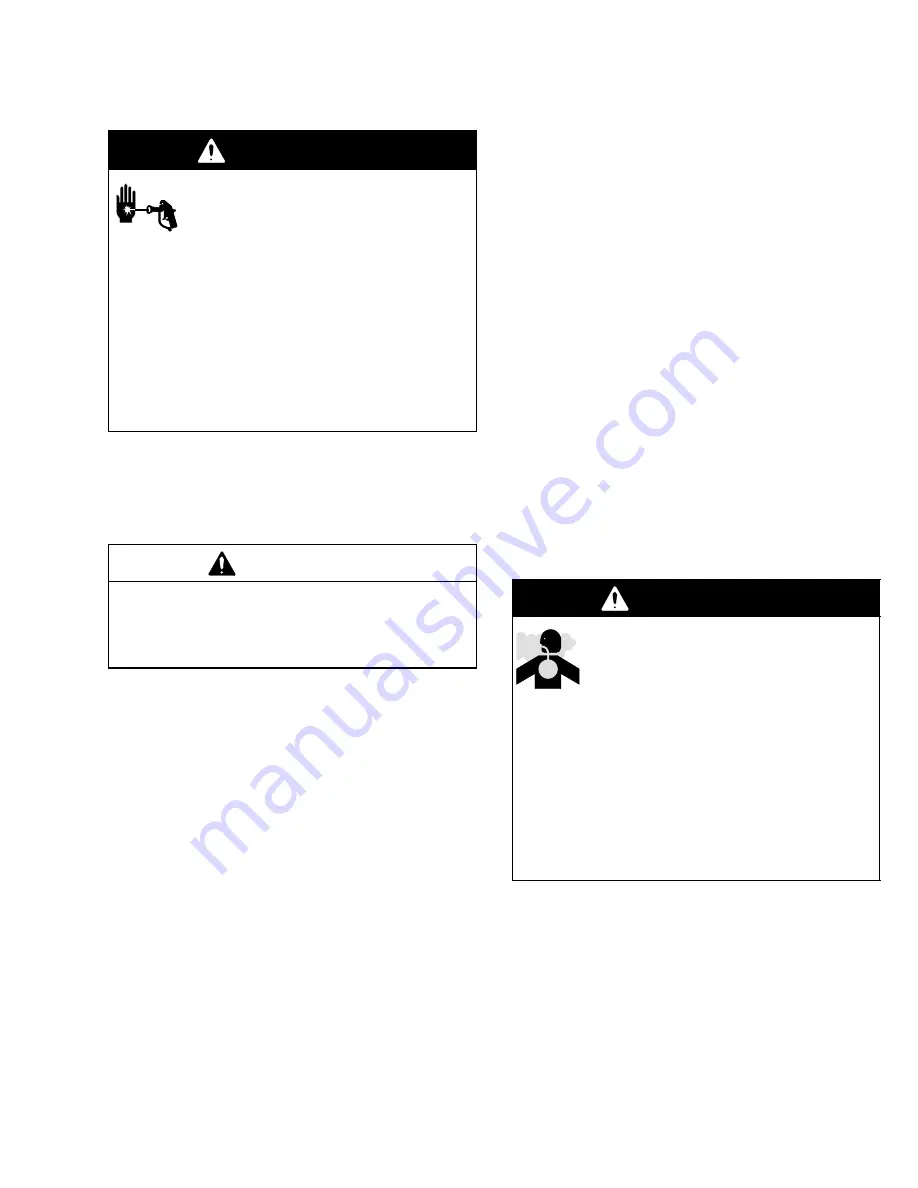
308986
23
Operation
Pneumatic Pressure Relief Procedure
WARNING
INJECTION HAZARD
The system pressure must be manually
relieved to prevent the system from
starting or spraying accidentally. Fluid
under high pressure can be injected through the
skin and cause serious injury. To reduce the risk of
an injury from injection, splashing fluid, or moving
parts, follow the
Pressure Relief Procedure
if the
spray tip/nozzle clogs and whenever you:
D
are instructed to relieve the pressure,
D
stop spraying,
D
check or service any of the system equipment,
D
or install or clean the spray tip.
1.
Engage the dispensing valve safety latch.
2.
Shut off the feed pump and proportioning pump air
regulators and bleed-type master air valves.
CAUTION
If material is left in the heaters without fluid move-
ment, the material could “cook” and ruin the coating
as well as plug the heater. The heaters have a large
mass and take several minutes to cool.
3.
If the system has heaters, turn the power off to the
heaters 10 minutes prior to the completion of the
application.
4.
Flush the system immediately after completion of
the application.
5.
Disengage the dispensing valve safety latch.
6.
Hold a metal part of the dispensing valve firmly to
the side of a grounded metal pail, and trigger the
dispensing valve to relieve pressure.
7.
Engage the safety latch.
8.
Open the mixer manifold drain valves, having a
container ready to catch the drainage. Close the
valves immediately.
9.
Use the solvent pump to flush the mixer manifold
solvent valves and fluid line(s) to the applicator.
10. Ensure pump air pressure and main air valve are
closed.
11. If you suspect that the nozzle or hose is com-
pletely clogged, or that pressure has not been fully
relieved after following the steps above:
a.
Remove and clean tip from spray gun.
b.
Direct the gun into a grounded container and
slowly trigger the gun.
c.
If system is still plugged, very slowly loosen
the fitting at the mix manifold 1/4 turn, allow
liquid to run out until pressure is relieved.
d.
Remove and clean or replace plugged compo-
nent .
e.
Tighten any loosened fittings.
f.
Very slowly loosen the nozzle or hose end
coupling and relieve pressure gradually, then
loosen completely. Now clear the nozzle or
hose.
Handling Plural Component Fluid
WARNING
PLURAL COMPONENT FLUID
HAZARD
Be extremely cautious when handling
plural component materials and solvents
used with them. Some are extremely
toxic. See the
Toxic Fluid Hazard
warnings on
page 5. Read and follow the coating and solvent
manufacturer’s safety precautions and warnings.
Wear the proper protective clothing, eye protection,
gloves, and clean air breathing apparatus as
prescribed by the fluid manufacturers recommen-
dations, O.S.H.A. regulations and as approved by
N.O.I.S.H. for the chemicals being used.
Observe the Pot (Workable) Life Limit
Flush the mixed fluid out of the mixer, dispensing lines
and equipment before it hardens. Flush the complete
system when necessary to prevent the fluids from
hardening in the equipment and hoses. Check the fluid
manufacturer’s instructions for fluid shelf life, and flush
the entire system before this time is reached. Flush the
system with a compatible solvent as explained on
page 21.
Summary of Contents for HYDRA-CAT FIXED RATIO
Page 38: ...38 308986 Notes...
Page 39: ...308986 39 Notes...