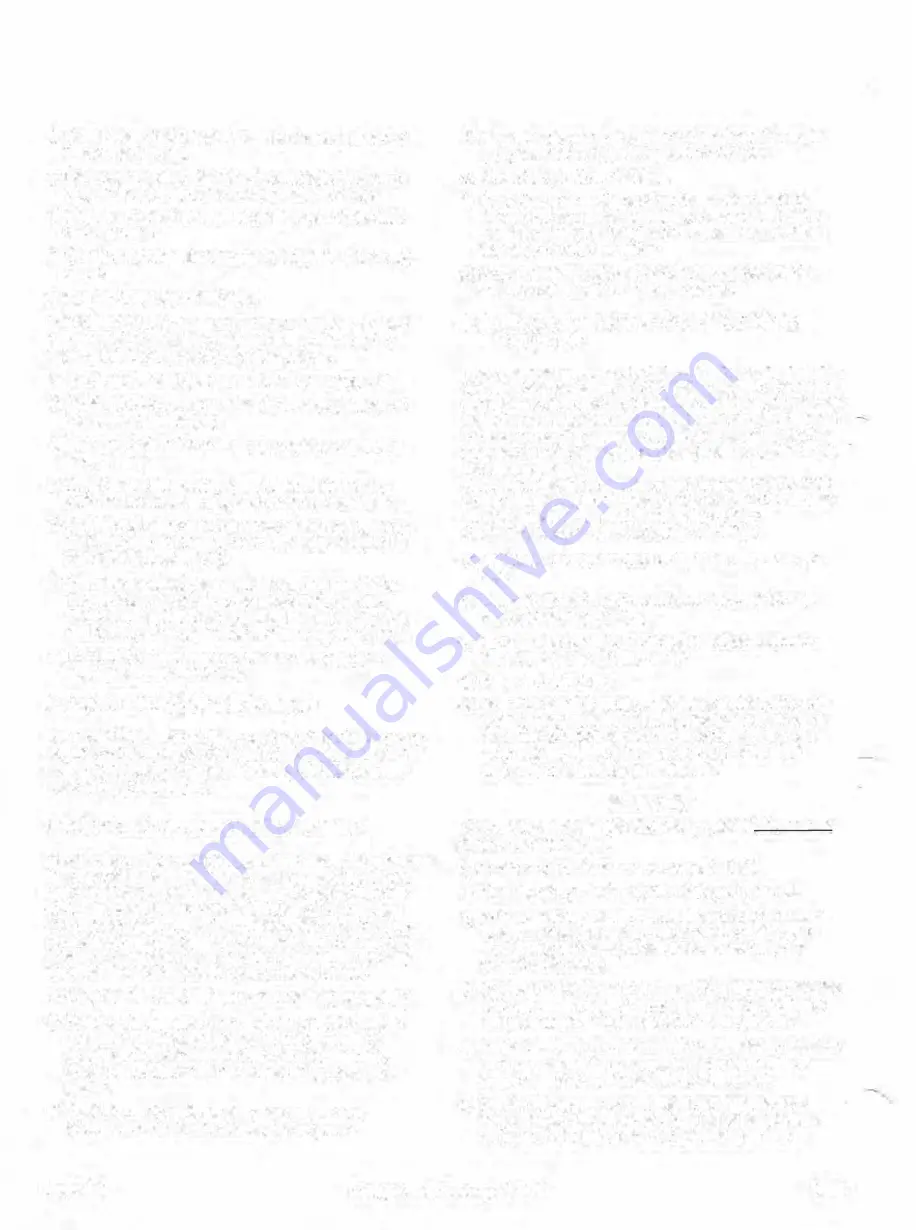
f) lnsert a new filter element, refit the retaining plate and
tasten the loek nut.
g) Refit the filter cover. Mind the condition of the sealing
ring so as to prevent leaks trom developing later.
h) Close the all drain stop valve at the bottom of the filter
housing again.
i) Check the oil level in the separator and, if required, top
up oiL
OIL PUMP SUCTION STRAINER
In full-flow oil pump designed packages also the oil pump
suction strainer element (15) requires maintenance. To
rernove this filter element proceed as follows:
a) Carry out the shut dow11 procedure in paragraph 7.3
b) Close the filter inlet stop valve (13). the stop valve and
the isolating valves (13).
