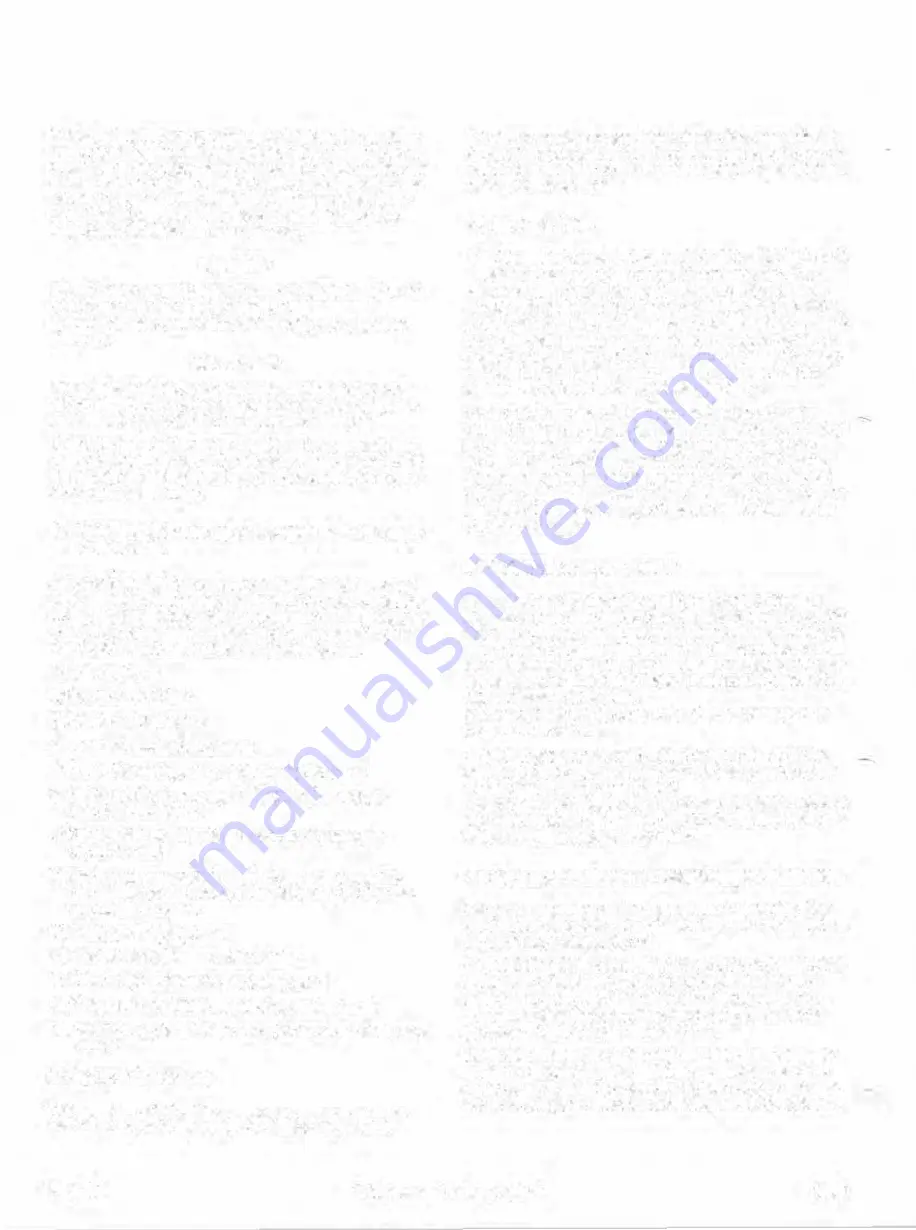
While the compressor is running each sight glass contains
foaming oil and small vapor bubbles. When clear vapor ap
pears in the top sight glass the oir level may be low. The oil
level can be áccurately checked when the compressor has
stopped and the oil has settled in the separator surnp for
about ten minutes. The oil level should be visible In the
sight gJass, between the two red marks.
WARNING
Do not remove caps, plugs, or other components when the
compressor is running or pressurized.
