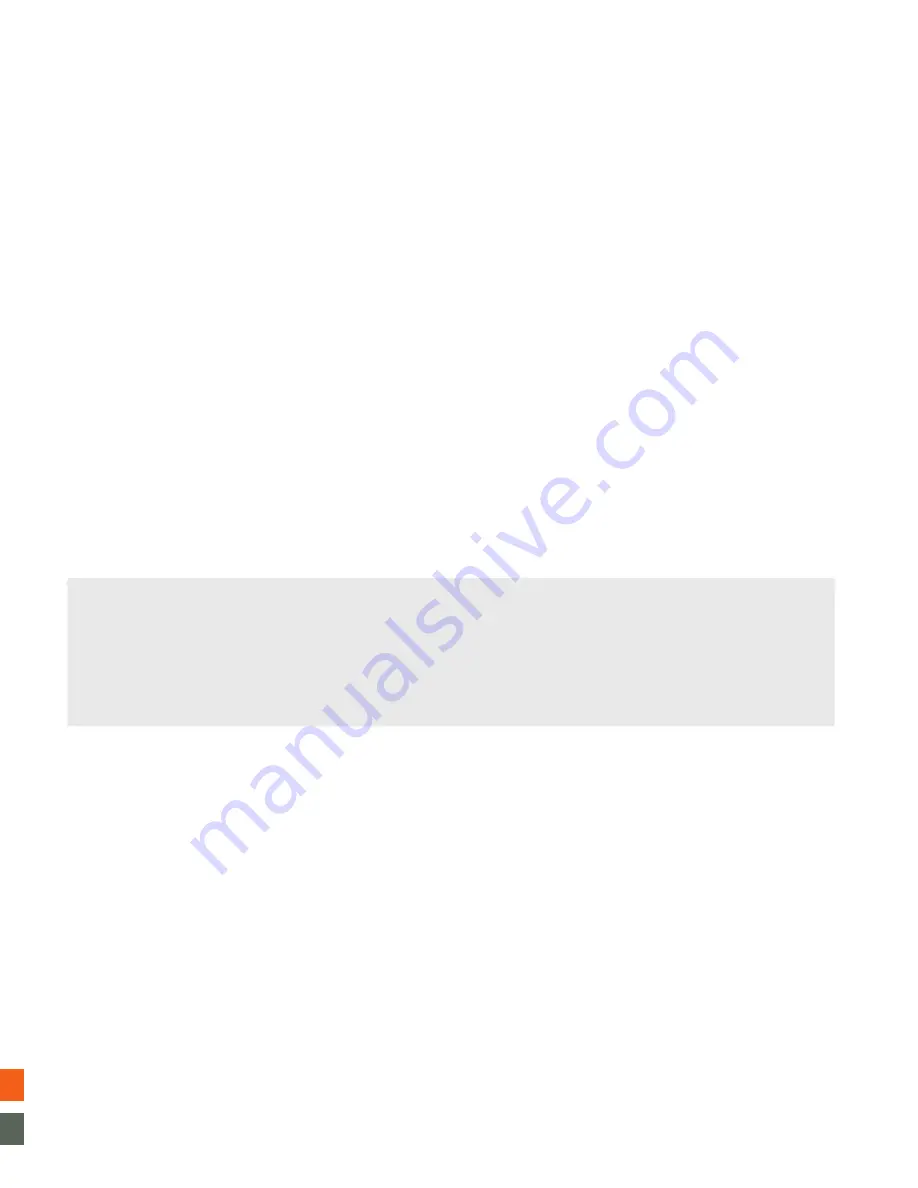
FULL FUNCTION TEST (SEE CHECKLIST IN APPENDIX IV)
SYSTEM CHECKS
1.
Check that no unauthorized modifications have been made to the UAM. Check that the Ayre’s T-piece is present and
spares as originally supplied are present. Check oxygen tubing for venturi (Hudson type) mask is available.
2.
UAM frame – check for any loose screws or panels and tighten as required. Check wheels.
3.
Check mains cable and gas supply tube condition and repair as required.
4.
Connect mains supply, turn on mains isolator switch (note that there will be a delay of around 10 seconds while the mains
filter starts) and check that the oxygen analyzer and patient monitor (if fitted) yellow charging LED’s are visible.
5.
Turn off the machine mains isolator and ensure that the Mains Power Indicator goes red – this indicates mains failure.
6.
