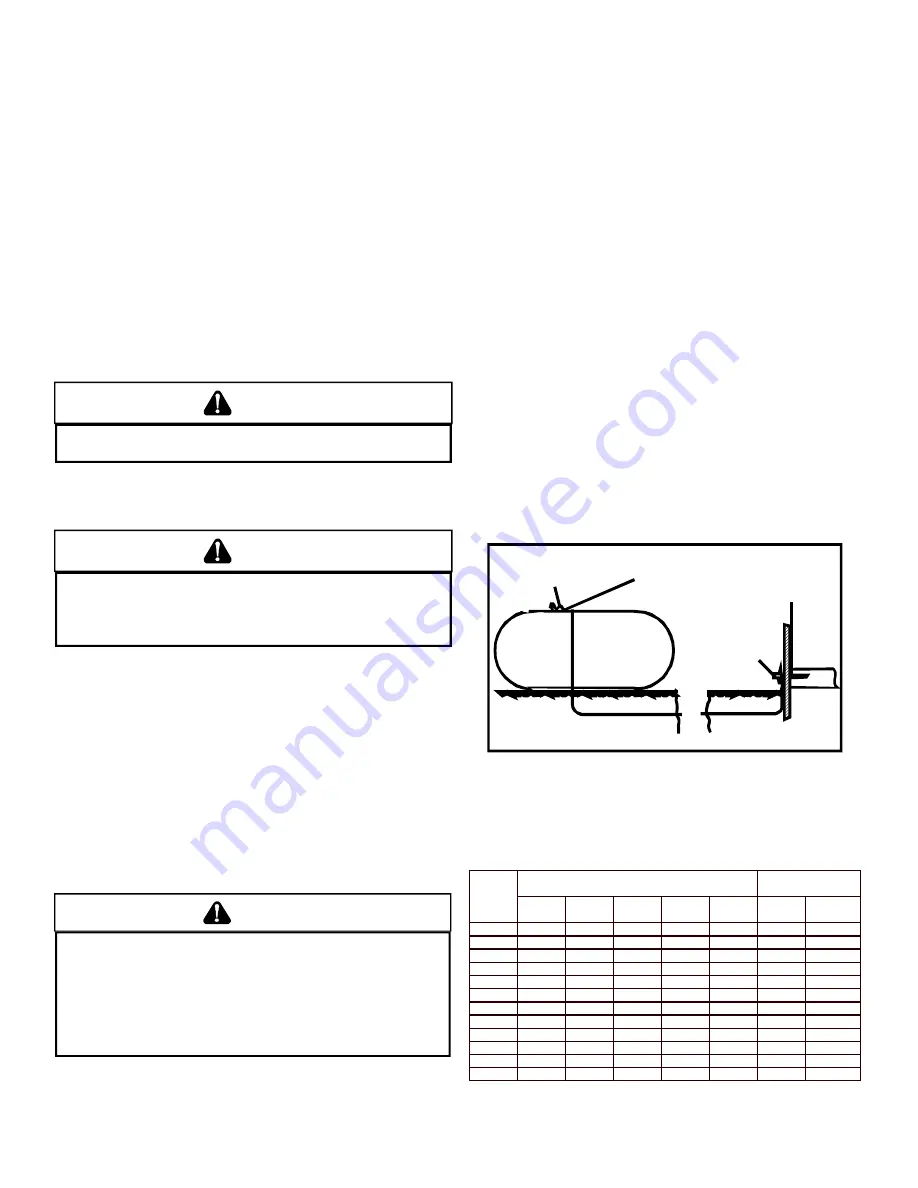
19
IO-242
5/04
C
OUNTERFLOW
I
NSTALLATIONS
When the gas piping enters through the left side of the furnace, the
installer must supply a straight pipe to reach the exterior of the
furnace.
A ground joint union, drip leg, and manual shutoff valve must also
be supplied by the installer. In some cases, the installer may also
need to supply a transition piece from 1/2" to another pipe size.
When the gas piping enters through the right side of the furnace,
the installer must supply the following fittings (starting at the gas
valve):
• 90 degree elbow.
• Close nipple.
• 90 degree elbow.
• Straight pipe to reach exterior of furnace.
G
AS
P
IPING
C
HECKS
Before placing unit in operation, leak test the unit and gas
connections.
WARNING
T
O AVOID THE POSSIBILITY OF EXPLOSION OR FIRE, NEVER USE A MATCH OR
OPEN FLAME TO TEST FOR LEAKS.
Check for leaks using an approved chloride-free soap and water
solution, an electronic combustible gas detector, or other approved
testing methods.