Stop compressor and refieve all intemal pressure before
doing
so.
IMPORTANT
Used or filtered oil shou/d never be added to a refrigerant
screw compressor under any circumstance. Use only new
oil (as in paragraph 2. 10) trom an oil manufacturer.
lf the addition of oil becornes too frequent, a problern may
have developed causing this excessive loss. See fault-find
ing (paragraph 6.13) under high oil consurnption for a prob
able cause and remedy.
6.4 MAINTENANCE AFTER THE INITIAL 200 HOURS OF
OPERATION
After the initia! 200 hours of operation a
few
maintenance
tasks are necessary to free the system of foreign materials
Whîch may have accumulated during assembly and installa
tion. Other procedures, stated below are required to sure
that the initia! operation of the machine is correct.
1) Change the oil
2) Replace the oil filter
3) Clean the ofl strainers
4) Clean the gas suction strainer
5) Check the settings of the capacity control cams
6) Check the pressure gauge calibration (0 bar when
open to atmosphere)
7) Trghten all balts, especially motor and compressor
mounting balts
8) Check compressor shaft seals
tor
excessive leakage
of 10 drops per minute. A small oil loss of 1 or 2 drops
per minute is normal.
9} Check coupling alignment
1 O) Check low oil pressure safety switch
î 1) Check high oil temperature safety switch
12) Check high discharge temperature safety switch
13) Restart and cfleck all operating ternperatures and pres
sures
6.5 SAFETY CONTROLS
The operation of all safety controls should be checked at
least monthly (as. in paragraph 4.14) as a safety switch
failure can result in an expensive repair_ lt is especially im
portant 10 regularly check the low oil pressure protective cir
cuit for fusing of the switch or delay timer contacts or failure
of the de lay timer coil.
6.6 OIL ANAL YS15
The oil injection screw compressor has proved to be a most
reliable and successfuJ compressor, but because of the
washing action of the oil. the oil quality must be checked
closely tor maximum compressor life. Since rr is impossible
to look at the oil and determine its quality, chemica! analysis
by a qualifîed concern signifies when to change the oil. Oil
analysis has proved to be of great value in preventing lubri
cation problems by diagnosing poor quality or contamîna
tfon before significant damage has been done.
lt in doubt to use the oil further more, take an oil sample
every 1,000 hours but at least every three months and send
it for laboratoty anaJysis. lf an unfavourabfe report îs
re
turned indicating a general dèterioration of the oil charge
(e.g. increased acidity high moisture content etc.), the old
package system oil should be drained off and separators re
filled
with
the correct charge of fresh oil (not reclaimed) of
the original grade.
6.7 MAINTENANCE SCHEDULE
The schedule (see next page) is intended as a minimum
maintenanoe schedule
.
and indicates after how many opera
ting hours
alo
terms maintenance operations have to be car
ried out. Abnormal conditions may require
more
frequent
actîon as determined by your daily listed readings. The year
ly maintenance jobs should ideally be carried out before the
start of the annual season.
For most of the maintenance tasks, the compressor must
be put out of action.
In order to prevent this from having to take place at incon
venient times, the tasks should as much as possible be ef
fected during a shut-down period.
The schedule has been drawn up in such a manner that sev
erat operations can be carried out simultaneously, which re
sults in reduced rnaintenance casts.
6.8 TOPPING UP Oll WITH COMPRESSOR OPERATING
Oil can be topped up whilst the package is operatîng. Use
the same oil as is already in the package (for the oil types to
be used, see Paragraph 2.10).
Oil should be preferably be added after the compressor has
stopped or been shut down. Add sufficient oil into the oil
separator to brîng the oll level into the sîght glass (1 to 3
quarters height) wîth a hand or electric pump capable of
pumping oîl agaînst a pressure of 7 bar.
When the compressor is running use a hand
or
an electric
pump to add oil through a 100 mesh strainer into either of
the normally plugged connections on each side of the elec
tric
valve
actuator ln the suction housîng of the compressor.
Page 6.2
Compressor Packa,ge GSLP
92.01