Check that the battery indicator icon shows three green segments and that it discharges with mains off and recharges
with mains on. NOTE: Battery must be replaced every three years or sooner if battery life is low.
7.
Check that the cylinder yoke seals are fitted and replace if damaged or missing.
8.
Connect the cylinders to the yokes and ensure that the cylinder pressure is indicated on the correct pressure gauge
(nitrous oxide and oxygen) when turned on individually.
9.
Connect the machine pipeline hoses to the supply outlets (wall outlet or bullnose cylinder regulator) and ensure that
pipeline pressure is indicated on the correct pressure gauge (nitrous oxide and oxygen) when connected and turned on
individually.
10.
Turn on the oxygen and the nitrous oxide flow dials using each gas supply (concentrator, cylinder and pipeline) and ensure
that the maximum flow of 10 L/minute is achieved for each gas.
11.
Close the flow dials and ensure that the flow stops.
12.
Check that the emergency oxygen inlet functions by observing an increase of oxygen % on the analyzer.
OXYGEN CALIBRATION, SAFETY AND QUAVLITY CHECKS
13.
Turn on the analyzer screen and ensure that the vaporizer is off. Turn on the oxygen cylinder or pipeline to provide 100%
oxygen, turn on a 6 liter/minute flow and wait for the oxygen sensor to stabilize, then press CAL – O2 – GO and wait for
the calibration to finish, then go back to the main display by pressing EXIT twice. If the oxygen sensor fails to calibrate or
an oxygen sensor exhausted alarm is present, replace the oxygen sensor.
NOTE:
For the most accurate performance over the entire range of possible oxygen concentrations, the oxygen sensor must
be c
alibrated with both 100 % oxygen and 21% oxygen (room air). If 100% oxygen is not available then the it should at least be
calibrated with 21% oxygen. If the sensor has not been calibrated at 100% oxygen then the monitor will display 104% at higher
oxygen concentrations. Calibrating the cell at 100% oxygen can clear this condition.
NOTE:
The oxygen sensor will need to be replaced approximately every 12 months. An alarm will indicate when the oxygen
sensor is exhausted.
14.
With the oxygen turned off cycle the bellows to draw in air, wait for the oxygen sensor to stabilize, then press CAL – AIR
– GO and wait, then press EXIT to go to the main display. If the sensor fails to calibrate or an oxygen sensor exhausted
alarm is present replace the oxygen sensor.
15.
Check that the high and low oxygen percentage alarms can be adjusted and that they function; this is achieved by turning
up the oxygen supply to exceed the high alarm or increasing the entrained air to fall below the lower alarm.
16.
Increase the nitrous oxide flow and ensure that it cuts off when the oxygen concentration is 25% or lower.
17.
Disconnect the oxygen sensor (mounted by the bellows in Configuration
A
, behind the rear top access panel in
Configuration
B
) – ensure that the disconnect alarm sounds and that nitrous oxide (if fitted) turns off.
18.
Set a 6 L/minute flow from the oxygen concentrator and ensure that the output stabilizes at 90% – 96% oxygen
concentration. increase the flow rate to 10 L/minute and ensure that the output remains at 90% or better. If the output
concentration is low check the filter condition and replace it if required.
BREATHING SYSTEM CHECKS
19.
Turn on the oxygen flow with patient Y-Piece blocked and ensure that the reservoir bag fills and excess gas escapes
through the pressure relief valve and that maximum circuit pressure is around 5 cmH
2
0. Confirm that the apnea alarm
sounds with a full bellows after 30 seconds and that it repeats every 30 seconds.
20.
Turn off the flowmeter and cycle the bellows and ensure that air is drawn in through the under pressure valve – this is
indicated by a slight fluttering of the reservoir bag when it is empty.
21.
Check condition of reservoir bag.
22.
Check that the bellows assembly is securely connected to the machine and is undamaged, check for splits in the bellows
or displacement of the end plates, loosen and re-clamp centrally if required.
18
Summary of Contents for Universal Anaesthesia Machine
Page 1: ...Universal Anaesthesia Machine Maintenance Manual...
Page 14: ...12...
Page 39: ...37 2 3 6 41 35 33 32 36 32 34 38 37 35 33 32 36 41 32 6 4 5 46 15 45 49 48 B B...
Page 40: ...38 41 36 37 39 6 40...
Page 41: ...39 25 27 29...
Page 48: ...NOTES...
Page 49: ......