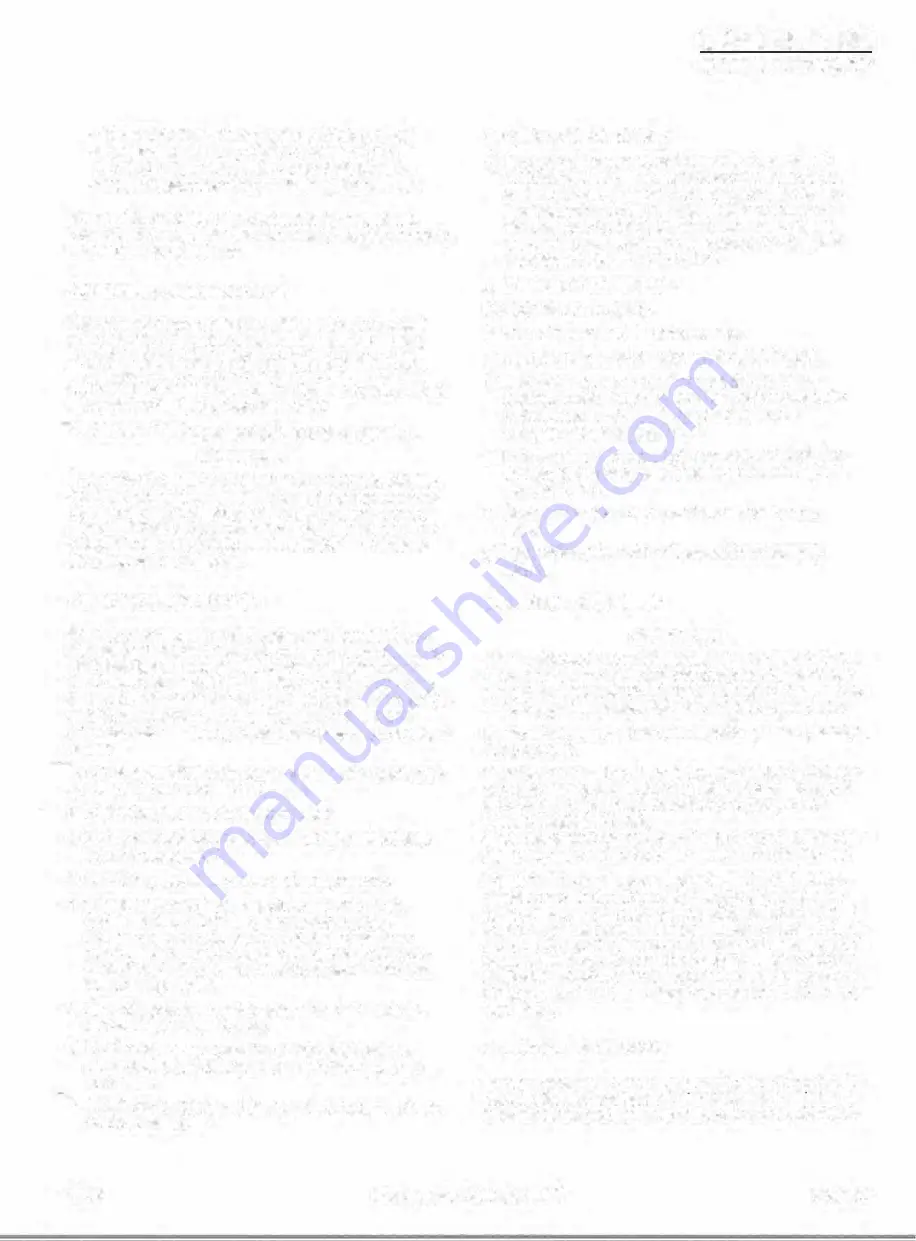
- temperature sensor of capacity controller (48 - 49)
� pressure sensor of capacity controller (50 - 51)
BEWARE� Connection X50 == exclusiveJy for DC+
- current transformer ot current limiting unit (46 - 47)
The provisions marked with an asterisk (1 are optional.
Theretore ifthese provisions are omltted. the corresponding
connections are out of use.
4.9 PACKAGE PRESSURE TEST
The package components have all been pressure tested
prior to leaving the factory. The compressor unit should,
however. be leak-checked at the job site to detect leaks
whîch may be present due to rough handling during ship
ment. This test sholJld be done simultaneously with the sys
tern pressure test and system leak check.
