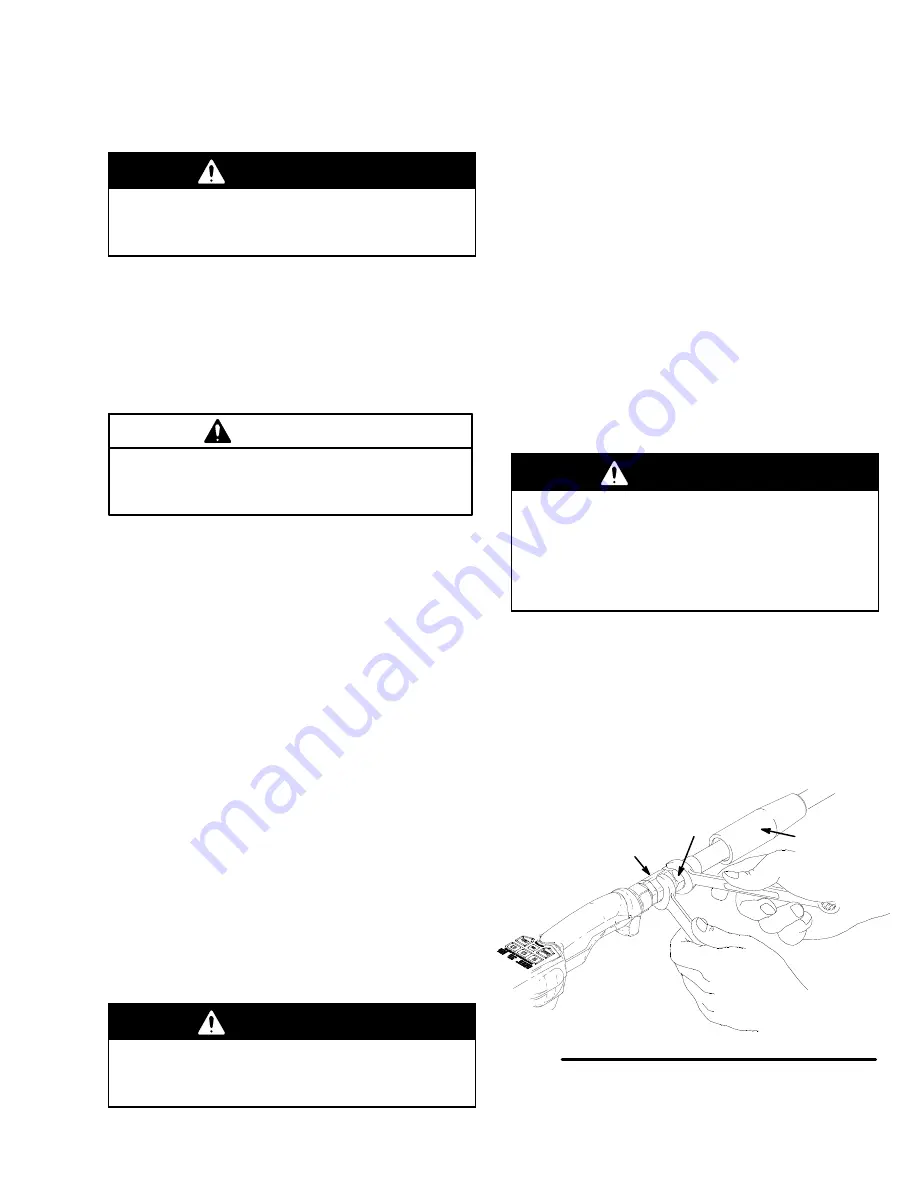
Installation
Pre-Installation Procedure
1.
Relieve the pressure.
To reduce the risk of serious injury whenever you
are instructed to relieve pressure, always follow the
Pressure Relief Procedure above.
2.
Close the shut-off valve (item J in Fig. 1).
3.
Ground the hose and reel or console. See
Grounding on page 6. Do not use Teflon
tape
on the pipe joints; it may cause a loss of ground
across the pipe joint.
Installation Procedure
If this is a new installation, or if the oil in the
lines is contaminated, flush the lines before you
install the metered valve.
1.
If this is an existing installation, go to step 7.
Steps 2 through 6 are the
Flushing Procedure
.
2.
Close the fluid shut-off valve (J) at each dispense
position.
3.
Make sure the main fluid outlet valve at the pump
is closed, the air pressure to the pump motor is
adjusted, and the air valve is open. Slowly open
main fluid valve.
4.
Place the hose end (with no dispense valve
connected) into a container for waste oil. Secure
the hose in the container so it will not come out
during flushing. If you have multiple dispense
positions, first flush the dispense position farthest
from the pump, and work your way toward the
pump.
5.
Slowly open the shut-off valve (J) at the dispense
position. Flush out a sufficient amount of oil to
ensure that the entire system is clean, and close
the valve.
6.
Repeat step 5 at all other dispense positions.
7.
Relieve the pressure.
To reduce the risk of serious injury, whenever you
are instructed to relieve pressure, always follow the
Pressure Relief Procedure on page 4.
8.
Loosen and disconnect the hose from the old
dispense valve (the one that you are replacing).
9.
Slide the swivel cover (4) onto the hose, small end
first. See Fig. 3.
10. Apply thread sealant to the the male threads of the
hose fitting, thread the hose fitting into the swivel
(3) of the EM5, and tighten firmly. See Fig. 3.
11. Thread the extension (5a, 6a, or 7a) into the outlet
of the EM5, and tighten firmly. For rigid
extensions, thread the extension in at least
three full turns, position the extension for
proper alignment, and tighten the sealing
nut (5c or 7c). See Fig. 4.
12. Thread the new dripless nozzle (5b, 6b, or 7b)
onto the extension, and, with an open-end
adjustable wrench on the flats of the nozzle,
tighten firmly. See Fig. 4.
Do not use the old non-drip nozzle (Part No.
203–655) or any other manual shut-off nozzle on
the EM5 extension. You must use the new nozzle
that is provided with the EM5. The old nozzle
could rupture under pressure, and the EM5 could
be damaged.
13. Open all dispense position shut-off valves, and
start the pump to pressurize the system. See the
Operation section for proper operation of meters.
14. To ensure dispensing accuracy, purge all air from
the fluid lines and dispense valves before you use
them. Set the system flow to the desired flow rate,
which is typically 1.5 gpm. Flow rates in excess of
5 gpm may cause metering errors.
3
hose fitting
Slide onto
hose before
connecting.
06187
Fig. 3
4
Summary of Contents for EM 238-451
Page 19: ...Notes...