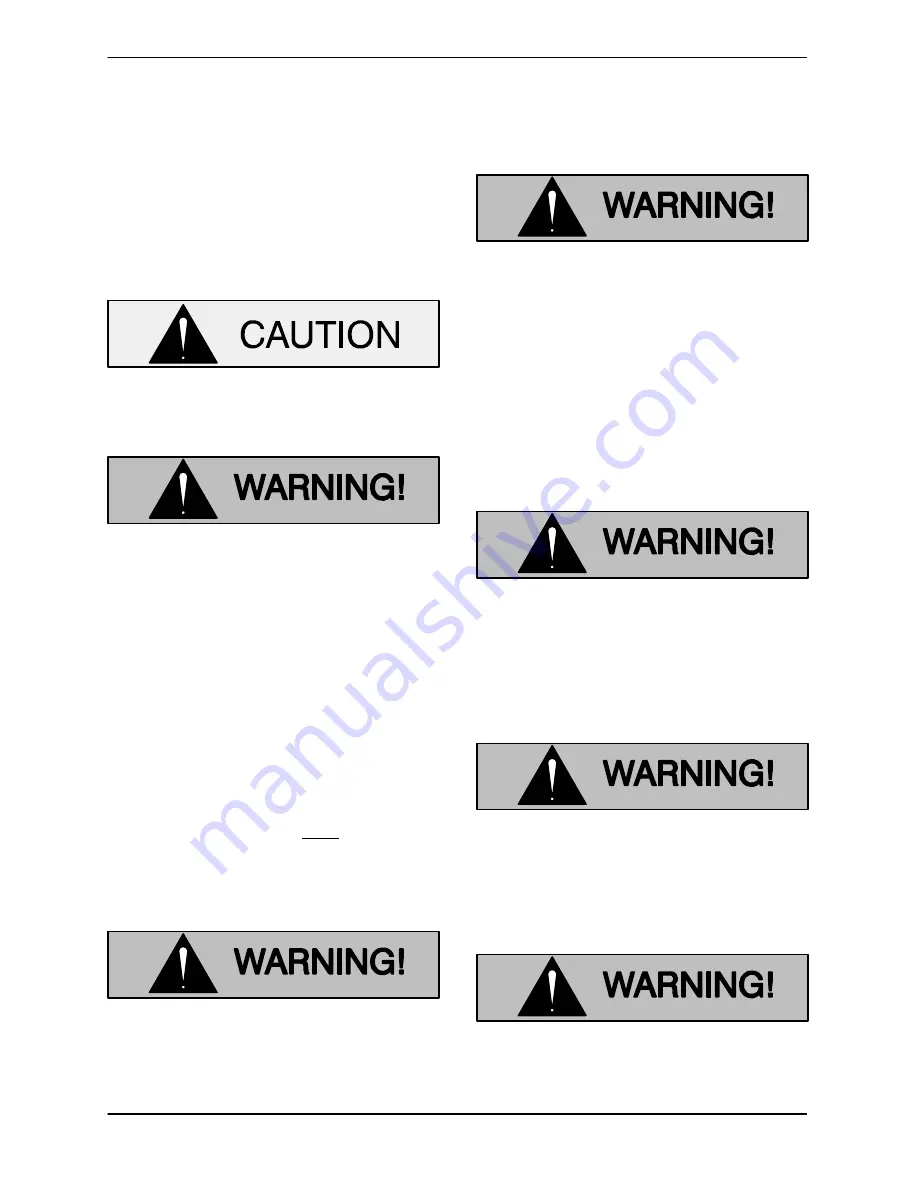
OM-04386
GMS SERIES
SAFETY
PAGE A-1
SAFETY - SECTION A
This information is specific to Gorman‐Rupp GMS
Series Rotary Gear Pumps.
It applies throughout
this manual and any manual or literature ac
companying the pump.
In addition to this manual, see the separate litera
ture covering the drive unit used to operate this
pump.
Pumps and related equipment must be in
stalled and operated according to all na
tional, local and industry standards.
This manual will alert personnel to
known procedures which require spe
cial attention, to those which could
damage equipment, and to those which
could be dangerous to personnel. How
ever, this manual cannot possibly pro
vide detailed instructions and precau
tions for each specific application or for
every situation that might occur during
maintenance of the unit. Therefore, it is
the responsibility of the owner, installer
and/or maintenance personnel to en
sure that applications and/or mainte
nance procedures not addressed in this
manual are performed only after estab
lishing that neither personal safety nor
pump integrity are compromised by
such applications or procedures.
Before attempting to install, operate, or
service this pump, familiarize yourself
with this manual, and with all other liter
ature shipped with the pump. Unfamil
iarity with all aspects of pump operation
covered in this manual could lead to de
struction of equipment, injury, or death.
The standard version of this pump is de
signed to handle a wide range of light,
medium, and heavy viscosity liquid, de
pending on design and components,
and a range of temperatures when fitted
with different seals. Do not apply at
higher temperatures than the seal will
handle. Do not attempt to pump liquids
which may damage the pump or endan
ger personnel as a result of pump fail
ure; consult the factory for chemical
compatibility.
If the pump and motor are furnished
mounted on a base, make certain that all
lifting devices have adequate capacity.
If chains or cables are used in lifting,
make certain that they are positioned so
as not to damage components, and so
that the load will be balanced.
After the pump has been installed, make
certain that the pump and all piping or
hose connections are secure before op
eration. Loose connections can result in
damage to the equipment and serious
injury to personnel.
Never operate the pump without a pres
sure relief valve installed on the pump
or in the discharge piping. Make certain
that pump‐mounted pressure relief