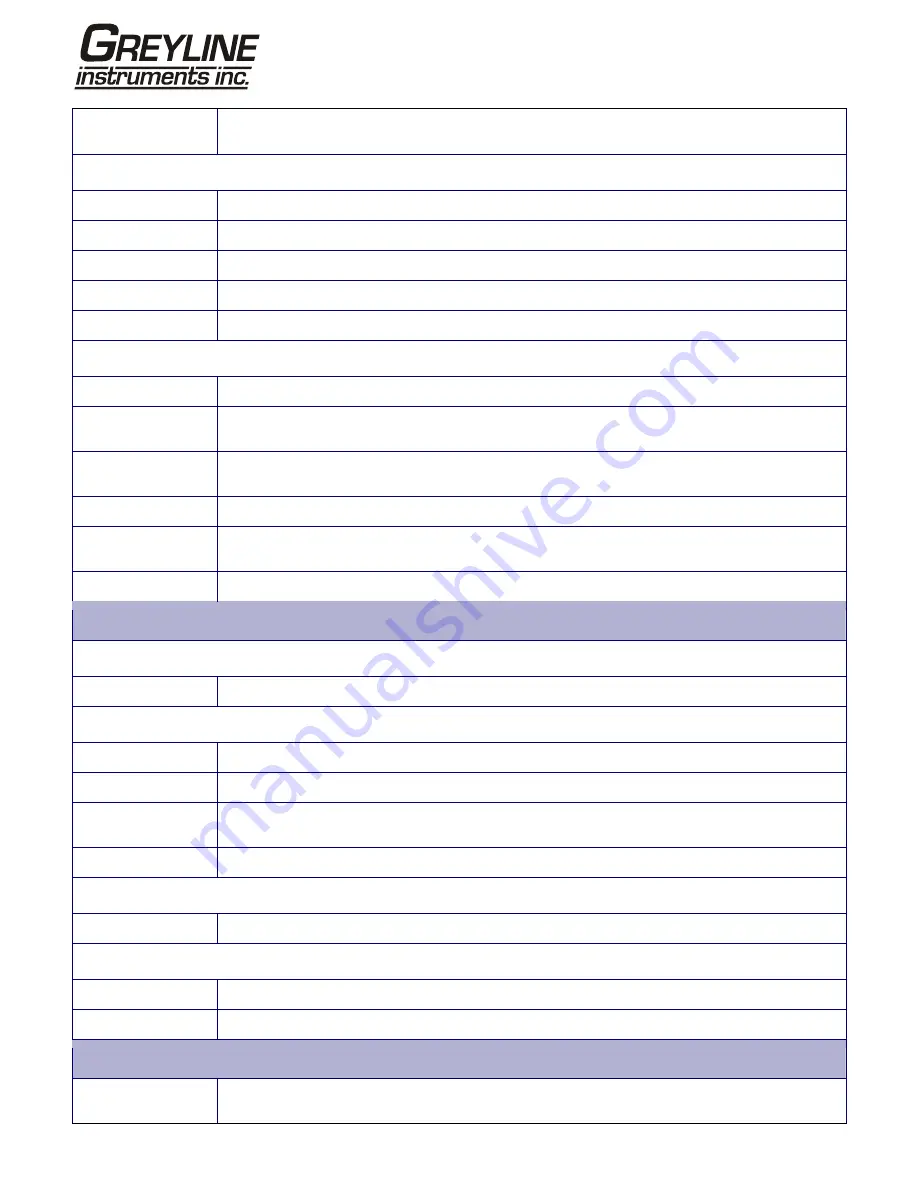
Page
57 www.greyline.com
Power
Consumption:
10.5W.
Battery:
Technology: 5-cell
NiMH.
Capacity: 3.8AHr.
Operating time:
Typically 20 hours continuous with backlight and 4-20mA output OFF.
Recharge Time:
6.5 Hours.
Service Life:
>500 charge/discharge cycles.
Power Supply/Charger:
Manufacturer:
ECOPAC Model ECO-181WP12.
Input Voltage
Range:
90–264Vac.
Input Frequency
Range:
47–63Hz.
Output Voltage:
12Vdc.
Max. Output
Current:
1.5A.
Approvals:
UL, CUL, TUV, CB & CE.
MECHANICAL
Carrying case:
Rating:
All components are contained in a hard-wearing IP67 rated carrying case with a protective moulded foam insert.
Enclosure:
Material:
Flame retardant injection moulded ABS.
Dimensions:
264mm x 168mm x 50mm.
Weight (Including
Battery):
2.5lbs (1.1 kg).
Protection: IP54.
Keypad:
No. Keys:
16.
Display:
Format:
240 x 64 pixel graphic display, high contrast black-on-white, with backlight.
Viewing Angle:
Min 30°, typically 40°.
ENVIRONMENTAL
Operating
Temperature:
-4°F to 122°F (–20°C to +50°C).