c) Open the drain valve of filter (15) and catch up the oil
in an oil tray.
d) Withdraw the filter element and clean it thoroughly,
refit the filter in its housing and close the drain valve.
e) Slacken the nipple coupling on top of the filter houslng
tor a few (two or three) turns and !hen slowly open the
filter inlet stop valve (� 3).
n This oil pump filter housing will be purged now due to
the incoming oil stream. lf the oil is leaking via the
slackened nipple coupling, tighten this nipple coupling
and at last, open stop valves and isolating valves (i3).
g) To start up the compressor, reverse the shut down
procedure in paragraph 7.3.
6.10 MAJNTENANCE OF THE
'
OIL PUMP
Generally the full-flow oil pump and the lubrication oll pump,
are free of maintenance. For maintenance, repairing and
servicing the suppliers instructions, supplied to the pack
ages, should be followed.
6.11 CLEANING OF SUCTION GAS STRAINER
The filtering surface area of the strainer element is sufficient
to ensure effective filtration over many years of operation,
provided that the refrîgerant gas system has no worthwile
contamination. The strainer element has to be inspected
and cleaned according to the malntenance schedtile of the
package. Should the strainer be clogged due to a very dirty
system, this wîll show up in reduced compressor capacity.
To clean the strainer element proceeds as fellows:
a) Carry out the shut down procedure as in paragraph 7.3.
b) Remove the fasten!,!rs trom both the suctlon combina
tion cover and flanged connection of the pressure
equaliz,ing line and
remove the
cover
(lf
necessary.
loosen cover with a "soft" hammer); remove also the
gasket_
c) Carefully withdraw the strainer element trom the
strainer housing Without darnaging the 9auze,
d) Clean the element With a light solvent Then thorough
ly dry the element preferably with an air blast.
e) Check the gauze for damage.
f) lnsert the strainer element into the housing, refit the
cleaned or new gasket and place the cover with tight
ened nuts after the flanges of the pressure equalizing
line are mutually connected.
g) Purge the compressor and at last the refrigeration in
stallation as stated in the plant manuaJ.
6.12 (RE)ADJUSTMENT ELECTRIC SLIDEVALVE
ACTUATOR
The compressor package is delivered with an adjusted efec
tric slide valve actuator. Prior to starting the compressor for
the first time, the micro end switches of the electric valve ac
tuator have to be adjusted so tha1 the adjusting motor is cut
out, as soon as the capacity control slide valve inside the
compressor has reached one of its end stops (maximum or
minimum capacity).
This original setting rnay have been deranged during wotk
on the capacity control system, in Which event it is necess
ary to readjust the capacify contra! mechanism.
To readjust the limit cams proceeds as follóws:
a) Disconnec! the control cabinet trom the electric supply
line.
b) Remove the black knob for manual control by loosen
ing the internal set screw.
c) Remove the four cover mounting screws and remove
the elec1ric valve actuator cover.
d) Release motor brake.
e) Move the capacity contra! slide vatve to the maximum
(fully loaded) position
by
turning the output shaft clock
wise with a suitable wrench untill it stops at the maxi
m urn position stop. At the end of this (mechanica!)
stop a slight resistance is noticeable.
IMPORTANT
To prevent damaging the bal/ bearing spindel
Do not over
� the output shaft!
f) Turn the output shaft one full revolution back.
g) Mark the output shaft end with a feit pen or penciL
h) lfthe maximum position cam is loose on the camshaft
or is suspected of having moved relative to the cam
shaft, carry out steps j, k and 1. OtherWise carry out
steps m, n, o and P-
i) loosen the set screw on the maximum position cam (the
first cam away
trom
the compressor which actuate the
red wfred micro switch) with a 3/32 Allen wrench.
j) Rotate the maximum position cam clockwise on the shaft
unlil the rolfer switch just opens. Listen for a click or
check electrical continuity with an ohm-meter.
.k) Tîghten the set screw in the maximum position cam
very tightly to prevent /oosening. The capacity indica
tor plate on the end of the cam shaft should read
Page6.4
Compressor Package GSLP
92.01