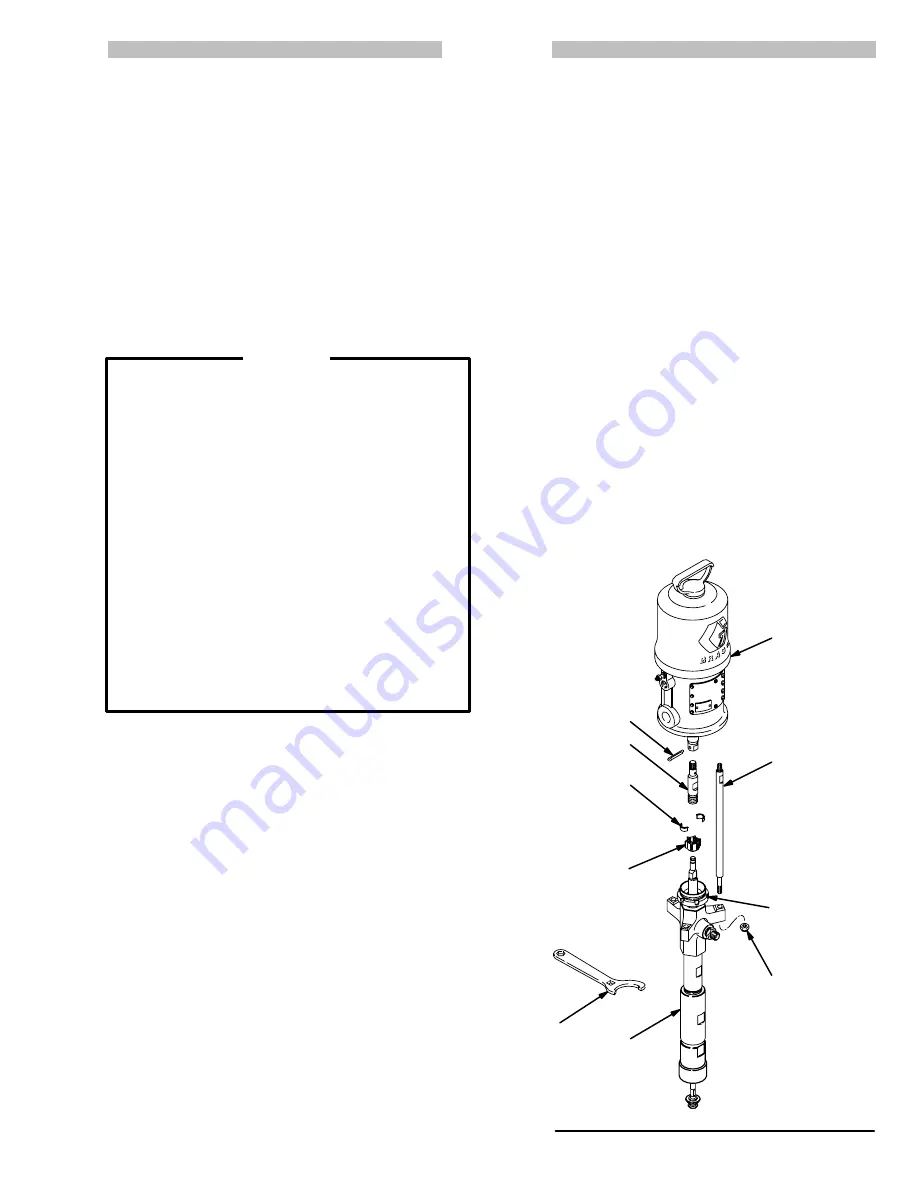
9
SERVICE
REQUIRED TOOLS
Torque wrench
Bench vise, with soft jaws
Hammer
Rubber mallet
Razor or other sharp tool
8 mm (5/16 in.) dia. brass rod
8 mm, 11 mm, 15 mm, 25 mm,
3/4 in. and 7/8 in. open–end wrenches
17 mm box or socket wrench
22 mm crow’s–foot wrench
Adjustable wrenches
24 in. adjustable wrench
Thread lubricant
Anaerobic thread sealant
DISCONNECTING THE DISPLACEMENT PUMP
KEEP HANDS AND FINGERS AWAY FROM THE
PRIMING PISTON DURING OPERA TION AND
WHENEVER THE PUMP IS CHARGED WITH AIR
to reduce the risk of injury!
