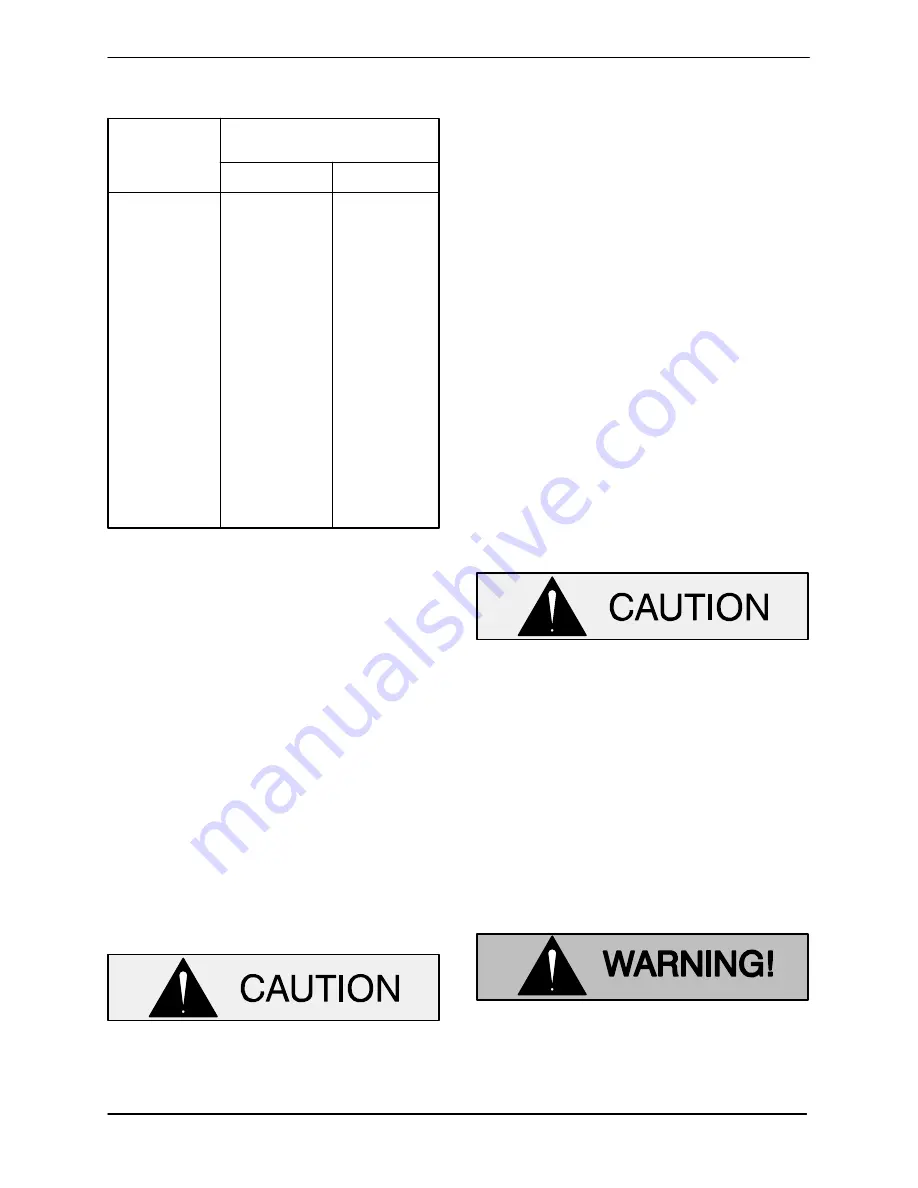
GMS SERIES
OM-04386
PAGE B-2
INSTALLATION
Table B‐1. Theoretical Displacement
Hydraulic
Size
Theoretical Displacement
Per Revolution
Gallons
Centimeters
3
DC
0.00568
21.486
DE
0.00704
26.646
GC
0.00967
36.619
GF
0.01405
53.186
GH
0.01915
72.479
GJ
0.02317
87.700
JG
0.03579
135.49
JJ
0.05159
195.28
JL
0.07078
267.94
JP
0.10078
381.48
NK
0.10665
403.71
NM
0.14173
536.51
NP
0.17681
669.31
RM
0.24030
909.65
RP
0.29979
1134.8
RR
0.35927
1360.0
RS
0.41876
1585.1
SR
0.65752
2489.0
SU
1.10240
4173.2
TU
1.91280
7240.7
PREINSTALLATION INSPECTION
The pump assembly was inspected and tested be
fore shipment from the factory. Before installation,
check for damage which may have occurred dur
ing shipment. Check as follows:
a. Inspect the pump assembly for cracks, dents,
damaged threads, and other obvious dam
age.
b. Check for loose attaching hardware. Since
gaskets tend to shrink after drying, check for
loose hardware at the mating surfaces.
c. Carefully read all tags, decals, and markings
on the pump assembly, and perform all duties
indicated.
STORAGE
Due to the extreme close machining toler
ances within rotary gear pumps, proper
storage before installation is essential to
prevent damage to the pump.
If the pump will not be immediately installed, follow
these procedures or damage to the pump will oc
cur.
a.
Do not
flush the pump. Ensure that the port
plugs shipped with the pump remain in place
until piping is installed to help prevent dust or
other foreign objects from entering the pump.
b. Pumps that will not be installed for an ex
tended period should be stored indoors if
possible. The factory‐installed port plugs will
not
ensure protection from excessive humid
ity, splash water or rain. In very humid or wet
conditions, install air‐tight plugs in the ports
and fill the pump completely with a lubricating
preservative liquid that is compatible with the
liquid to be pumped.
c. Pumps stored outdoors
must be fully pre
served
as described above,
completely
cov
ered
with plastic or other water‐tight material,
and the covering anchored to ensure that it
will not be blown off.
Flushing
Clean piping is essential because of close‐
tolerance moving parts in this pump. Flush
all dirt, grit, weld beads or scale from the
suction piping before installing the pump.
Damage to the pump because of debris in
the suction line is not covered by the pump
warranty.
The pump may have been tested using a petro
leum‐based preservative, or a preservative may
have been used for long‐term storage of the pump.
If flushing is required, do not do so until just before
installation; the test oil protects close‐tolerance
pump parts from corrosion.
Most cleaning solvents are toxic and
flammable. Use them only in a well ven
tilated area free from flame, sparks, and
excessive heat. Read and follow all pre
cautions printed on solvent containers.