CAUTION
T
O PREVENT PROPERTY DAMAGE OR PERSONAL INJURY DUE TO FIRE, THE
FOLLOWING INSTRUCTIONS MUST BE PERFORMED REGARDING GAS
CONNECTIONS, PRESSURE TESTING, LOCATION OF SHUTOFF VALVE AND
INSTALLATION OF GAS PIPING.
NOTE:
Never exceed specified pressures for testing. Higher
pressure may damage the gas valve and cause subsequent
overfiring, resulting in heat exchanger failure.
Disconnect this unit and shutoff valve from the gas supply piping
system before pressure testing the supply piping system with
pressures in excess of 1/2 psig (3.48 kPa).
This unit must be isolated from the gas supply system by closing
its manual shutoff valve before pressure testing of gas supply piping
system with test pressures equal to or less than 1/2 psig (3.48
kPa).
P
ROPANE
G
AS
T
ANKS
AND
P
IPING
WARNING
I
F THE GAS FURNACE IS INSTALLED IN A BASEMENT, AN EXCAVATED
AREA OR A CONFINED SPACE, IT IS STRONGLY RECOMMENDED TO
CONTACT A PROPANE SUPPLIER TO INSTALL A GAS DETECTING
WARNING DEVICE IN CASE OF A GAS LEAK.
•
S
INCE PROPANE GAS IS HEAVIER THAN AIR, ANY LEAKING GAS CAN
SETTLE IN ANY LOW AREAS OR CONFINED SPACES.
•
P
ROPANE GAS ODORANT MAY FADE, MAKING THE GAS UNDETECTABLE
EXCEPT WITH A W ARNING DEVICE.
A gas detecting warning system is the only reliable way to detect a
propane gas leak. Rust can reduce the level of odorant in propane
gas. Do not rely on your sense of smell. Contact a local propane
gas supplier about installing a gas detecting warning system. If
the presence of gas is suspected, follow the instructions on Page
4 of this manual.
All propane gas equipment must conform to the safety standards
of the National Board of Fire Underwriters, NBFU Manual 58.
For satisfactory operation, propane gas pressure must be 11 inch
WC at the furnace manifold with all gas appliances in operation.
Maintaining proper gas pressure depends on three main factors:
1. Vaporization rate, depending on temperature of the liquid,
and “wetted surface” area of the container or containers.
2. Proper pressure regulation. (Two-stage regulation is
recommended for both cost and efficiency).
3. Pressure drop in lines between regulators, and between
second stage regulator and the appliance. Pipe size will
depend on length of pipe run and total load of all appliances.
Complete information regarding tank sizing for vaporization,
recommended regulator settings, and pipe sizing is available from
most regulator manufacturers and propane gas suppliers.
Since propane gas will quickly dissolve white lead and most
standard commercial compounds, special pipe dope must be used.
Shellac-based compounds resistant to the actions of liquefied
petroleum gases such as Gasolac
®
, Stalactic
®
, Clyde’s
®
or John
Crane
®
are satisfactory.
Refer to the following illustration for typical propane gas installations
and piping.
200 PSIG
Maximum
5 to 15 PSIG
(20 PSIG Max.)
Continuous
11" W.C.
Second Stage
Regulator
First Stage
Regulator
Propane Gas Installation (Typ.)
P
ROPANE
G
AS
P
IPING
C
HARTS
Sizing Between First and Second Stage Regulator*
Maximum Propane Capacities listed are based on 2 psig pressure drop at 10 psig setting.
Capacities in 1,000 BTU/hour.
Pipe or
Nominal Pipe Size
Tubing
Tubing Size, O.D. Type L
Schedule 40
Length,
3/8"
1/2"
5/8"
3/4"
7/8"
1/2"
3/4"
Feet
10
730
1,700
3,200
5,300
8,300
3,200
7,500
20
500
1,100
2,200
3,700
5,800
2,200
4,200
30
400
920
2,000
2,900
4,700
1,800
4,000
40
370
850
1,700
2,700
4,100
1,600
3,700
50
330
770
1,500
2,400
3,700
1,500
3,400
60
300
700
1,300
2,200
3,300
1,300
3,100
80
260
610
1,200
1,900
2,900
1,200
2,600
100
220
540
1,000
1,700
2,600
1,000
2,300
125
200
490
900
1,400
2,300
900
2,100
150
190
430
830
1,300
2,100
830
1,900
175
170
400
780
1,200
1,900
770
1,700
200
160
380
730
1,100
1,800
720
1,500
To convert to capacities at 15 psig settings - multiply by 1.130
To convert to capacities at 5 psig settings - multiply by 0.879