ïo
not
add oil to the package prior to pressure testing.
IMPORTANT
Whenever the compressor package is co/der than fhe con
densing temperature, admit onfy enough high pressure r�
frigerant to bring the paokage up to the test pressure and
then close the in/et stop valve. This minimizes the amount
of liquid condensing in the package which could damage
the compressor on start up.
4.10SYSTEM EVACUATION
Any free moisture and air in
a
system will mix with the re
frigerant and oil to form harmful organlc contamlnants in re
sinous sludge and wax like forms which will plug thê oit
filters and strainers and damage the compressor_ The sys
tem must
be
evacuated to remove both the air and the mois
ture. This evacuation can
be
done with a high vacuum
pump capab.te of reducing the absolute pressure to
1 .. 3
bar
or less.
"'o not evacuate with oil in the separator as the oir prevents
c1.ny trapped moisture from boiling off.
The following procedure is recommended:
a)
Ensure all leaks have been corrected by pressure test
ing as in paragraph 4.9.
b) Blow the system down to atmospheric pressUre.
c) As many vacuum pumps contain brass which ïs at-
1acked by ammonia in the presence ot moisture,
remove any ammonia remaining in the system trom
the pressure test by adding dry nitrogen to a pressure
of about D.7 bar(e). Again blow the system down to al
mospheric pressure.
d) Open all the interconnecting stop vaives between the
low and high pressure sides.
A)
Insta.Il
a vacuum 9au91,1 at the oil
filter
drain valve
or
some ether corwenient system connectlon. Open the
drain valve.
.
Attach the vacuum pump by hose to the blowdown valve
on the oil separator.
g) Open the blowdown valve.
GRBSSa
IIEIE"NCSV00RS04RFT/IIETAIEtlSAHl.ElT'IJtOC,
INS'TFcUCTICIN.....,.��
h) Start the vacuum pump and evacuate the system to
1 .33
bar(a). Depending on the intemal volume of the
system. the amount of air and water present, the am
bient temperature and the size of the vacuum pump
this may take irom half an hour
to
ten hours. Should
the ambient temperature be less
than O
·c,
evacuate
the systern to 0.20 Torr (26.6 Pa).
j) Close the blowdown valve.
k) Stop the vacuum pump.
1) Record the system absolute pressure.
m) Wait two hours and repeat steps f. g. h, j, k and
1.
n) Wait tor two hours and read the system _absolute
pressure again. lf the pressure has not incre
_
ased
,
de
hydration has complete. lf the pressure has m
creased, repeat steps as in ·m".
o) tf the vaouum fails to hold atter several dehy_dration al
tempts, check the system tor leaks and agam repeat
steps as in urn•.
p) Close the blowdown
va/ve
and the vacuum gauge
valve.
q) Charge the system with refrigerant at the charging
valve.
4.11 INITIAL OIL CHARGE
IMPORTANT
Used or filtered
oi/
should MW J2p added to
a
refrigerat;on
screw compressor under any circumstance. Us� on/y ne�
oi/
trom an oil manllfacturer (any of the major 01/ compames
or their approved dealers)
as
in the of/ table in para 2. 10.
Before charging any oil in1o the screw compressor package,
see para.
2.10.
Sufficfent oil should be charged into the (primary) oil separ
ator reservoir via the oil charging valve
to
establish a level
in the oil level sight glass. Refer for oil capacity the oil
cooler indentification plate.
When the desired oil level is reached, most of the oil system
pipes, oil cooler, oil filter and compressor are filled up too.
Check that the bearings are prelubricated by loosening a
nipple on the discharge journal oil sup�ly line at the com-.
presser bearing and pump a small add1t1onal a'!'ount of 011
until oil weeps at the loosened nipple. Make_a f1nal check by
pumping further oil and noting the pre
s
sure rnc,:ease o� the
oil pressure gauge. Revolve the compressor d�1ve shaft by
hand a few times to prevenl liquid hammer at first start and
to topping up the oil separator to the main level of the upper
sight glass.
4.12 INITIAL OIL WARM UP
Supply power to the compressor pa�el before th� arrival
o!
the Suppliers representative. Th1s w1/I allow the 01� In the 011
reservoir to warm to operatingr temperature and vv1fl help fa-
92.01
Compressor Package GSLP
P-age4.5