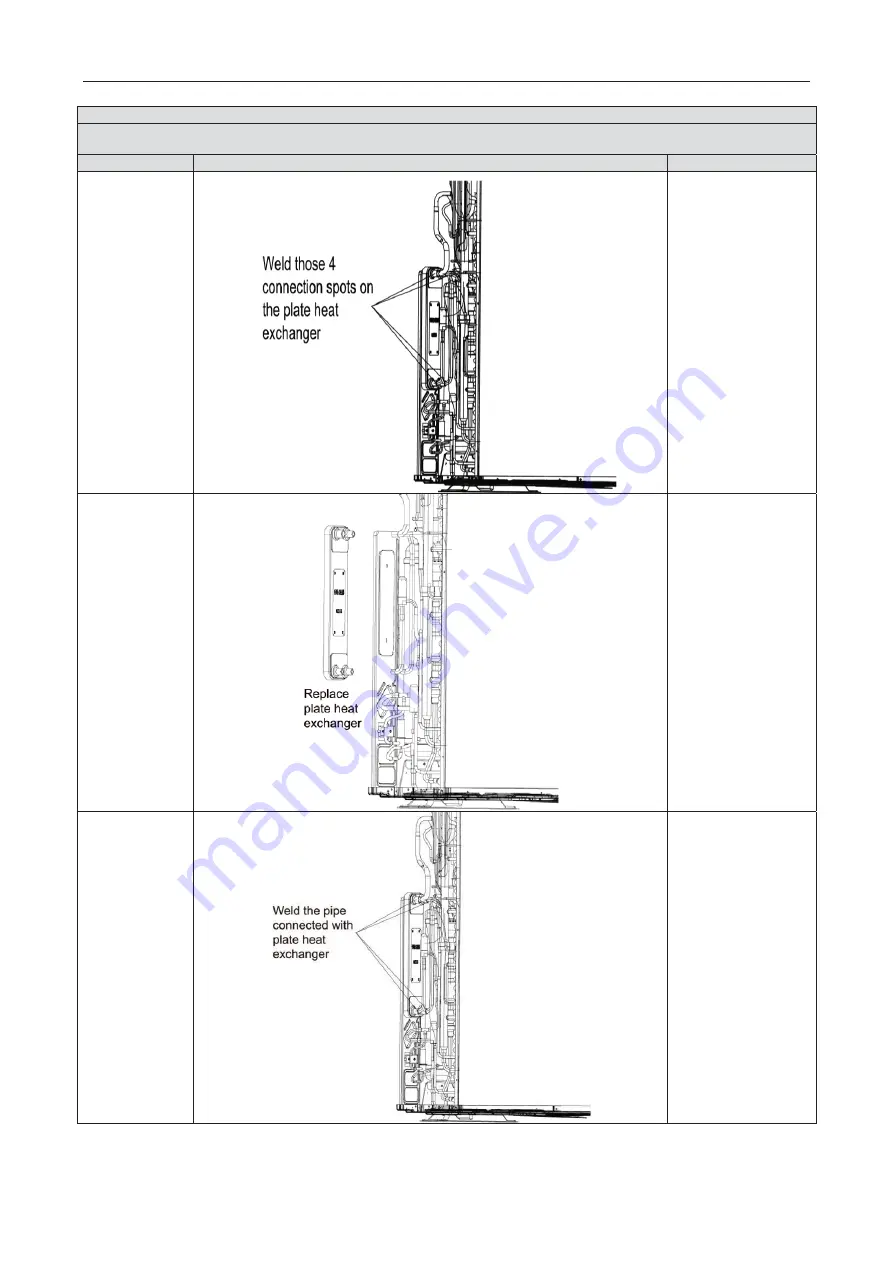
GREE DC Inverter Multi VRF System II Service Manual
116
Removal operation for plate heat exchanger
Remark: Before removing the plate heat exchanger, please make sure that there’s no refrigerant inside the pipeline of
system and disconnect the power
Process
Photo
Operation Instruction
2)Disconnect
inlet pipe and
outlet pipe of
plate heat
exchanger
● Weld those 4
connection spots on
the plate heat
exchanger, and then
pull out the
connection pipe.
Note: During welding
process, do not let
flame burn out other
parts
3)Replace plate
heat exchanger
●
Replace plate heat
exchanger
4) Replace gas
liquid separator
● Weld the pipe
connected with plate
heat exchanger
Note: During welding
process, do not let
flame burn out other
parts
Summary of Contents for GMV-100WL/A-T
Page 1: ...DC INVERTER VRF SYSTEM SERVICE MANUAL R410A...
Page 4: ...DC INVERTER VRF SYSTEM II SERVICE MANUAL R410A PRODUCT...
Page 16: ...GREE DC Inverter Multi VRF System II Service Manual 12 GMV 141WL C T...
Page 18: ...GREE DC Inverter Multi VRF System II Service Manual 14 CONTROL...
Page 64: ...GREE DC Inverter Multi VRF System II Service Manual 60 INSTALLATION...
Page 72: ...GREE DC Inverter Multi VRF System II Service Manual 68 DEBUGGING MAINTENANCE...
Page 173: ...JF00302323...