On the pump down-
stroke the priming piston extends beyond the intake
cylinder to pull the material into the pump. The prim-
ing piston works under extreme force. During opera-
tion and whenever the pump is charged with air, the
priming piston can severely injure or amputate a
hand or finger, or break a tool, caught between it and
the intake cylinder. Always follow the
Pressure Re-
lief Procedure Warning
on page 8, before check-
ing, clearing, cleaning, flushing or servicing any part
of the pump.
The air motor piston (located behind the air motor
plates) also moves when air is supplied to the motor.
NEVER operate the pump with the air motor plates
removed. Before servicing the pump, follow the
Pressure Relief Procedure Warning
on page 8, to
prevent the pump from starting accidentally.
WARNING
1. Flush the pump if possible. Stop the pump at the bot-
tom of its stroke. Follow the
Pressure Relief Proce-
dure Warning
on page 8.
2. Disconnect the air hose. Hold the fluid outlet fitting
(7) with an adjustable wrench to keep it from being
loosened while you disconnect the fluid hose. Re-
move the pump from its mounting. Note the relative
position of the pump’s fluid outlet to the air motor’s air
inlet.
3. Using an adjustable wrench, unscrew the coupling
nut (104) from the connecting rod (103). Remove the
coupling collars (105). Take care not to lose or drop
them. See Fig 3.
4. Hold the tie rod flats with an 11 mm wrench to keep
them from turning. Use the wrench (1 13) provided
with the pump (or a 17 mm box or socket wrench) to
unscrew the tie rod locknuts (106) from the tie rods
(102). Carefully pull the displacement pump (107) off
the air motor (101).
5. Refer to page 10 for displacement pump service. To
service the air motor, refer to the separate air motor
manual, supplied.
RECONNECTING THE DISPLACEMENT PUMP
1. Orient the pump’s fluid outlet to the air motor’s air in-
let as was noted in step 2 under
Disconnecting the
Displacement Pump.
Position the displacement
pump (107) on the tie rods (102). See Fig 3.
NOTE:
If you removed the tie rods (102) from the air mo-
tor (101) or air motor adapter plate, reinstall
them using an 11 mm wrench. Torque the rods to
20–25 N.m (15–18 ft–lb) on Model 222–783, and
34–41 N.m (25–30 ft–lb) on Model 222–782.
2. Screw the locknuts (106) onto the tie rods (102) and
torque to 34–41 N.m (25–30 ft–lb), using the wrench
(113) provided (or a 17 mm box or socket wrench).
3. Place the coupling nut (104) on the displacement
rod, then place the coupling collars (105) in the nut.
Screw the coupling nut onto the connecting rod (103)
loosely. Hold the connecting rod flats with an adjust-
able wrench to keep it from turning. Using an adjust-
able wrench, torque the nut to 41–48 N.m (30–35 ft–
lb).
4. Using a torque wrench in the square hole of the
supplied wrench (113), torque the packing nut (2) to
27–34 N.m (20–25 ft–lb).
5. Mount the pump and reconnect all hoses. Reconnect
the ground wire if it was disconnected during repair.
Turn on the air to the motor and run the pump slowly.
6. Fill the packing nut/wet–cup 1/3 full of Graco Throat
Seal Liquid or compatible solvent.
Fig 3
101
103
105
107
102
TORQUE TO
20–25 N.m
(15–18 ft–lb)
ON MODEL
222–783;
34–41 N.m
(25–30 ft–lb)
ON MODEL
222–782
106
TORQUE TO
34–41 N.m
(25–30 ft–lb)
104
TORQUE TO
41–48 N.m
(30–35 ft–lb)
108
2
TORQUE TO
27–34 N.m
(20–25 ft–lb)
0204A
113
Summary of Contents for Metric CHECK-MATE 200
Page 26: ...26 NOTES...
Page 27: ...27 NOTES...